現場改善会計論(Gemba Kaizen Costing, 以下GKC)をさまざまな斬り口でみてきました。どこを探しても、腑に落ちる「理論」は見当たりません。で、視点を換えて管理会計の歴史をたどってみたのが前回。わかったことは、100年以上前の工場でならGKCが使えるかもしれない、ということでした。より具体的なイメージで言えば、単一製品を、手待ちが生じないように工程間にはたっぷりと仕掛を置き、簡単な道具を使って手作業でつくっている工場。もちろん今だって、似たような生産環境はありますが、あったとしても内職的な請負や低賃金国など、でしょう。
市場の需要変動に追従しながら生産リソース(人、機械設備、、)を効率よく運用しなければならない昨今の生産環境・・多品種少量、変種変量生産では、GKCはまったく使えません。
今回は、どのような考えをベースにしてGKCの研究が進められてきたのか、下記の三つの研究課題に関する論文、研究実績報告などから読み解いてみたいと思います。先ず、GKCの初めの頃の論文と思われる
- 生産現場の改善と原価計算−改善効果の見える化−
(以下、生産現場の改善と原価計算)
柊 紫乃、 上總 康行 原価計算研究 2016
メルコ学術振興財団2012年度研究助成
と、下記の日本学術振興会科研費の支援を受けた2つの研究テーマの研究実績報告をみてみたいと思います。
- グローバル競争に直面する日本製造企業の組織能力を進化させる現場改善会計の研究
代表者 柊 紫乃 愛知工業大学, 経営学部, 教授
分担者 上總 康行 福井県立大学, 地域経済研究所, 研究員
期間 (年度) 2017/04~2021/3、課題ステータス;完了 (2020年度)
配分額 4,420,000円 - 現場改善会計の工場導入実験とその成果に基づく理論構築に関する研究
代表者 柊 紫乃 愛知工業大学, 経営学部, 教授
分担者 上總 康行 福井県立大学, 地域経済研究所, 客員研究員
期間 (年度) 2022/04~2025/3
配分額 3,250,000円
2012年度~2024年度の13年間にわたる三つの研究課題。いずれもGKCをテーマにしています。それぞれの研究実績からGKCの形成過程を追ってみます。
1、「生産現場の改善と原価計算」の要点
この研究テーマからはGKCの初期の考え方を読み取ることができるのではないかと思われます。要点をまとめてみます。
(以下、論文、研究実績報告等からの引用部分は“緑字”で表示します。詳細については、出典元原文をご参照ください。)
1.1 研究課題の要点
[課題の背景];現場改善効果を成長期は原価低減、収益増として把握できたが、停滞期に入り、捉えられなくなった。
[解決策];「機会損失」概念を導入することにより、いかなる経済環境でも改善効果を捉えられるように、新しい原価計算方法を考察した。
[先行研究];改善効果の貨幣的測定を目指した数少ない事例の中に、千住教授・伏見教授が1960年代に提唱した「経済性分析」で「改善活動の経済性評価」を取り上げている。但し、「機会費用として次年度の検討資料に利用できる」とはしているが、「手余りの際の効果金額を計算してはならない」としている。
岡本教授は、2000年に、設備管理と標準原価計算を統合する新たな差異分析を提案し、原価改善の経済的効果測定についても具体的な計算例を示した。しかし停滞期・減退期の経済環境下で発生する余剰生産能力を活用するという積極性はあまりない。千住教授・伏見教授の主張と同様に、これも事後管理を前提としている。
1987 年の「レレバンス・ロスト」(Johnson & Kaplan)が指摘した、全部原価計算における製造間接費配賦の歪みの解決策として、Kaplan はCooper とともに製造間接費配賦の精緻化を意図した「活動基準原価計算(ABC)」とマネジメントに応用した「活動基準管理(ABM)」を提唱した。ABM は活動を付加価値と非付加価値に分け、ムダを削減する点において現場改善会計に近い。しかし,そこに機会損失の測定と活用は明示されていない。
[先行研究評価・結論];以上,主要な先行研究を検討した限りでは、千住教授・伏見教授および岡本教授の現場改善効果を貨幣的に測定するという研究に関心が向く。しかし、それらの研究は、総じて右肩上がりの経済成長による 販売量増大=生産量増大 を前提としている。また、標準原価計算にしてもABC/ABMにしても、一定の改良は認められるが、根本的な対策にはなっていない。
さらに、いずれもが事後管理に焦点があてられており、停滞期・減退期に特に必要である事前管理については十分な考察が行われていない。
[現場改善効果を測定する原価計算例];図1に示すような4工程から成る生産ラインで、生産品種は1 種類。1 日ごとに出荷予定数を当日中に完成させる。日の終わりにまとめて出荷し翌日に在庫は残さない。各工程の処理時間は工程ごと一定でバラツキはなし。
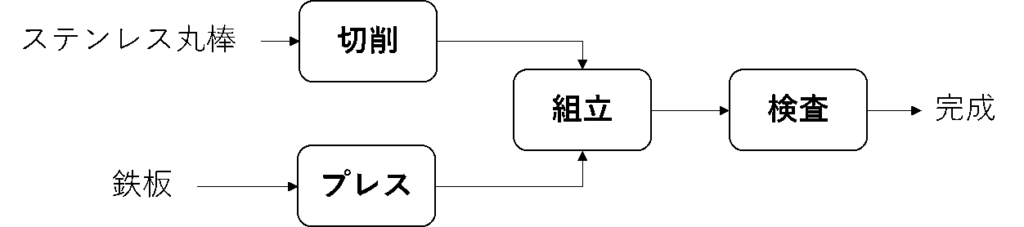
図1 原価計算事例の生産ラインモデル
改善効果の金額評価方法を表1で例示している。金額への変換は、
改善効果金額=直接作業短縮時間×賃率
で、行っている。
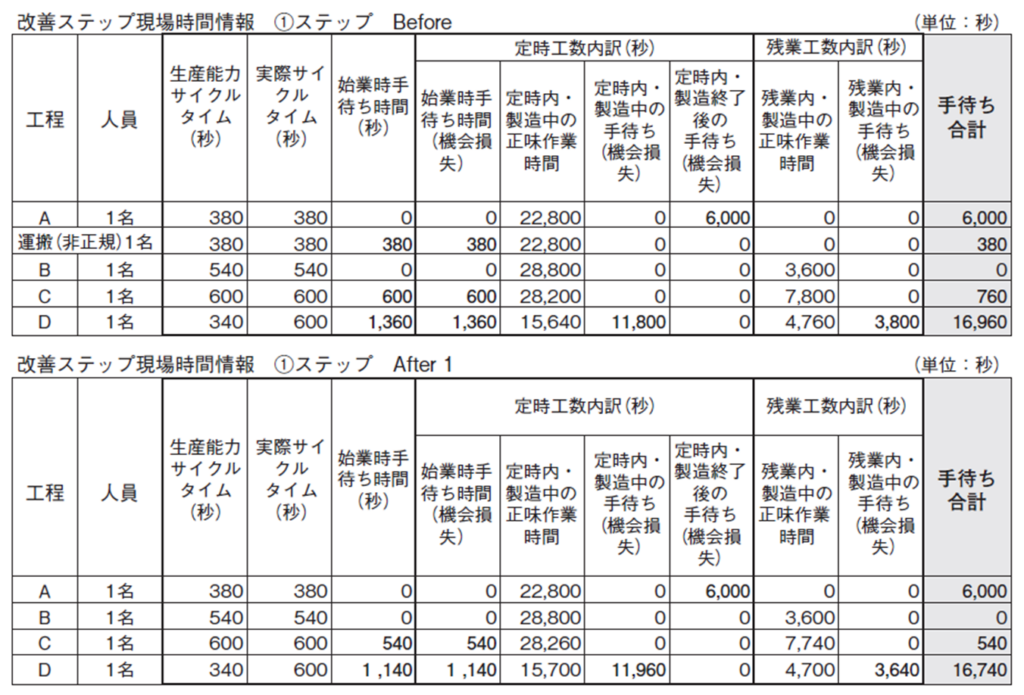
表1 出典;生産現場の改善と原価計算
1.2 研究実績の論評
ここで設定している生産条件をもう一度確認しておきます。
・生産計画固定(予め生産数量が決められている)
・製品は1種類
・仕掛在庫なし(当日生産・当日出荷)
・作業時間固定
このような生産条件があるとすれば、前回申し上げたことですが、19世紀の家内制手工業、問屋制手工業、工場制手工業の時代、つまり100年以上前のこと。これは、GKC初期の論文ですので、簡単な条件から始めることは理解できます。問題は、これ以降、日本学術振興会の科研費を使った研究でどのように理論構築していったのか。その研究実績報告で確かめてみたいと思います。
2、日本学術振興会の科研費を使った研究課題
日本学術振興会の科研費を使った2つの研究実績報告をみてみます。
*グローバル競争に直面する日本製造企業の組織能力を進化させる現場改善会計の研究 研究期間;2017年度~2020年度
*「現場改善会計の工場導入実験とその成果に基づく理論構築に関する研究」
研究期間;2022年度~2024年度
2.1 研究実績報告[2017年度~2020年度]の要点まとめ
時系列的に研究実績報告の要点をまとめてみます。先ず、研究目的を確認しておきます。
[GKCの目的]
製造現場で行われる改善効果の金額測定法開発及び、その会計的論理体系の構築。
最大の関心事は、どのような論理展開でこの目的を達成しようとしているのか、あるいは、したのかです。科研費研究実績報告からその痕跡をたどってみます。
[2017年度実績]
ほぼ当初計画通りに進捗。具体的には以下の3点。
①理論研究として生産能力に焦点をあて、製造間接費について詳細に検討した。その成果を学会、大学等で発表。
②海外研究者と知見を交換。その成果を学術財団のペーパーで公表。
③理論の実践的検証として、外資系製造企業との共同研究を開始。
[2018年度実績]
主な進捗は以下の3点。
①生産能力展開図に沿って金額計算ロジックをほぼ構築した。その成果の一部は書籍に掲載。また国内研究者との共同研究・論文公表に参加。
②海外研究者との知見交換として、海外開催会議で成果報告を行った。
③外資系製造企業との共同研究はほぼ予定通り進展。また、国内製造企業数社と知見交換と議論を行った。
[2019年度実績]
計算構造についての研究成果を学会で報告。また、複数の製造企業との共同研究も予定通り進展した。研究成果を書籍として発刊準備中。また、3年間にわたるGKC理論研究の成果をふまえ、より実践的な企業実務への応用研究に取り組んでいく。すでに、2019年度後半より、複数企業でのパイロット導入が始まっており、これらを実践的に進めることにより、さらなる理論の進化を目指していく。
[2020年度実績]
計算構造についての研究成果論文を投稿、査読が進行中(2021年度現在)。また、複数の製造企業との共同研究も予定通り進展している。
[研究成果の学術的意義や社会的意義]
本研究では、現場改善効果金額測定の困難さという問題を摘出し、主として日本企業の現場および会計担当者への調査研究を経て、原価計算構造と改善効果との因果関係を究明した。さらに、計算構造のより詳細な検討と体系化を試みた点に学術的意義がある。また、本研究は管理会計分野の理論研究と、その応用研究および会計処方研究を同時並行的に進めてきた。今後の実務適用につながる基礎理論を構築し得た点に社会的意義がある。
2.2 研究実績報告[2022年度~2023年度]の要点まとめ
続いて、2022年度~2024年度に行われた研究実績報告をみてみます。
[2022年度研究開始に当たっての目的確認]
本研究は、藤本隆宏教授の「設計情報転写論」および、柊紫乃・上總康行のGKCを理論的基盤としながら、従前より日本の製造業における強みとされてきた改善実践やトヨタ生産システム(以下TPS)について、会計的視点から理論化することを目的とする。また、理論化と同時に、様々な業種業態に適合可能な実務導入の方法論を創出する。GKCのこれまでの基礎理論研究に基づいた、「学際的・実践的・応用研究」である。
[2022年度研究実績]
2022年度の研究目的である「GKC適用による企業における実現・未実現の改善効果の金額計算方法」について、企業におけるアクション・リサーチを継続的に実施した。その結果、かなりの精度で、実現・未実現の改善効果測定が可能となる基本の原価管理帳票が完成した。
また、これらの事例および、その基礎となったGKCの基礎理論について、国内外で報告を行った。また、これらの事例および、その基礎となったGKCの基礎理論について、以下の国内外で報告。
① 第6回国際会議 P&OM Nara 2022にてGKCについての学術発表。牧誠財団の英文ディスカッションペーパーとして公表。
②類似研究の多いLean Accounting Summitにて成果発表。
③ 日本管理会計学会の統一論題に関する報告およびパネルディスカッションに登壇、同学会誌「管理会計学」で公表。
柊・上總「現場改善効果の類型化―会計的視点からの考察―」が、2022年度 日本管理会計学会・学会賞(論文賞)を受賞した。
GKCに興味をもち、検討を希望される企業がいるので、それらの可能性を模索していく。また、海外の研究者(デンマーク、アメリカ)が、本研究の基礎理論に非常に興味を示しており、国際的共同研究につながる可能性がでてきている。今後も積極的に成果を国内外に報告していく。
[2023年度研究実績]
前年度より継続して、実際に改善中の企業におけるアクション・リサーチを実施した。それ以外にもリサーチが進んできており、最終2024年度の学会報告に繋がる見込みである。また、GKCの基礎理論についての成果をまとめ、書籍として 上總康行・柊紫乃『現場改善会計論:改善効果の見える化』中央経済社 を公刊した(2023年12月)。当該書籍は研究者だけでなく実務家からも注目されており、企業からの社内講演等依頼がきている。英訳版公刊も準備中。
また、新たにリサーチをしている2社のうち、自動車部品・医療系部品を製造する企業との課題検討も順調に推移している。最終年度である2024年度は、3社との間で継続的アクション・リサーチの実施を予定しており、順調に実践的研究が続いている。
3、現場改善会計論(GKC)の科研費研究実績報告の総括
3.1 研究実績報告のまとめおよび論評
どのようなことを行ったのか、ポイントをまとめてみると次のようになります。
[目的]
- 製造現場で行われる改善効果の金額測定法開発及び、その会計的論理体系の構築。
- トヨタ生産システム(TPS)の会計的視点からの理論化(2022年度追加)
- 様々な業種・業態へのGKC導入方法の創出(2022年度追加)
[研究実績]
*研究内容
➡管理会計分野の理論研究および応用研究
➡会計処理方法の研究
*研究成果
➡実務への適用につながる基礎理論を構築した
➡原価計算構造と改善効果の因果関係を究明した
*知見交換・・・研究者、企業、大学等と
*共同研究・・・研究者、企業、大学等と
*発表・公表・報告
➡学会、カンファレンス、専門誌、書籍等
*アクション・リサーチ
[目的達成への論理展開]
実績報告の大部分は知見交換、共同研究、発表・公表・報告、アクション・リサーチ等で占められ、研究成果の具体的内容は不明。目標達成への論理展開の説明も説得力に欠けます。
[目的達成度]
どの程度目標に近づいているか、を判断する記述はありません。研究成果として次の2点を挙げています。
*実務への適用につながる基礎理論を構築した。
*原価計算構造と改善効果の因果関係を究明した。
しかしいずれも、具体的な説明はなく、目的達成度を判断することはできません。
3.2 目的達成度を知る手がかり
先に示したGKC研究当初(2016年)の「生産現場の改善と原価計算」にある[現場改善効果を測定する原価計算例]がその後どのように改善されたか、研究目的達成度を知る手がかりになるのではないか、と思います。
改善後の計算例として2022年度 日本管理会計学会・学会賞(論文賞)を受賞した「現場改善効果の類型化―会計的視点からの考察―」(以下、現場改善効果の類型化)の「改善効果の計算例」を比べてみます。研究が行われていた6~7年間に原価計算方法がどのように改良されたかがわかります。
「現場改善効果の類型化」の中の「ムダの排除による改善効果の金額測定」をみてみます。ポイントは、
*「B製品のみを生産」
*「加工費に含まれる機械の減価償却費等も直接作業時間と同様の割合で改善されるとし、改善後の正味作業時間比率を100%と想定する」
という条件で計算していることです。
―以下、引用―
(改善事例A)
A 工場では,B 製品のみを生産、製品在庫はなし、販売単価3,200 円で出荷している。
<改善前> 生産:100 個/日
原価:材料費(変動費)1,100 円/個、加工費(固定費)90,000 円/日
<改善後> 生産:120 個/日 ※生産能力増大
原価:材料費(変動費)1,000 円/個 ※原価低減、加工費(固定費)90,000 円/日
なお、加工費90,000 円は直接作業時間に応じて製品に分配されるが、単純化のため、加工費に含まれる機械の減価償却費等も直接作業時間と同様の割合で改善されるとし、実現可能性は別として改善後の正味作業時間比率を100%と想定する。
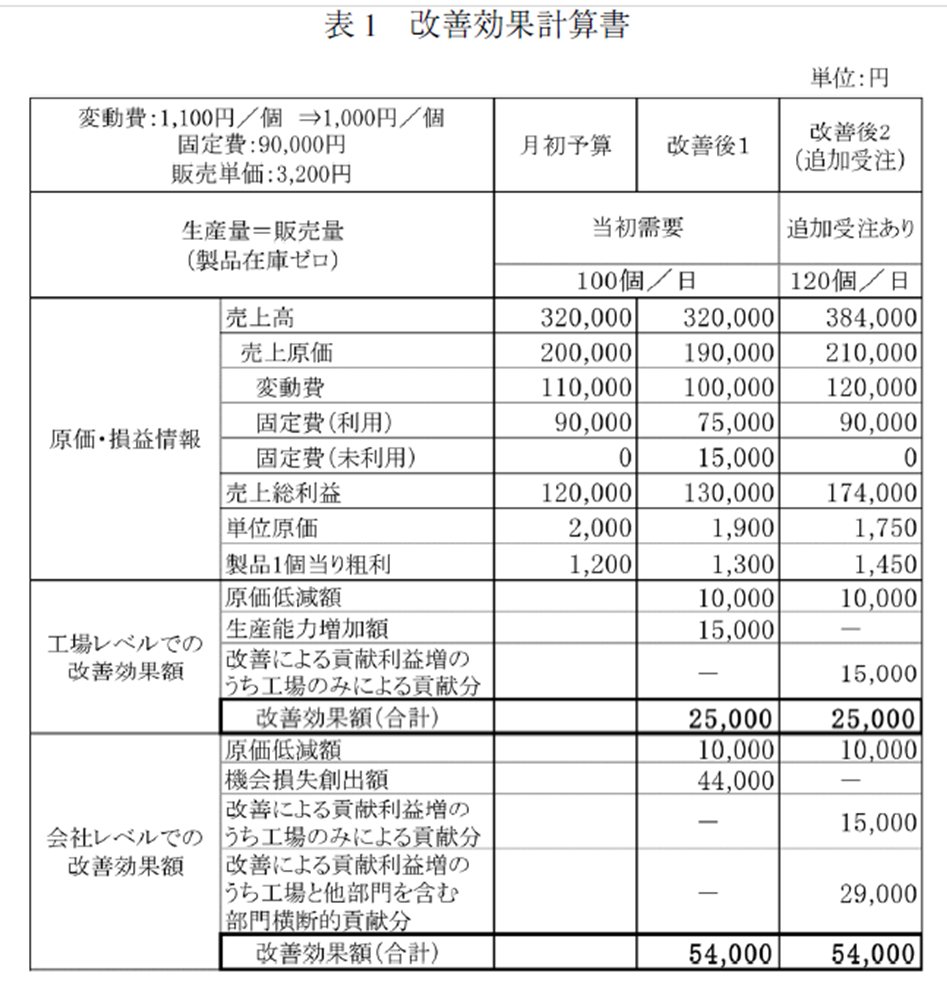
表2 改善効果計算例(出典;現場改善効果の類型化)
条件に「単純化のため」とか「実現可能性は別として」とか、実務を指向した計算事例にはふさわしくない但し書きがあり、結局、2016年の[現場改善効果を測定する原価計算例]と基本条件はほぼ同じではないか、と考えられます。
つまり、2022年の「改善効果の金額評価方法」は2016年のそれと、ほぼ同じ。その間の研究成果はまったく認められない、ということになります。「実務への適用につながる基礎理論を構築した」「原価計算構造と改善効果の因果関係を究明した」との説明に強烈な違和感をおぼえます。計算方法はまったく昔のまま。なんの進歩もみられません。
4、現場改善会計のねらいは、パラダイム・シフトだったのか
GKCの理論体系がどのようにして形成されたのか、10年余りにわたる関連する研究実績報告を中心に調べてみました。
科研費の研究実績報告を読むと、知見交換、共同研究、学会発表、論文投稿、書籍出版、英語版出版準備、パイロット導入、アクション・リサーチ・・・と華々しい研究活動が行われていたように感じられます。しかし中身は“カラッポ”。
767万円もの科研費を使って、研究の成果は虚無。いや、虚偽かな。どうしてこうなったのでしょうか。過失、誤謬、無能、欲望、バイアス、詐欺・・・背後には何かがある・・・。外からみてもわかりません、、、。
4.1 論理展開を手掛かりに
GKCの「生産現場の改善と原価計算」の先行事例調査では、「改善効果の金額測定」について次のように説明しています。
- (1960年代)千住教授・伏見教授が「手余りの際の効果金額を計算してはならない」、利用できるとしても「次年度の検討資料として」である。
- (1987年)「レレバンス・ロスト」(Johnson & Kaplan)が指摘した製造間接費配賦の歪みの解決策であるABC/ ABMも機会損失の測定と活用は明示されていない。
- (2000年)岡本教授は、原価改善の新たな差異分析計算例を示したが余剰生産能力を活用するという積極性はあまりない。
少なくても半世紀以上前から、GKCの目的である「改善効果の金額測定」に対しては、否定的な見解が多い、ということです。
で、普通なら、「改善効果の金額測定」がうまく行かない理由、原因などを調べて、その原因を排除する策をみつけ出す、というようなアプローチをとる。しかしGKCでは、これまでの流れにとらわれない、まったく新しい概念を取り入れました。
科学の進歩を顧みると、地動説から天動説、大航海から宇宙探査、古典物理学から相対性理論・量子論などのように、先行知見の延長線ではない、むしろ先人の知見を否定した新しいパラダイムへの転換が起きています。GKCがとったアプローチも、パラダイムシフト的転換を狙っていたのではないか、と思われます。
GKCが採用した新しいパラダイムが、上總 康行教授の「機会損失論」であり、藤本隆宏教授の「設計情報転写論」であり、そしてTPSだ、と解釈すると、まぁ、一応は納得できます。「GKCは、管理会計・生産現場管理の学際的領域で、パラダイムシフト的大発見を狙った」のではないか、という仮説に留意しながら、GKCの問題解決過程をみてみたいと思います。
4.2 GKCの論理展開;3つのポイント
「現場改善効果の類型化」に次のような説明があります。
「現場改善効果を金額測定できる原価計算手法の確立」としては、以下の3つが挙げられる。
① 生産システムに投入された経営資源(生産)を、良品生産に貢献するか否かによって区分する。それにより改善対象となる「ムダ」を会計的視点から定義する。
② 定義されたムダが生産プロセスの中のどの時点で発生するかについて、GKC の「生産能力展開図」を使って具体的に特定する。
③ それらのムダが排除され、生産能力が増大した場合にあらわれる会計的効果について、計算方法を検討し、変動要因を明示し類型化する。なお、経営に関わる様々な資源のうち、生産に関わる資源を「経営資源(生産)」と表記。
先ず①ですが、
経営資源(インプット)➡[生産システム]➡良品(アウトプット)
というように抽象化しています。そして、「良品生産に貢献しない経営資源をムダとして会計的に定義する」としています。また、
経営資源 = 販売品 + ムダ
の式があります。同じ経営資源でムダを減らせば販売品の価値が上がる、ということでしょう。このムダの説明に7つのムダ等々、おなじみのトヨタ語が出てきます。TPSをベースにムダを捉えています。ここで留意しておきたいことは、計算のロジックは単純な“一次関数の加減乗除”だ、ということです。“線形モデル” という言い方もあると思います。
そして②、「ムダが生産プロセスの中のどの時点で発生するかについて、GKC の「生産能力展開図」を使って具体的に特定する」とあります。参考に図3に「生産能力展開図」を本論文より引用します。これも生産能力が単純な“一次関数の加減乗除”、“線形モデル” で表されています。
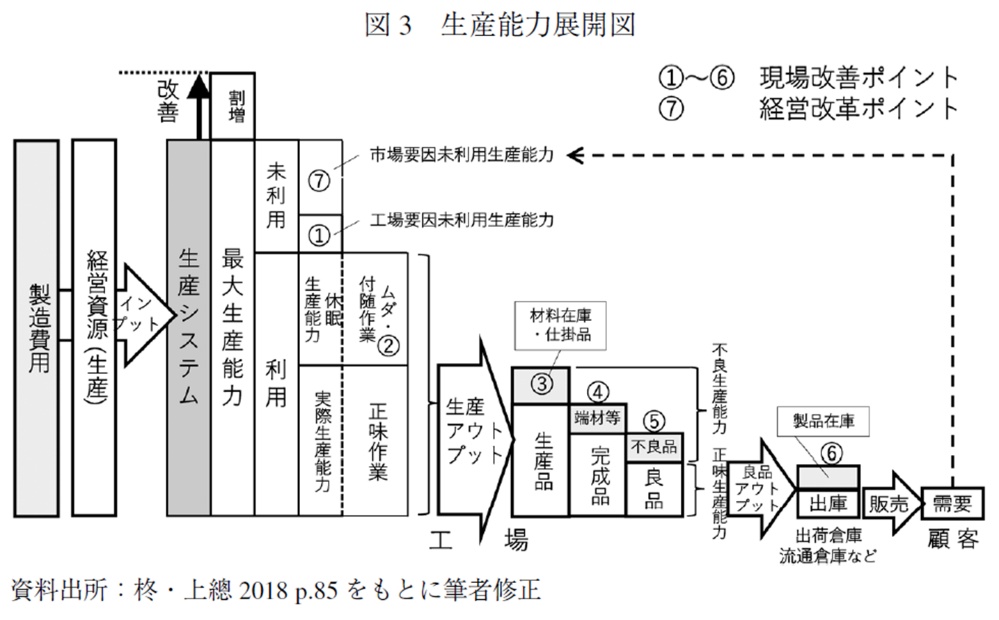
図3 本論文より引用;「生産能力展開図」
さらに③ですが、「それらのムダが排除され、生産能力が増大した場合にあらわれる会計的効果について、計算方法を検討し」とありますが、ここでの計算方法とは、やはり“一次関数の加減乗除”、“線形モデル” である、と解釈できます。
ここでいう“一次関数の加減乗除”、“線形モデル” とは、何かが増えたり減ったりすると別の何かが減ったり増えたりする直線的な関係(比例関係)にあるモデルです。視覚的に言えばある一瞬をとらえた“写真”。それで前後の動きは推測できますが、不規則な動きがわかる動画ではありません。“静止画”です。
GKCが依拠した理論と考え方は「機会損失論」と「設計情報転写論」それに「TPS」です。
「機会損失論」の基本概念は次式で説明されています。
改善効果=原価低減額 + 機会損失額
この式、経営資源 = 販売品 + ムダ と似てます。線形モデルで、静止画的です。
「設計情報転写論」は、ちょっと、わかりにくいのですが、図4に参照図を示します。
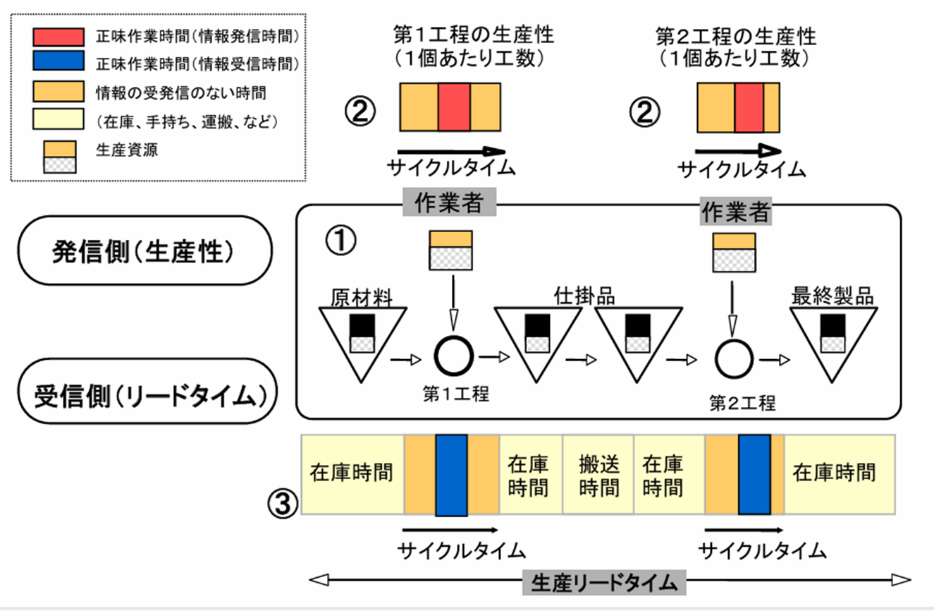
図4 設計情報転写の説明 出典;経営第6回 現代日本のものづくり経営学(2011/1)
ピンクの設計情報が工程で作業者によって材料に「転写」され青色となって、次工程に流れて行く、という説明です。この図は、同じものをたくさんつくる場合をイメージしているように思われます。例えば、ラインバランスがほぼ100%で一定のサイクルタイムで同期生産が行われているTPSとか、、。一般の変種変量受注生産では、こうはなりません。流れる製品によってサイクルタイムが違ってきますので、工程は手待ちになったり、その前に仕掛が滞留したり、それを予測することはほぼ不可能です。一般の生産現場を対象としているGKCとしては、大量見込生産も変種変量受注生産もひっくるめて対象にしているはずです。そう考えると、4図はある一瞬をとらえた “静止画” 的感覚で生産システムを捉えているように思われます。。
では、TPSをベースにした “ムダ” はどうでしょうか。図5で説明していますのでムダは加減算の線形モデルで、静止画的です。
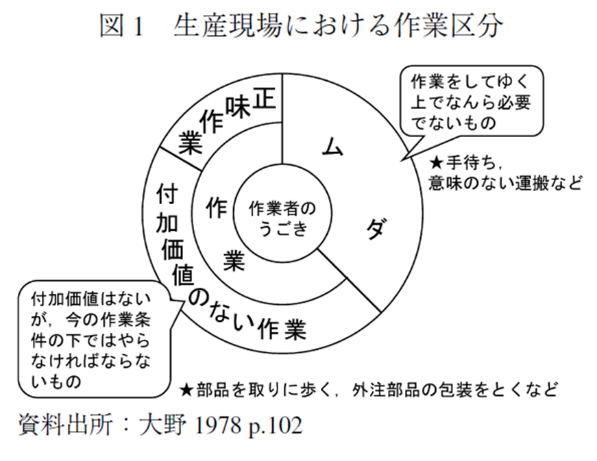
図5 ムダの説明
まとめますと、
GKCが依拠した「機会損失論」、「設計情報転写論」、「TPS」は、生産システムを
線形モデル
一次関数の加減乗除
という概念で捉えている、と思われます。
5、GKCが捨象した生産ラインの物理特性
GKCが依拠した「機会損失論」、「設計情報転写論」、「TPS」のいずれもが「線形モデル」という概念で生産システムを捉えているように思われます。現実の生産システムを線形モデルで捉えたことにより、GKCの論理展開にどのような影響を与えたのでしょうか。読み解くキーワードが4つ、あります。
- ボトルネック現象;生産ラインの能力は一番能力の低い工程の能力で決まる
- 待ち行列現象:工程の処理時間の変動とその工程にワーク(被処理物)が到着する時間間隔の変動との関係で生じる「工程手待ち(手空き)」と「ワークの待ち時間」発生現象
- トヨタ生産システムの特徴;Just In Time
- 個別製品原価計算における製造間接費配賦の関連性・妥当性喪失
5.1 ボトルネック現象
生産ラインの能力は、一番能力の低い工程(ボトルネック工程)の能力で決まる。ボトルネック工程で生産数量が制約されている生産ラインで、非ボトルネック工程を改善して時間を短縮しても、生産能力は高まらず、生産数量は増えない。実際の生産ラインでは、特に多品種、変種変量受注生産では、ボトルネックは動き回ることが多くなり、改善で作業時間を短縮ができたとしてもそれが余剰生産能力になるかどうかは、わからない(ならない場合が多い)。従って多くの場合、改善による作業時間短縮=手余り時間発生=余剰能力発生➡機会損失、とはならない。
この現象については20世紀初め、テーラーの科学的管理法等で盛んに研究され、製造業界ではよく知られた現象である。
5.2 待ち行列現象
この現象が、生産ラインでも重要であることが知られるようになったのは1990年以降である。どのような特性かは“ものづくり徒然草”のNo.110やNo.111を参照。簡単に言えば、工程の稼働率が高くなるに従い、その前で仕掛として待つ時間が指数関数的に長くなる、という現象である。図6参照。多品種少量、変種変量受注生産ではワークの到着間隔や工程処理時間のバラツキが大きくなりやすく、生産リードタイムの長期化、仕掛在庫の増大など、生産管理上重要な問題となる。改善により発生した手待ち時間は、
手待ち発生➡稼働率低下➡待ち時間短縮➡リードタイム短縮➡短納期受注獲得
のように納期短縮による受注獲得力の増強にも使えるのである。
リソース(作業者、機械設備)の稼働率と生産リードタイムはトレードオフの関係にあり、生産数量を増やして収益を上げるか、待ち時間の短い領域で生産リードタイムを短縮して受注獲得を有利にするか等は、企業それぞれの戦略による。
5.3 トヨタ生産システムの特徴を確認
「GKCはトヨタ生産システム(以下、TPS)の実践知・・・に依拠する」、と説明されている。GKCの研究実績を総括するにあたり、生産システムとしてTPSはどのような特徴があるのか、理解しておく必要がある。
TPSの特徴をボトルネック現象、待ち行列現象、間接費配賦問題の視点で分析してみる。詳細は別紙に穣ことにして、ここでは基本的なことを簡単にまとめる。
TPSの最大の特徴は、Just In Time。各工程で作業が開始される時刻にワーク(被処理物)が到着する、というイメージ。このような生産ラインを実現するうえで、密接な関係にある生産ラインの物理特性がボトルネック現象と待ち行列現象である。図6を参照。
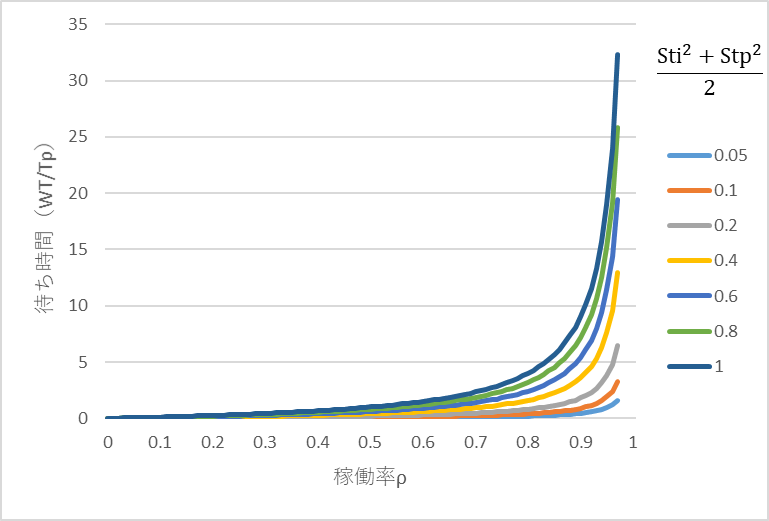
図6 稼働率v.s.待ち時間WT
工程で作業が終わらないうちに次のワークが到着したら、そのワークは待たなければならない。待ち時間が発生する。工程での作業が終わってもワークが到着しなければ、工程は手待ち(手空き)になる。前者はワークの待ち時間(仕掛の滞留)が発生、後者は手待ちが発生(稼働率が低下)する。工程処理時間=ワーク到着時間間隔 のとき、待ち時間がゼロ、手待ちがゼロ。つまり、工程間仕掛ゼロ、稼働率100%となる。これがJust In Timeが狙う理想状態である。
Just In Time を成立させる条件をまとめると、次のようになる。
*工程処理時間(平均);Tp、*その変動係数;Stp
*ワークの到着時間間隔(平均);Ti、*その変動係数;Sti
*稼働率;ρ ρ=Tp/Ti
*待ち時間(平均);WT

[TPSの成立条件]
- ρを100%にするため ➡ Tp=Ti
- WTをゼロにするため ➡ Sti=0、Stp=0
Tp=Tiを実現する方法のポイントは、全ての工程の処理時間(能力)を揃える(ラインバランス100%) ➡平準化、サイクルタイムによる同期生産
Sti、Stpをゼロにする方法として、各工程の処理時間のバラツキをなくす
➡標準作業時間の維持管理
この条件を満たすためには、生産計画を確定した見込生産でなければならない。多品種少量、変種変量の受注生産でTPSは機能しない。多品種少量、変種変量受注生産が多い一般の生産ラインでは、稼働率と生産リードタイムのトレードオフをできるだけ有利な動作点で生産するように管理する必要がある。そのためには、ボトルネック現象と待ち行列現象を正しく理解しておく必要がある。
5.4 製造間接費の配賦問題
製造間接費の配賦問題は、同じ生産ライン(工場、企業、)で生産品種が複数種以上になると顕在化する。昨今の多品種少量、変種変量生産ではこの問題を避けることはできない。単一製品を量産している工場であれば、総製造費を生産数で割れば一個の原価を計算できるが、複数品種になると各品種と間接費の関係を一義的に決めることができなくなり、原価の歪みが生じる。20世紀に入って、多品種化が進み、製造原価に占める間接費の比率がますます増大し、個別製品原価の妥当性・関連性の低下が進んでいる。
6、現実の生産システムとGKCが設定した生産システムの前提条件
6.1 GKCが設定した生産システムの前提条件
GKCの目的達成のために採ったアプローチは、次の3ステップ。
① 良品生産に貢献するか否かによって、「ムダ」を会計的視点で定義する。
② ムダが生産プロセスの中でいつ発生するか、「生産能力展開図」を使って特定する。
③ ムダが排除され、生産能力が増大した場合にあらわれる会計的効果の計算方法を検討する。
GKCが生産システムを分析するときに設定した条件は、生産システムは、線形モデルであるとしています。
なぜ、GKCは生産システムを線形モデルで分析できる、と考えたのでしょうか。
GKCが依拠した「機会損失論」、「設計情報転写論」が線形モデルをベースにした理論である。また、TPSは多くの生産現場で、生産システムの模範として受け入れられてきた。Just In Timeが実現した現場は線形モデルをベースにした簡潔的な管理可能となる。ムダも含めて、TPSの解説の大部分は線形モデルで説明できる。
このような背景から、実際の生産システムのほとんどが線形モデルで取り扱うことができる、と考えたのではないか。
6.2 実際の生産システムは非線形特性;捨象により線形モデルに変身
実際の生産システムは、「ボトルネック現象」や「待ち行列現象」で代表される非線形の物理特性を持っています。基本的にはどのような生産ラインでも必ず存在する特性です。その特性を目立たない程度まで抑制しているのがTPS。但し、TPS成立のためには、ある程度以上の量産、生産計画固定、見込生産などの条件が必須です。多品種少量、変種変量受注生産では、非線形特性を避けることはできません。
法則とか定理とか○○論とかは、ほとんどすべて、抽象化されています。抽象化とは、特定の対象から重要な要素を抜き出し、他の要素を無視する思考の手法です。物理特性も例外ではありません。「機会損失論」も「設計情報転写論」も抽象化されています。抽象化した要素は、
「機会損失論」➡需要がないとき改善効果は機会損失となる
「設計情報転写論」➡設計情報が媒体(材料)に転写され商品となる
となります。
抽象化は捨象(他の要素を無視)をともないます。「機会損失論」、「設計情報転写論」が捨象した要素は何か。それは“物理現象”です。具体的に言えば、「ボトルネック現象」と「待ち行列現象」です。どちらも非線形特性です。これを無視(捨象)した「機会損失論」も「設計情報転写論」も非線形特性を扱えなくなりました。つまり、「ボトルネック現象」も「待ち行列現象」も扱えなくなってしまいました。
現実の生産システムを線形モデルだとして扱えば、例えば、改善で作業時間を短縮したとき、その工程がボトルネックか非ボトルネックかの区別もなしに、即、余剰能力発生となるわけです。稼働率が高くなると待ち時間が急伸して生産リードタイムが指数関数的に長くなることも無視され、実現性のない生産能力が余剰能力として計算されます。リソース(人、機械設備等)の余裕を機会損失と計算し、短納期の受注チャンスを見逃すことにもなります。
7、研究手法も含めて、GKC関連論文は、すべて“NULL”である
GKCの論理展開を分析するとき使ったキーワードはGKCを論評するときも使えそうです。
- 製造間接費配賦問題
- ボトルネック現象
- 待ち行列現象
- トヨタ生産システムの線形モデル化
これらのキーワードはGKCの目的
「製造現場で行われる改善効果の金額測定法開発及び、その会計的論理体系の構築」
を達成するうえで非常に重要です。
7.1 製造間接費配賦問題
複雑な生産工程で複数種の製品をつくる工場で、個別製品の製造原価を計算するとき出てくるのが製造間接費配賦問題。製造間接費を個別製品に跡付けするとき、その関連性が失われているために正しい原価が計算できない、という問題です。
この問題を最初に指摘したのは、「Relevance Lost」(Johnson & Kaplan,1987年)です。改善策として提案された活動基準管理(ABM)について、
「付加価値と非付加価値に分け、ムダを削減する点において現場改善会計に近いが、機会損失の測定と活用は明示されていない」
と「生産現場の改善と原価計算」で評しています。つまり、GKCでははじめから製造間接費配賦問題を認識していたことがわかります。
では、この問題に対してGKCはどのような改善策を提案したのか。これは、「3,現場改善会計論(GKC)の科研費研究実績報告」の総括で紹介した、「生産現場の改善と原価計算」(2016年)と「現場改善効果の類型化」(2022年)の計算事例の比較でわかります。
計算事例では、どちらも、「生産品種は1種類で計算期間を超える在庫はなし」という条件で間接費配賦の歪みを回避しています。間接費配賦問題に対する研究の痕跡は何もありません。GKCでは、この問題をそのまま放置した、ということになります、
7.2 ボトルネック現象、待ち行列現象
両現象は生産システムの持つ基本的な物理特性です。すでに述べてきたように、生産ラインの重要な基本特性である物理特性を無視したためか、「改善効果の金額測定」という目的達成のための課題も特定できていません。的外れで不可解な記述が散乱し、論理展開には程遠い低劣な説明がだらだらと続きます。研究成果がどうのこうのと論評する以前の問題ではないか、と思われます。
どこを探しても、「改善効果の金額測定」の具体的方法についての言及はなく、「会計的論理体系」に関する記述もありません。中身が“カラッポ”、という感じがします。
なぜ、そうなったか。実際は非線形特性を持つ生産システムを線形モデルとして扱い、論理展開を行ったからだ、と解するのが自然だと思います。
7.3 トヨタ生産方式の線形モデル化
トヨタ生産方式(TPS)の代名詞でもある Just In Time。ボトルネック現象と待ち行列現象の抑制によって、Just In Timeが成立し、生産ラインは線形モデルとして管理できるようになります。(詳細は、「5、GKCが捨象した生産ラインの物理特性」 を参照)
しかし、TPSを再現できるのはごく限られた企業だけです。一般企業の多くは多品種少量、変種変量受注生産なので、TPSのように、非線形特性を抑制することはできません。
GKCのムダの概念は線形モデル化されたTPSをベースにしています。非線形特性を持つ一般の生産システムにGKCのムダの概念を適用することはできません。
7.4 GKC関連論文は、すべて、“NULL”か
①間接費配賦問題を認識していながらなんら検討もせず、②ボトルネック現象・待ち行列現象を無視し、③TPSのスッキリした管理でわかりやすくなったムダの概念を一般企業にも適用しようとしたGKC。これら3つのうち、どれかひとつだけでも、GKCの目標達成への論理展開は不可能になります。実際は、致命的な条件が3つも重なっているわけです。
GKC関連の論文を読み返せば、そちらこちらに散乱する不可解な、不合理な記述が目に飛び込んできます。論理展開の大前提が間違っていたのですから、当然の帰結ではあります。
3つの致命的な間違いを抱えながら行われてきたGKCの研究を総括すれば、
研究手法も含めて、GKC関連論文は、すべて“NULL”である!
という結論になります。
10年余にわたり、研究が順調に進んでいるがごとく報告し実態を糊塗し続け、科研費を浪費してきたGKC。先月(2025年3月)で科研費研究の最終年度が終わりました。この研究をどのようなかたちで締めくくるのでしょうか。
“世間がアッと驚くどんでん返し” となるのか。
・・・微かではありますが、期待しています。