日本のものづくりを先導する藤本隆宏教授が提唱する「設計情報転写論」。その骨子は、ものづくり企業の開発から販売までの流れに沿ってみれば、
- 設計情報を創造するのが開発
- 素材を社外から調達するのが購買
- 設計情報を素材に転写するのが生産
- 設計情報が素材に転写されたものが製品
- 製品を顧客に発信するのが販売
と説明されています。これからもわかるように、設計情報転写論はモノを加工し、組み立てる工程(生産、製造、)だけではなく、開発~購買~生産~販売 と製造業のほぼ全工程を対象にしています。さらに、サービス業など、製造業以外にも広く適用できるとしています。
1、サービス業への適用事例
ものづくり改善ネットワーク の中にサービス業への適用事例として「ものづくり現場としての医療現場」(YouTube)がありますので、ちょっとのぞいてみましょう。
以下、要約~~~~~
画1は開発された医薬・医療システムという設計情報を患者に転写して健康状態を改善する流れを示している。健康が不安定な人が医療サービスを受けて(転写して)健康な人になる。
画1 サービス業としての医療
医療現場をものづくり現場の視点でみた流れが画2に示されている。
画2 医療現場での「患者さんの良い流れ」作り
ここで、重要なポイントは、工程別稼働率(画3)とリードタイム(画4)である。
画3 工程別稼働率(医師の目)
画4 リードタイム(患者の目)
開院中の有効稼働時間(稼働率)と患者のリードタイム(来院~帰るまでの時間)を同時に表す方法として画5を例示している。
画5 稼働率とリードタイムを表示
患者の滞在時間を短くする改善策として、次のようなことを挙げている。
画6 患者の滞留時間を意識する
~~~~~~~~~~~~
「設計情報転写論」は製造業だけではなく、サービス業にも適用可能である事例として「医療現場」を紹介しています。
「工程別稼働率(生産性)」を高く維持しながら「患者の滞在時間(リードタイム)」をできるだけ短くするためにどうするか、が課題のようです。ものづくり現場の視点で医療現場の改善点が図6にまとめられています。要点を再掲しますと、
- 「患者の流れ」を良くする
- 予約時間調整でボトルネック発生を防止する
- 柔軟なスケジュール修正ができる人材を配置する
- 職能ごとに適切な作業分配をする
- 標準作業時間を意識する
課題の範囲はいいとして、各項目それぞれはピンボケで、的を射てない感じがします。生産ラインの基本特性である「稼働率」と「生産リードタイム」の物理的特性に基づく説明がまったくありません。
2、生産ラインの基本特性
2.1 シミュレーションで確認
生産ラインの基本特性って、どうなっているか、医療現場の事例と同じように5工程直列ライン(図1)を例に、シミュレーションで確認してみます。
まず、サービス時間は各工程10分一定とし、来院間隔は10.53分(稼働率は95%)とします。

図1 5工程直列ライン
表1に最初から6人目までの来院者ごとの工程を通る時刻を示します。
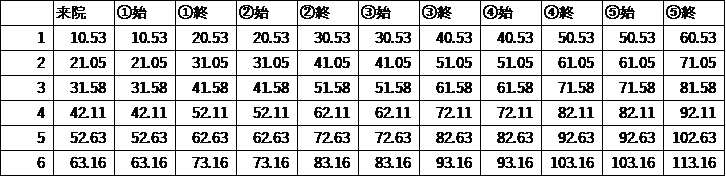
表1 最初から6人目までの来院者ごとの工程を通る時刻
10.53分に1人目が来院、ただちに第1工程開始(①始)、10分後の20.53分に終了(①終)。待つことなく直ちに第2工程開始(②始)。21.05分に2人目が来院、ただちに第1工程開始。1人目が30.53分に第2工程終了(②終)。2人目が第1工程を31.05分に終了。以下同様。
図2はグラフにしたものです。横軸は工程、立て軸は経過時間を示しています。グラフの灰色の部分は工程間の移動を示しています。ここでは工程間の待ち時間はゼロです。(運搬などの移動時間はゼロとします)
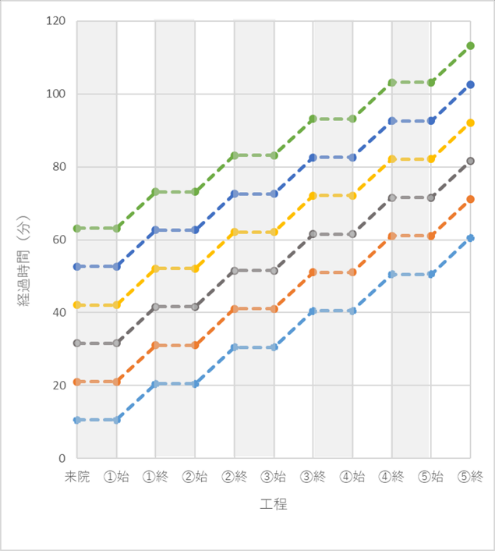
図2 患者の各工程を通る時刻
各工程のサービス時間(処理時間)が同じで一定(バラツキなし)、そして来院間隔も一定で、来院間隔>サービス時間なので、いずれの工程でも待つ時間はゼロです。
ここで、予備的なシミュレーションをしてみます。処理時間がバラツクとどうなるか。変動係数(標準偏差/平均値)を0.2、0.4、0.6(各工程同じ)とした場合、図2のグラフがどうなるかをみてみます。シミュレーション結果の一例を図3に示します。
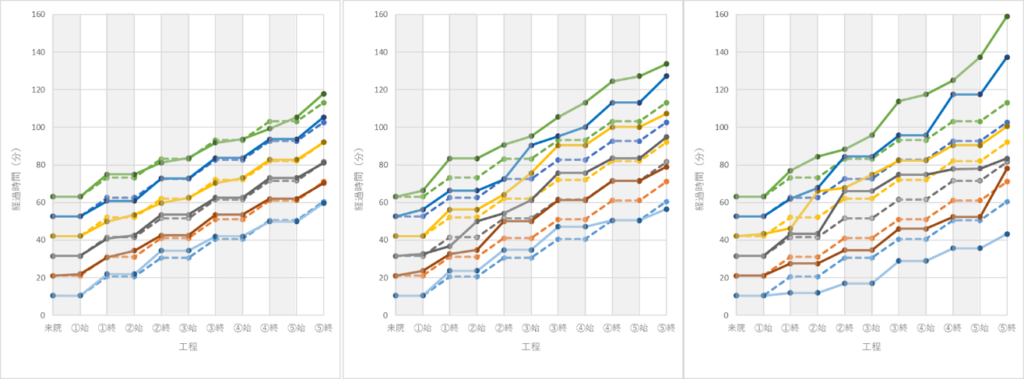
図3 変動係数;左から 0.2、0.4、0.6
破線はバラツキがない場合、実線はバラツキがある場合です。変動係数が大きくなるに従い破線と実線の差が大きくなることがわかります。
2.2 シミュレーション条件範囲
実際は来院間隔もバラバラ、内科とか外科とか大まかな専門領域はあっても個々の患者の疾患も様々なのでサービス時間(診察、処置、、時間;以下、処理時間)もいろいろです。
工程への到着間隔と処理時間が変動するとき、患者ごとの処理時間の合計、各工程での待ち時間の合計、投入から完成までのリードタイムがどうなるかをシミュレーションしてみます。シミュレーションは簡易的にエクセルで行います。
*稼働率の条件
稼働率は0.95、0.85、0.75の3種類とします。
*処理時間の条件
処理時間の平均はどの工程も10分、処理時間のバラツキは、どの工程も同じとして、変動係数で0.2、0.4、0.6の3種類とします。分布はガンマ分布を使います。
*来院間隔の条件
稼働率=処理時間/来院間隔 なので、稼働率に対して来院間隔平均は表2のようになります。来院間隔の変動係数は0、0.5、1の3種類とします。分布は、変動係数0.5はガンマ分布、1は指数分布を使います。
稼働率 | 来院間隔平均(分) | 処理時間平均(分) |
0.95 | 10/0.95=10.53 | 10 |
0.85 | 10/0.85=11.76 | 10 |
0.75 | 10/0.75=13.33 | 10 |
表2 稼働率と来院間隔
図4にシミュレーションの条件範囲を示します。
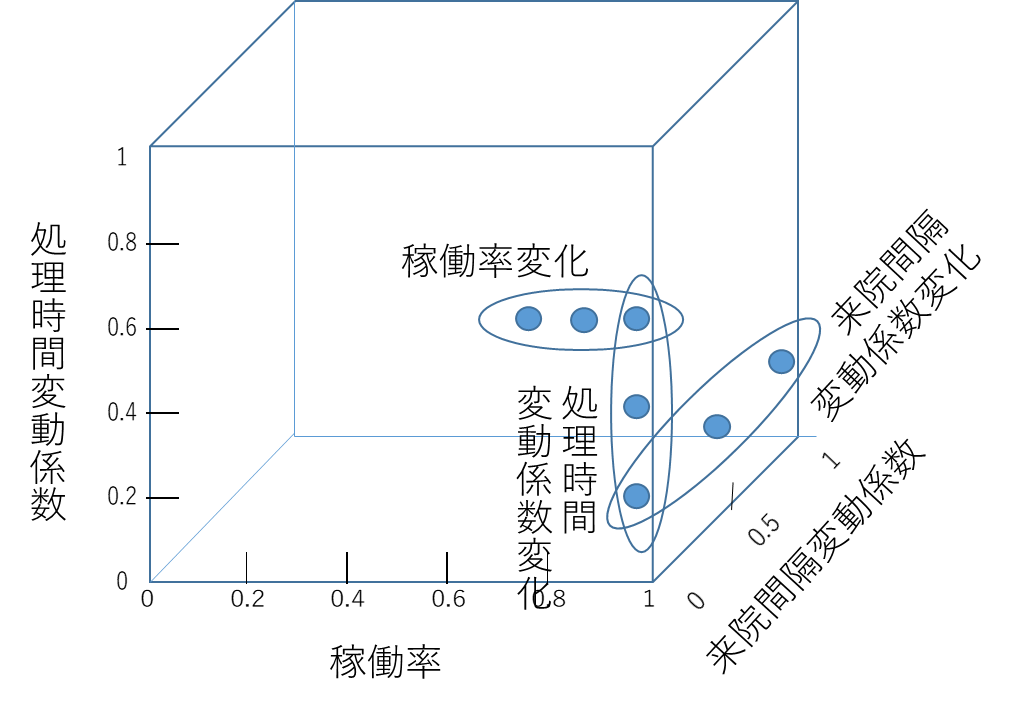
図4 シミュレーション条件の範囲
3、シミュレーション結果
来院から帰宅までのリードタイム、サービス時間(処理時間)、待ち時間の3項目のシミュレーション結果をみてみます。
データ数(来院患者数)は1000(人)とします。
3.1 処理時間変動係数変化
来院間隔;10.53分一定
各工程処理時間平均;10分、変動係数;0.2、0.4、0.6
特性項目;処理時間(水色)、待ち時間(橙色)、リードタイム(灰色)
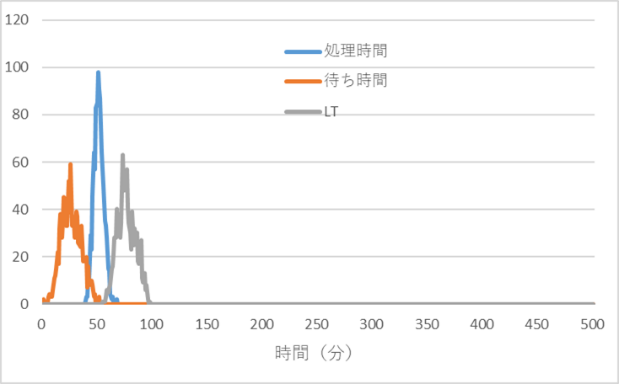
図5 変動係数;0.2
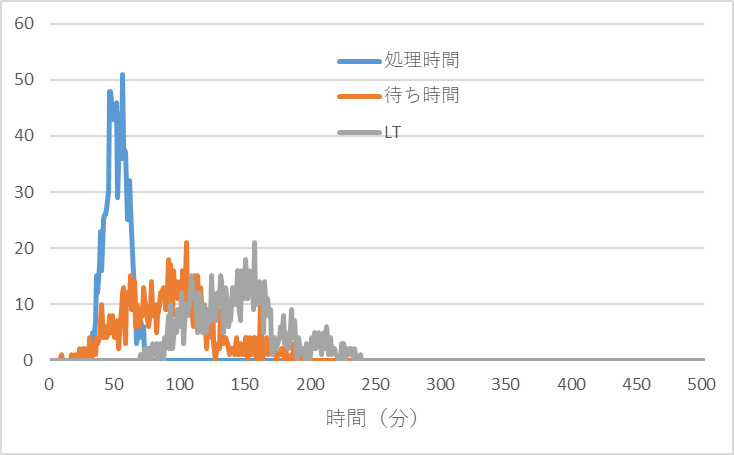
図6 変動係数;0.4
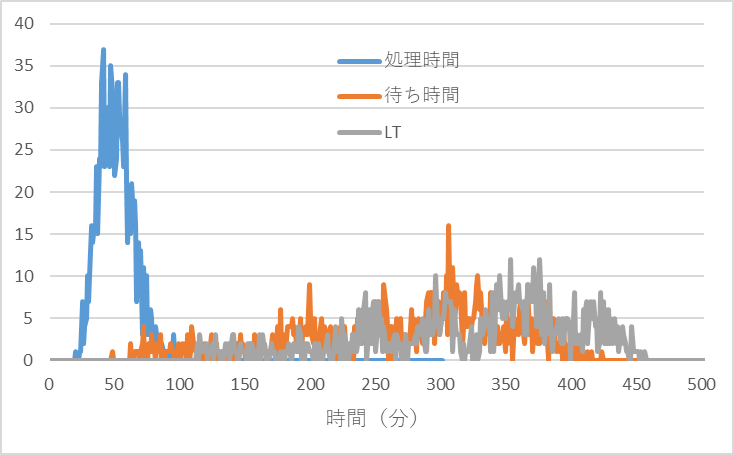
図7 変動係数;0.6
3.2 稼働率変化
来院間隔;10.53分一定(稼働率0.95)、11.76分一定(0.85)、13.33分一定(0.75)
各工程処理時間平均;10分、変動係数;0.6
特性項目;処理時間(水色)、待ち時間(橙色)、リードタイム(灰色)
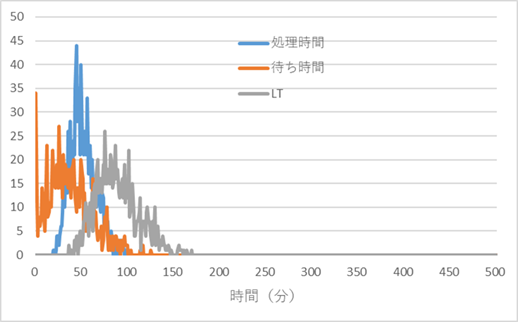
図8 稼働率;0.75
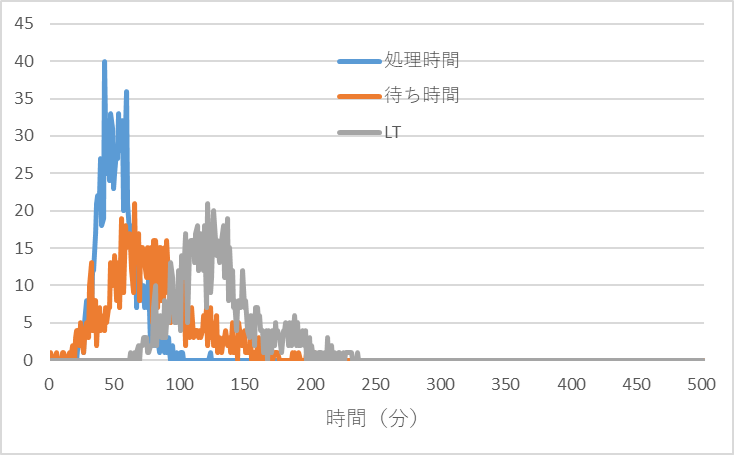
図9 稼働率;0.85
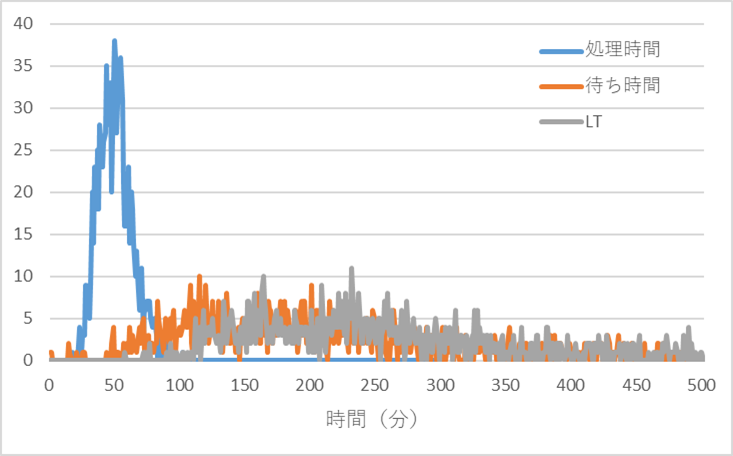
図10 稼働率;0.95
3.3 来院間隔変動係数変化
来院間隔平均;10.53分(稼働率0.95)、変動係数;0、0.5、1
各工程時間平均;10分、変動係数;0.2
特性項目;処理時間(水色)、待ち時間(橙色)、リードタイム(灰色)
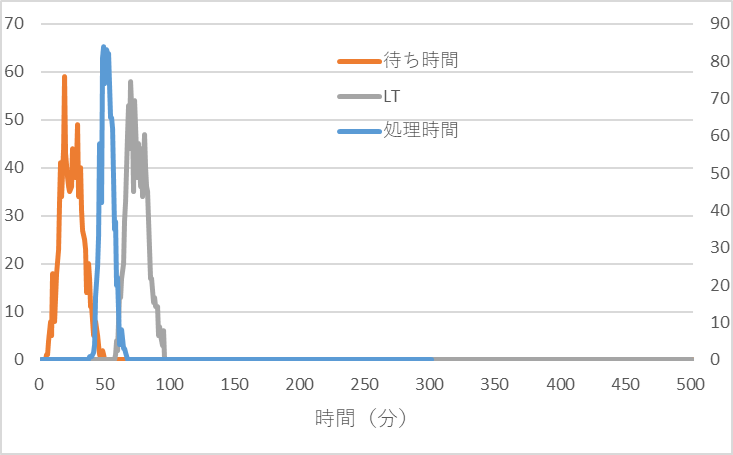
図11 来院間隔変動係数;0
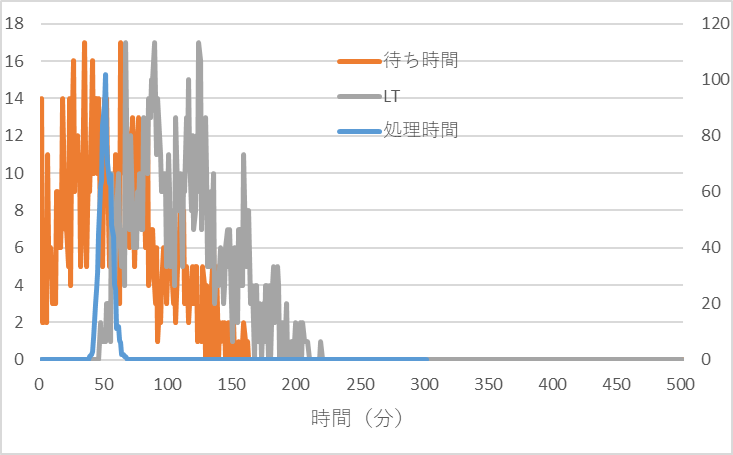
図12 来院間隔変動係数;0.5
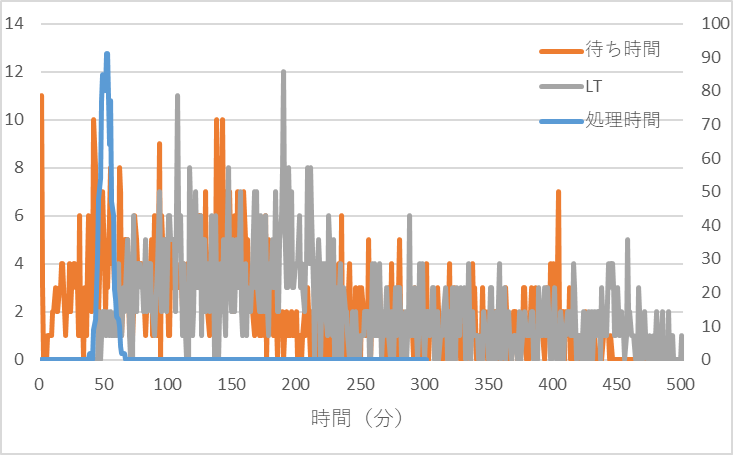
図13 来院間隔変動係数;1
3.4 シミュレーション結果の大雑把なまとめ
シミュレーション結果から、特徴をザックリとまとめると、次のような事が言えるのではないでしょうか。
- 稼働率が高くなると待ち時間、リードタイムが長くなる。
- 処理時間の変動係数が大きくなっても、来院間隔の変動係数が大きくなっても待ち時間、リードタイムは長くなる。
- リードタイムが長くなる要因の大部分は、待ち時間が長くなるためである。
- リードタイム(待ち時間)が長くなるとそのバラツキも大きくなり、だだっ広い分布形状となる。
4、「ものづくり現場としての医療現場」;流れ改善の方向性
シミュレーション結果からみて、医療現場の流れを良くし、生産性とリードタイムを改善するためにどんなことが重要なのかを考えてみたいと思います。
医療現場の特徴として次のような事が挙げられます。
- 急患の来院➡発生時刻が予測不能
- 患者ごとのサービス(診察、検査、治療、、)が異なる➡多品種変量少量生産に類似
- 患者ごとの来院時間がまちまち➡受注生産と類似
医療現場の管理という視点から管理状態をザックリと、二つに分けてみます。
①管理可能状態
②管理困難状態
管理可能状態とは、待ち時間やリードタイムの分布形状が山形(釣鐘形状)で、統計理論での確率推定が可能な場合です。
管理困難状態とは、シミュレーション結果で示せば、図7、図10、図13のような分布形状で、だだっ広く広がっている場合です。だだっ広い分布形状ですと、統計理論を使っても特性間の因果関係の蓋然性が低く、「流れ」改善のための「なぜなぜ5回」も「PDCAサイクル」もうまく機能しなくなります。
従って、現状が管理可能状態なのか管理困難状態にあるのか、を知ることが非常に重要となります。
常に問題を抱えているのか、来院患者数が多いときとか、医師やスタッフが手薄のときとかに問題が起きやすいのか、経験則である程度の判断はできると思います。慢性的であれば、管理困難状態にあるのかどうかを調べる必要があるでしょう。
調べる方法は現場環境で異なると思いますが、簡単には例えば、患者ごとの時刻記録(診察開始・終了時刻、検査開始・終了時刻、、、会計終了時刻)を必要人数分採るなどの現状調査をするのが一般的です。
管理可能状態にあれば、「流れを」さらに良くするためにどこを改善するか。ポイントは、医師、スタッフの稼働率と患者の待ち時間はトレードオフの関係にあることを認識しながら、稼働率を上げたいのか、患者の待ち時間を短くしたいのか、あるいはどちらも改善したいのか、狙いを定めます。
医師の稼働率と患者の待ち時間を決める主要因は、患者の来院間隔の平均とバラツキ、及びサービス時間の平均とバラツキですので、改善策を考える場合のキーワードになります。また、管理困難状態に陥らないような策を考えておくことも重要です。
ザっと、医療現場の改善の方向性について愚見を述べましたが、現場の環境によって具体的な対策はさまざまでしょう。ただ、稼働率と待ち時間の関係が、生産ラインと同様のメカニズムであれば、基本原理は同じですので、応用範囲は広がると思います。
藤本教授の解説のまとめ;
- 「患者の流れ」を良くする
- 予約時間調整でボトルネック発生を防止する
- 柔軟なスケジュール修正ができる人材を配置する
- 職能ごとに適切な作業分配をする
- 標準作業時間を意識する
と比べてみてください。違いがあることはお分かりいただけると思います。
違いの原因は、「設計情報転写論」では生産ラインの基本特性を捨象している(切り捨てている)ことにあります。最も重要な特性を切り捨てましたから、「設計情報転写論」で生産ラインの問題点を指摘することができないのは当然です。
医療現場もサービス業とはいえ、生産ラインと同じメカニズムで動きますので、「設計情報転写論」に沿って改善を行うとすると、ピンボケで、的はずれた改善策になってしまいます。経験則で判断した方がまだ、マシでしょう
医療現場でも「「設計情報転写論」は使えません。