前回は、AIで生産管理はどうなるか、日立の取組をみてみました。要点は、
鉄道の運行管理などの数理最適化技術(所有技術)とAI制約プログラミング(新技術)を融合し、熟練者独自の計画パターンを機械学習させ、
- 自動的に最適な生産計画の立案
- 需要変動など日々の環境変化にも柔軟に生産計画の組み替えを可能とする
のだそうです。
これで生産管理の問題がすべて解決か、という期待で読み進んだんですが、途中から “あら、あらあら”となって、最後は“ガクン”ときて、、、。
で、なぜ、“ガクン”ときたのか、その理由の方が重要かもしれませんので、そのあたりについて愚見を放ってみたいと思います。
日立の説明の中に、キーワードがいくつかあります。
*鉄道の運行管理
*生産計画
*日々の環境変化
「鉄道の運行管理」には最適なダイヤグラム編成も含まれていると思います。それをベースに運行を管理する。工場では、最適な生産計画をつくり、それをベースに生産管理を行う。似てますね。日立が手持ちの鉄道の運行管理技術にAIを加えて、生産計画作成支援サービスを開発した、という流れです。
このような技術の転用、応用はいたるところで起きています。ものごとの発展、進化の王道的流れではないかと思います。逆にみれば、どこが同じ(似て)、どこが違うのか、という視点でみれば、日立の取組の方向性が正しいのか、そうでないのか、を判断する手がかりになるかもしれません。
「鉄道」と「生産ライン」を対比させてみてみましょう。鉄道の線路は生産ラインでの工程(機械、作業員、)に、列車は工程を流れる被加工物(以下、ワーク)に。
鉄道 | 生産ライン |
線路 | 工程(機械、作業員、、) |
列車 | 被加工物(ワーク) |
全体が見えるように比較の幅を広げてみます。鉄道に一般道を加えて“交通・運輸”、生産ラインを“工場・生産管理”とし、トヨタ生産方式と一般の工場とに分けて比べてみます。トヨタ生産方式の特徴を見込生産、一般の工場の特徴を多品種変量/見込受注混合生産とします。
列車の運行制御はダイヤグラムに基づき、一般道を走る自動車は各自それぞれのスケジュールで交通ルールに従って動きます。トヨタ生産方式では企業(工場)全体の生産計画があり、それに基づいてワークが流されます。一般の工場では、生産計画をつくってもその通り生産は進まず、計画と実際にズレが生じ、現場の判断で計画とは違った手順で進められることが常態化しています。
線路は列車専用でダイヤグラムに従って運行されますので列車間の干渉はほとんどありませんが、一般道は様々な交通手段で共用され、各自のスケジュールで動きますのでいたるところで干渉が起こります。トヨタ生産方式では生産計画からつくられた日程計画に従い作業が割り当てられますので、大きな干渉はありません。一般の工場では生産計画がうまく機能しないため、いたるところで干渉が生じます。
線路に対する負荷はダイヤグラムの管理下にあります。一般道では社会活動の影響をそのまま受けますので交通量の変動は大きくなります。トヨタ生産方式では生産計画時に負荷が調整され、その生産計画は変更されませんので、負荷の変動は非常に小さく抑えられます。
一般道での待ち時間は交通量により大きく変動します。高速道路でさえ帰省シーズンは長蛇の渋滞。動かない車の中で過ごす家族のニュース映像はお馴染みです。一般道では通勤時の渋滞。常態化してます。一方、列車の待ち時間は、列車の種類にもよりますが、一般道と比べ非常に短くなります。一般の工場でのワークの待ち時間は需要(受注量)により大きく変動します。残業や外注化で生産能力を補強したり、納期を調整したり、時には受注調整を行うなど、対応に追われることになります。加工時間に対する待ち時間の比は1:5000、一方、トヨタでのそれは1:300だそうです(トヨタ生産方式をトコトン理解する辞典、山田日登志著より)。トヨタの待ち時間の短さがわかります。
表2にまとめてみました。
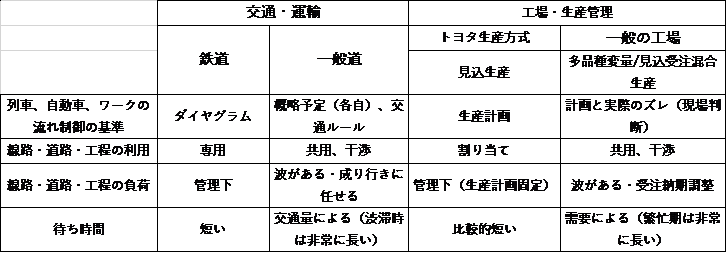
表2 交通・運輸と工場・生産管理の比較
ザックリと比較の特徴を挙げれば、次のようになります。
- 鉄道は、線路が専用で、全体のダイヤグラムで管理されている。
- 一般道は、様々な交通手段(歩行者も含む)で共用され、個々の予定はあっても全体のスケジュールはない。交通量は大きく変動する。
- トヨタ生産方式は、月次生産計画を固定し、それに基づく負荷配分等を行い、実行可能な日程計画で管理される。
- 一般の工場では、計画が策定されても、需要の変動で計画通り生産は進まず、多くはその場その場で場当り的な対応をしてしまう。
鉄道はダイヤグラムという全体計画がありますが、一般道を走る各々の車の全体計画はありません。トヨタでは生産計画という全体計画がありますが、一般の工場では変更が頻発して実行可能な全体計画とはなっておりません。
日立の説明をもう一度みてみましょう。
鉄道の運行管理などの数理最適化技術(所有技術)とAI制約プログラミング(新技術)を融合して、熟練者独自の計画パターンを機械学習させ、
- 自動的に最適な生産計画の立案
- 需要変動など日々の環境変化にも柔軟に生産計画の組み替えを可能とする
、、、と。
生産管理の基準となる生産計画を自動的に立案し、日々の環境の変化が激しい一般の工場では、計画そのものを短時間で組み替え、生産計画を実行可能状態に維持する。こうみてみますと、日立は、現状の生産管理の問題を的確にとらえているようにみえます。
完璧に見える日立のアプローチ。実は、思いがけない落とし穴があるんです、、。
落とし穴があるなんて、誰も気づきません。完璧に見えれば見えるほど、穴の深さは深い。日立もその穴の中にはまったまま、出てこれなくなっているのかもしれません。日立だけではありません。“柔軟な計画変更”を喧伝する生産管理ソフトメーカー・販売会社も同じ穴の貉(むじな)ではないか、と。
表2を眺めてください。鉄道にはダイヤグラム、トヨタ生産方式には生産計画があります。では、一般道では? 一般道路網のダイヤグラムはありますか、、?
「ありますよ。乗り合いバス」
そうですね。乗り合いバスではダイヤグラムとは言いませんが、時刻表はそれに相当します。走る道路は予め決まっていて、さらにラッシュアワーには専用レーンとなるところもあり、鉄道に似ています。時刻表の精度は鉄道のそれと比べれば低いのはやむを得ませんが、、。
乗り合いバスは交通量全体からみれば少量でしょう。一般道を走る交通手段すべてを対象にしたダイヤグラム(時刻表)みたいなものって、ありますか。
・・・・・・・
「ありますかぁ~」、「ありませんかぁ~」、、
「・・・・・・・」
ちょっと、バカバカしい質問だったようです。
「そんなもの、あるわけないじゃないか」
「考えるまでもないよ」、、
口に出せば、品のない答えになってしまいます。
表2の右側、工場・生産管理の方をご覧ください。交通・運輸の一般道に相当するのが多品種変量/見込受注混合生産(一般の工場)です。生産ライン(工程網)では様々な製品がランダムな時間間隔で投入されるのに対し、一般の道路網では様々な交通手段(車、バイク、自転車、、)がランダムに流入する。両者の物理現象は重なります。
一般の道路網で様々な干渉が起きて混雑するように、一般の工場でも様々な干渉で混乱、停滞が起きます。
「問題はきちんとした生産計画がないからだ。必要あらば、毎日でも生産計画を組みなおさなければならない」
名うての生産管理コンサルタントの指導に逆らう御仁はおりません。日立も同じ方向を向いています。つまり、“生産計画作成→日々の環境変化→速やかな生産計画の組み替え”を繰返し、生産計画基準の生産管理体系を維持する、という考えですね。
一般道では、前代未聞のダイヤグラムですが、一般の工場では、基本中の基本。おもしろいですね、この違い。
どこに落とし穴が隠れているか、うすうす、お気付きになっていただけるとたすかります。
では、ダイヤグラムなどあたまの片隅にもない一般道では、AIをどのように利用しようとしているのか、みてみましょう。最近よく聞きますね。自動運転。そのうちレベル5(完全自動運転)の車も実用化されることでしょう。客探しAIを搭載したタクシーも導入されているそうです。AIを搭載した無人配送車も実用段階に近づいているようです。ヒントになりませんか?
自動運転の車を工程を流れるワーク(被加工物)とみたらどうでしょう。
こんなイメージかなぁ~、、
生産ラインの状態(工程の稼働状態、仕掛、投入待ちワーク、トラブル状態、、)が常時監視されている。個々のワークには必要情報(工程順、処理方法、納期、など)が入力されたチップが付けられ、工程が進むごとに履歴が更新される。各ワークは、各々の優先度や工程の負荷状態などをみて、通過工程を選択しながら流れていく。
生産リードタイムは確率分布で捉えられる。納期が10日なら60%、12日なら90%というように、予め納期遵守率が確率で示される。生産ラインの負荷状態を常に監視し、受注量、納期等を考慮して投入コントロールを行う。データが蓄積されればされるほど、学習効果が上がり、管理レベルは向上する。市場の需要変動に追従しながら生産の流れをコントロールする。
AIで生産計画をつくり、それを介し生産ラインを管理するのではなく、AIで直接生産ラインをコントロールする。これこそ、AI生産管理が向かう方向ではないでしょうか。
AIも、馬鹿も鋏も使いよう・・・