1,待ち行列問題について;藤本教授の解説
設計情報転写論では出てこない「待ち行列問題」についての解説が藤本隆宏著「生産マネジメント入門Ⅰ コラム;待ち行列問題(240~242p)」にあります。コラムに次のような説明があります。
実は「待ち行列」は問題の基本構造が、前述の在庫問題と似ていることを指摘しておこう。
・・(中略)・・
基本構造は同じだが、待ち行列問題では、インプット(顧客の到着ベース)、アウトプット(顧客の要求による)ともに企業側でコントロールできず、不確実性がともなう。「EOQ」問題では、インプット、アウトプットともに不確実性なしを前提にするし、「安全在庫問題」でも、アウトプットはある程度不確実だがインプットは決定論モデルである。しかし、待ち行列問題では、インプット(到着)、アウトプット(サービス完了)ともに、確率的に与えられる。
待ち行列問題を在庫問題との対比で説明しています。「EOQ」問題だとか「安全在庫問題」だとか、付属的なことだし、在庫問題にしろ、待ち行列問題にしろ、需要変動は避けられない環境条件とみるのが一般的、、、インプットやアウトプットの不確実性がどうのこうのと、イマイチ、ピンときません。
在庫問題との対比で説明しようとしている待ち行列問題ですが、その前に、在庫問題を藤本教授はどのように捉えているのか、そこを確認しておかないとダメかな、と感じました。
「生産マネジメント入門Ⅰ」を読み返してみると、今度は、在庫問題の説明に分かりにくい箇所がいくつかあって、しっくりこないんです。対比する在庫問題の理解が曖昧では待ち行列問題の説明も理解できなくなります。
ということで、在庫問題とはそもそも、なんだ、から始めることにします。在庫の基本的役割や基本原理に重きを置いて調べてみようと思います。基本的な視点からみるため、在庫問題を「在庫管理モデル」、待ち行列問題を「待ち行列モデル」と呼び換えて整理してみます。
2,在庫管理モデルの基本メカニズム
先ず、在庫管理モデルの基本的なメカニズムを確認します。図1は在庫管理モデルにおけるモノや情報の流れです。受注がトリガーとなって、出荷指示が出され、注文品が在庫から出荷(アウトプット)されます。一方、在庫状況をみながら必要な時期に必要な数量を供給元(納入業者)に発注し、納入後、入庫(インプット)します。
在庫を介して流通させるこのメカニズムは、製品倉庫、材料倉庫、工程間仕掛等々、基本はすべて同じです。基本は同じですが、実際は、定期発注方式、定量発注方式、ダブルビン方式、発注点補充点方式、定期補充点方式、定期発注点補充方式、CRP(連続在庫補充方式)、VMI(ベンダー管理在庫方式)など、、、それぞれの商品の特質や物流環境にあわせていろいろな在庫管理方法があります。この中に足を突っ込むと、わかりにくくなりますので、基本原理に最も近い在庫管理方式に絞り、それを基準にしたいと思います。
もっとも基本原理に忠実な在庫管理モデルとは? そうです。ご存知、「かんばん方式」です。
しかし、「かんばん方式」の導入失敗事例は後を絶ちません。世の中でうまく使いこなせない管理方法が基準になりえるのか、という疑問が出てきます。失敗原因は「平準化」ができていないからだ、といわれています。「生産マネジメント入門Ⅰ」にもこんなことが書いてあります。
234p;
その(かんばんシステム)の大前提は、後工程における平準化生産である。後工程の部品消費量が変動するようでは、実際の生産量でt期先の納入量を決めることに意味がなくなる。
ところが、ところが、、です。かんばん方式って、米国のスーパーマーケットの商品補充方法をヒントに編み出された、という話は有名です。でも、売れ行きって、平準化されていませんよね。しようと思ってもできませんよね。で、スーパーではどのような在庫管理をしていたか。例えば、定期的に商品棚を見回り、売れた分を調べて、(売れた分+α)を補充発注する、というような感じです。今ならPOSで簡単にできますが、、。
もうひとつ。「かんばん方式」生みの親、大野耐一著「トヨタ生産方式」(1978)の78p~80pに、“「かんばん」の弾力性”という段落があります。一部、引用します。
・・・(中略)・・・
シャフトのアンバランスをなくすために、仕上げの段階で、小さな鉄片のバランス・ウェイトが作業者の手ではり付けられる。
この小さな鉄片のバランス・ウェイトには五種類あって、プロペラ・シャフトのアンバランスの程度によって、そのなかから選ばれてはり付けられる。アンバランスがなければ、バランス・ウェイトはいらない。場合によっては何個もはり付けなければならない。これら五種類のバランス・ウェイトの使用量はまったく不規則であって、普通の部品のように、生産計画がわかれば使用量がわかる、といったものではない。
・・・(中略)・・・
「かんばん」は、毎日安定して使用される部品の管理にしか使えないものと考えている人がいるようだが、これはまちがいである。引き取りの安定した部品でないと、「かんばん」は使えないと、早呑み込みしているようである。これも間違いである。
・・・(中略)・・・
私は、「かんばん方式」は決して硬直化したものではないことを強調しておきたいのである。使用量の不安定な、一見、「かんばん」では御しきれないようにみえる特殊専用部品の管理にも、「かんばん」は有効な道具であることが、バランス・ウェイトの例にみられるとおり、トヨタ自工内部で実証されていることを知ってほしいのである。
使用量の不安定な部品の管理にも「かんばん」は有効な道具であることが、トヨタで実証されているんです。半世紀以上前に、、。つまり、平準化を条件としない一般の在庫管理にも「かんばん方式」は使えるということです。
「かんばん方式って、どこでも使えるってぇっ!」
にわかには信じられないかもしれません。おいおい、きちんと説明しますが、「かんばん方式」が消費(需要)がバラツク環境でも使える理由は、在庫管理モデルの中にバラツキを処理する数理モデルが組み込まれているからです。資料を紹介しておきます。
在庫管理;
かんばん方式を一般の在庫管理に適用できるように拡張不定期不定量発注;場当り的?、理想的?、、 ;
従来(一般の在庫管理)とSTIC(かんばん方式拡張)をシミュレーションで比較
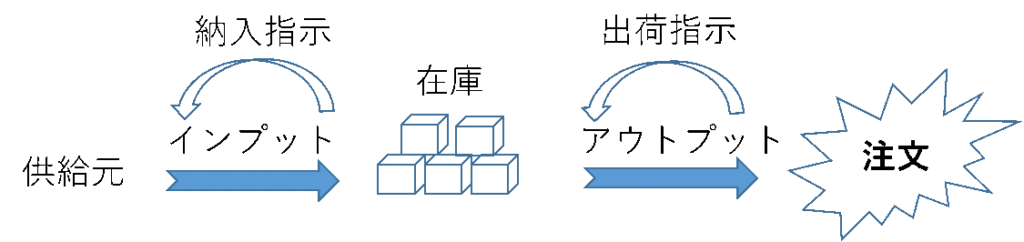
図1 在庫管理モデルの流れ
「かんばん方式」は特殊な条件(トヨタ生産方式とか平準化とか、、)でしか成り立たないということではなく、一般の在庫管理に使える。ということで、在庫管理モデルを「かんばん方式」をベースにして(基準にして)考えていきたいと思います。
3,待ち行列モデルの基本的メカニズム
一方、待ち行列モデルの流れは図2のようになります。注文(Aとします)を受けて生産を開始します。材料を投入(インプット)し、工程で処理が行われます。工程が前の注文品を処理している状態(ビジー状態)であれば、その処理が終わるまで工程前で待たなければなりません。前の注文品の処理が終わったら注文(A)の処理を行い、終了すれば次の工程(または完成品置場)に送られます(アウトプット)。
待ち行列モデルは日常、よく見かけます。ひるさがりATMに並ぶ人の列、スーパーのレジに並ぶ人の列、評判のラーメン屋さん、コロナワクチン接種会場、など、などで行列をよく見かけます。生産ラインの工程前にできる仕掛も同じ原理で生じます。決して、珍しい現象ではありません。

図2 待ち行列モデルの流れ
4,待ち行列の特徴;稼働率vs待ち時間(or仕掛数)
コラムには平均行列長(生産ラインでは平均仕掛数)と平均行列時間(生産ラインでは平均待ち時間)を求める数式はありますが、それが、どのような特性であるのかの説明はありませんので、補足しておきます。
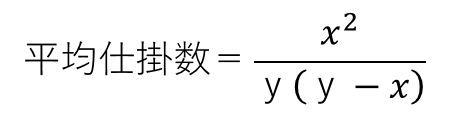
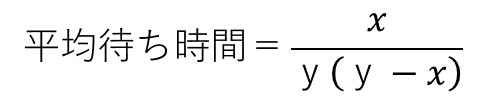
の式に具体的な数値を入れて計算してみます。単位時間を1時間(60分)とします。工程の平均処理能力 y を10個/60分 として、平均投入個数 x を0,0.5,1・・・・9.0、9.5個/60分 と振ってみます。
結果を図3に示します。
横軸は、平均投入個数ですが、処理能力が y=10個/60分 に対して、x=1個/60分 のときは、稼働率は10%、x=5個/60分のときは50%となり、稼働率を示します。
稼動率に対して平均待ち時間が指数関数的に長くなり、また、仕掛数も急激に増えるのが特徴です。
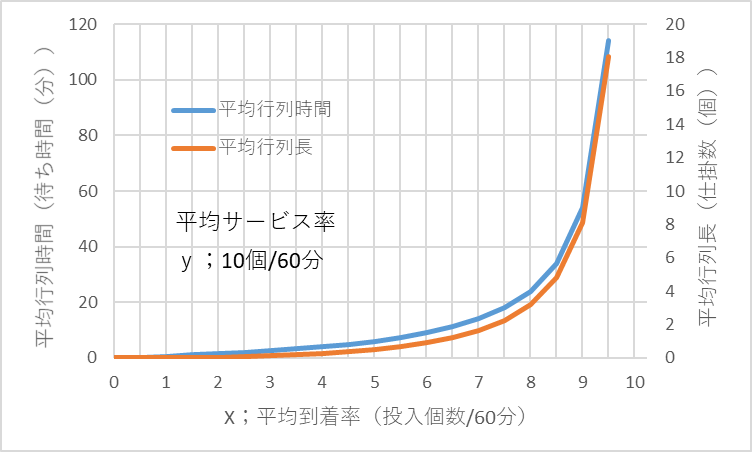
図3 稼働率vs平均待ち時間、平均仕掛数の特性
5,在庫管理モデルと待ち行列モデルを比べてみる
コラムではどのような比較をしているでしょうか。242pにある説明を再掲します。
基本構造は同じだが、待ち行列問題では、インプット(顧客の到着ベース)、アウトプット(顧客の要求による)ともに企業側でコントロールできず、不確実性がともなう。「EOQ」問題では、インプット、アウトプットともに不確実性なしを前提にするし、「安全在庫問題」でも、アウトプットはある程度不確実だがインプットは決定論モデルである。しかし、待ち行列問題では、インプット(到着)、アウトプット(サービス完了)ともに、確率的に与えられる。
5.1,基本構造は同じ・・・?
「基本構造は同じである」理由について、コラムでは次のように説明しています。
例えば、在庫におけるEOQ問題や、最適バッファー在庫問題は、インプットがあり、アウトプットがあり、その間のストックないし停滞を問題にする点で、待ち行列問題と共通している。
「インプットがありアウトプットがあり、その間に在庫が停滞する」、だから、「基本構造は同じである」と。
確かに遠くから眺めれば同じようにみえます。しかし、両者の在庫発生のメカニズムをみれば、異なる部分の方が多いのではないか、と感じられますが、さらに詳しくみていきます。
両者を比べてみますと、どちらも注文がトリガーとなって流れが始まることは同じですが、在庫管理モデルでは在庫から「搬出(出荷)する」のに対して、待ち行列モデルでは「生産を開始する」となります。これを別の視点からみれば、在庫管理モデルはプル型、待ち行列モデルはプッシュ型である、ともいえます。
在庫管理モデルでは、受注・出荷により在庫が減りますので、いつ、いくつ補充発注・入庫するかの管理が重要です。在庫数量の上限はコストを抑えるために、下限は欠品を防ぐために設定されます。在庫の増減は加減算で計算できる線形モデルです。
待ち行列モデルでは、投入間隔と処理時間が独立に変動することで、工程が処理中(ビジー状態)にワークが到着することがあります。そのような時、ワークは待つことになり、待っている間は仕掛在庫となります。待ち時間は既述のように稼働率(平均投入間隔÷平均処理時間)に対して指数関数的に長くなる(仕掛が増える)非線形モデルです。
在庫管理モデルの在庫には役割がありますが、待ち行列モデルではリードタイムが延長し、仕掛滞留によるコストがかさむなどの弊害が目立ちます。手空きを防ぎ稼働率を高める効果はありますが、リードタイムが急激に長くなる領域に入ると管理不能状態に陥る危険が出てきます。
生産管理上、在庫管理モデルと待ち行列モデルは、在庫の発生メカニズムが異なり、基本構造もまったく異なる、とみる方が正しいのではないか、と考えられます・
5.2 トヨタ生産方式との関係
待ち行列モデルの待ち時間発生を抑制しているのが「トヨタ生産方式」です。Just In Timeとは「必要なモノを、必要なときに、必要なだけ供給する」こと、つまり、待ち時間ゼロでモノを供給すること、と解せます。平準化、標準作業、サイクルタイムでの同期生産、多能工、アンドン、、など、トヨタ生産方式の多くのツールが待ち時間の抑制にかかわっています。
「かんばん方式」と「トヨタ生産方式」の関係について確認しておきます。「トヨタ生産方式」と最も結びつきの強いツールが「かんばん方式」である、「トヨタ生産方式」は「かんばん方式」が内在していることで成立している、と巷では、考えられています。
しかし、「かんばん方式」が平準化されていなくても使えることは、50年以上も前に、トヨタで実証済みです。売れ行きの変動が大きいスーパーマーケットで行われていた商品棚在庫管理から「かんばん方式」が生まれたことは単なる偶然ではありません。
「かんばん方式」が「トヨタ生産方式」成立の絶対条件ではないことが判ります。
「トヨタ生産方式」が成り立っているのは、持ち行列現象による待ち時間の抑制ができている(Just In Timeが実現している)からです。
Just In Timeが実現している環境で「かんばん方式」は威力を発揮します。非線形の待ち時間が無くなると、「かんばん方式」は線形モデルで運用、管理することができるようになります。必要なかんばん枚数の計算も簡単になります。
「かんばん方式」は在庫管理モデルの応用であり、Just In Timeは待ち行列モデルの応用である、とみることもできます。このことからも、在庫管理モデルと待ち行列モデルは、基本構造も基本原理も適用目的も、まったくと言っていいほど異なる、と言えます。
在庫管理モデルと待ち行列モデルでは、在庫の発生メカニズムが異なるだけではなく、管理方法もまったく異なることになります。
5.3,在庫管理モデルと待ち行列モデルの比較
表1に両者の比較を示します。
在庫管理モデル | 待ち行列モデル | |
流れ駆動 | プル | プッシュ |
在庫数量 | 実在庫+発注残+発注待ち | x²/y(y-x) |
生産 | 見込生産、まとめづくり | 受注生産、個別流れ生産 |
在庫の効用 | 欠品防止 | 稼働率向上 |
在庫の弊害 | コストアップ、LT延長 | LT延長、コストアップ、管理不能 |
特徴 | 線形モデル | 非線形モデル 稼働率vs待ち時間(仕掛) |
管理の重点 | 適正在庫、在庫上限・下限 | 待ち時間(仕掛)抑制、管理不能領域突入の回避 |
トヨタ生産方式 | かんばん方式の基本モデル | Just In Timeの実現をサポート |
x;平均到着率(生産ライン;単位時間に投入されるオーダー(ワーク)の数)
y;平均サービス率(生産ライン;単位時間での処理数)
表1 在庫と待ち行列モデルの比較
6,藤本隆宏教授の専門知識を疑う
待ち行列問題を在庫問題との比較で説明した藤本隆宏教授の見解についての所感をまとめます。
問題だと思われることを挙げます。
① 既に指摘済だが、在庫問題と待ち行列問題の「基本構造は同じ」は間違い。
② 「EOQ」問題や「安全在庫問題」そして「待ち行列問題」でインプットとアウトプットの不確実性の違いを挙げているが、需要は変動があるものが前提。在庫問題と待ち行列問題を区別する指標とはならない
③ 待ち行列理論の数式を持ち出しながら、待ち時間の指数関数的急延長について言及なし。的外れ。
④ 「かんばん方式」は使用量の不安定な部品の管理にも、有効な道具であることが、トヨタ自工内部で実証されている。にもかかわらず、「かんばん方式」の大前提は、後工程における平準化生産である、と否定している。
藤本隆宏教授に次のような質問をさせていただきました。(2023年7月頃)
一般に行われている「待ち行列理論」で生産システムを捉えるアプローチに対して、設計情報の転写で流れを捉え、流体力学(渋滞学)で生産シシステムを捉えることのメリットは何でしょうか。「待ち行列理論」では捉えられないが、流体力学(渋滞学)なら捉えられることとは、具体的には、どのようなことでしょうか。
次のような返事を頂きました。
佐々木様、藤本です。西成さんの本はお勧めです。待ち行列理論、流体力学、通常の在庫理論、これらは、状況に応じて使い分ければ良いのだと思います。
インプットとアウトプットの間に滞留ができると言う設定だと、インプット量、アウトプット量をそれぞれ確定にするか確率変動させるかで、いろいろな議論が使いますが、これは問題設定に合わせて選択すれば良いと思います。要するに、全部使えると思います。
待ち行列理論、流体力学、通常の在庫理論は状況に応じて使い分ければ良い。インプット量、アウトプット量は問題設定に合わせれば、全部使える、、と。
待ち行列理論、流体力学、通常の在庫理論の理解ができていないようです。それだけではなく、生産ラインの基本的メカニズムも理解できていないようです。このいぶかしき藤本隆宏教授の見解は、「生産マネジメントⅠ」(2001年6月)のコラムの説明と雰囲気が似ていますね。このいい加減さは、20年前から変わってないようです。
藤本隆宏教授に問う
*生産ラインの基本構造、モノが流れる基本的メカニズムを説明できますか。
*在庫を介してモノが流れる在庫流動の基本的メカニズムを説明できますか。
*生産ラインで発生する待ち行列現象を説明できますか。
*平準化しなくても「かんばん方式」は成り立つことをご存知ですか。
技術・生産管理、進化経済学を専門として、トヨタ生産方式をはじめとした製造業の生産管理方式の研究で知られる、と紹介される藤本隆宏教授です。
どうみても、藤本教授の専門領域の知識レベルに問題がありそうです。だとすれば、藤本教授の講義を受講した学生、東大ものづくり経営研究センター(MMRC)の受講者、後継教授陣およびメディアを通じて彼の主張に接した一般の方々は、彼から習った中身をチェックしてみる必要があるかもしれません。