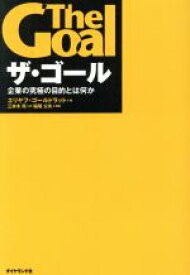
成功事例よりもはるかに多い生産スケジューラ導入の失敗事例。今始まったことではありません。様々な改善の努力も行われています。月間雑誌「工場管理」では頻繁に取り上げられるテーマです。「あーやればいい」、「こうやらなくちゃ」、「いやいやこうであるべきだ」、、と議論は尽きません。でも、改善の兆しは一向に見えない。
AIだ、IoTだ、第4次産業革命だって騒いでいるご時世ですから、生産スケジューラもさぞかし進化しているのでは、と思われる方も多いと思います。生産スケジューラ・ベンダーのWebsiteを見れば、見込生産、受注生産なんでもござれ、スケジュール変更も即座に対応、、うんぬんと万能ぶりをうたう説明が満載。
生産現場で多発する生産スケジューラ導入失敗事例とベンダーの美辞麗句。このギャップに、異常な“怪しさ”を感じてしまいます。これが、日本の“製造業”をむしばんでいなければいいのですが、、。製造現場でも、お悩みの方が多いのではないか、と察します。
「えっ、えっ、えっ、、生産スケジューラって、そんなに複雑な問題なんですか? 昔からあったし、スケジュールなんて、日常生活のいたるところにあるじゃないですか。珍しくもなんともない。何が問題なんですかぁ~。」
生産スケジューラの背後にある問題構造とは? と、大上段に構えるつもりはありません。ごく、常識的な知見をつなぎ合わせながら、生産スケジューラが抱える根本問題を探ってみたいと思います。
ちょっと、振り返ってみましょう。生産スケジューラと最も関係が深いのがMRP。
MRPはMaterial Requirements Planningで、資材所要量計画のこと。計画した生産台数に必要な部品などの数量を計算するのに使われます。それにスケジューリング機能が加わり、MRPIIとかManufacturing Resource Planning(製造資源計画)となります。生産スケジューラとの関係を考えるのは、MRPIIの方ですが、MRPと略します。
MRPのスケジューリング機能は、その出自からみてもわかりますように、時間単位(タイムバケット)が大きい。1週間程度が多いようですが、時間や分、秒単位ではない。ですから、MRPのスケジュールは大雑把。
時代が進むと、この大雑把さが問題となってきます。この問題に対していくつかの提案が出てきます。その中のひとつが、TOC(制約理論)のDBR(Drum Buffer Rope)。
“『ザ・ゴール』誕生の背景とその後”から抜粋、要約
1970年代後半にイスラエルの物理学者エリー・ゴールドラット(Eli Goldratt)は生産スケジューリングのことを相談され、物理学の研究で得た発想や知識を使って当時としてはアーキテクチャ面で画期的な生産スケジューリングソフトウェアOPT(Optimized Production Technology)を開発した。
OPTは高価なソフトウェアであるにもかかわらず、それを導入した工場では生産性が大幅に改善され、生産リードタイムが劇的に短縮するという効果が出て一躍注目されるようになった。
市場環境も良かった。どの工場もコンピュータ導入に躍起で、オートメーションが時代の流行でもあった。どの生産マネジャーもスループットの向上と納期遵守に悪戦苦闘していた。仕掛品の削減メリットに注目し始めた者もいた。これを実現する機能を備えたソフトは、OPTだけだった。にもかかわらず、クライアント数は期待したほど増えなかった。
失望感のなかから、何か新しいアプローチがあるはずだとゴールドラットは考えた。小説を通じて製造とは何なのか、彼の手法を伝えようと思ったのだ。『ザ・ゴール』の誕生である。
ところが、『The Goal』の出版(1984年)直後に、多くの読者から『The Goal』は自分の工場とまったく同じ状況を描いているとか、自分の工場をモデルにしたのではないかという手紙が舞い込むようになる。中には小説にあるとおりに改善を実施してみたら、小説とまったく同じような劇的な成果が出たという手紙もあった。
いくつかの工場を訪れるにつれ、ゴールドラットは非常に不愉快な現実に直面することになった。それまで我が子のように大切に育て誇りにしていたスケジューリング・ソフトがパフォーマンス改善にとって障害になるのだと現実が証明してしまったのだ。『ザ・ゴール』を読み、その内容を実行しただけの工場のほうが、高いお金を払ってOPTを採用したクライアントより高い成果を上げてしまったのだ。それもはるかに短い期間にである。どうしてなのだとゴールドラットは悩んだ。
これがきっかけで、ゴールドラットはOPTの販売を止め、その背後にある考え方をTOC(Theory Of Constraints:制約条件の理論)と名付け、経営コンサルティングに従事するようになったのである。
この件(くだり)に、生産スケジューラの特性が隠れているのではないか、と思います。それは、「OPTでうまくスケジューリングすることができなかった」ことです。
OPTはボトルネック工程の能力を100%発揮するように、スケジュールします。つまり稼働率100%でスケジュールします。そうしますと待ち行列現象が起きて、予測不能な待ち時間が発生します。こうなるとスケジュール通りの実行が不可能になります。
待ち行列現象による待ち時間を短くするためには稼働率を下げるしかありません。つまり、稼働率と待ち時間はトレードオフの関係にあります。
しかし、スケジューリング通りに実行できなくても、ボトルネックの能力を重点に管理することになります。その結果、工場全体の生産性は改善することになります。
前に取り上げたA社の事例によく似てます。
MRP/生産管理パッケージを使っていた受注生産が主体のA社。納期短縮のため、詳細な計画を策定できる生産スケジューラの導入を企画した。導入してみたが、納期の短縮は実現できなかった。むしろ以前よりも納期が長くなるケースが頻発したり、欠品が増えたりした。
コンサルタントの支援を受けてたどり着いた解決策(運用基本方針)は、
「ボトルネック工程は手作業で管理」
「前後の非ボトルネック工程はスケジューラで計画作成」
でした。その結果、
「新たな運用基本方針により、A社の標準納期は標準品が平均30日から平均10日、材料調達を伴う特注品は平均60日から平均40日に短縮できた。」
つまり、稼働率の低い非ボトルネック工程はスケジュールできるが、稼働率の高いボトルネック工程は実行可能なスケジューリングはできないため、手作業で管理することにした、ということです。「『ザ・ゴール』を読み、その内容を実行しただけの工場のほうが、高いお金を払ってOPTを採用したクライアントより高い成果を上げてしまった」話と似ていませんか。
オーダーが次々飛び込み、作業時間等は確率的に変動する環境では、
「ボトルネック工程の稼働率が100%のとき、待ち時間が予測不能となり、実行可能なスケジューリングを組むことは不可能である」
と言えます。稼働率と待ち時間はトレードオフの関係にあり、この現象から逃れることはできません。
「OPTがなくても、それ以上の改善効果が出る」。ゴールドラットはなぜそうなるのか、理解できていなかったようです。10年もの年月をかけて開発したOPT。MRPの大雑把なスケジューリングを改善しようとした試みは未達に終わりました。しかし、ゴールドラットの非凡なところは、ポジティブな面、つまり、スケジューラがなくても生産性を改善できることに注目したことです。それがDBRとなり、TOCに発展したわけです。
次回も、生産スケジューラとTOCの関係をみていきます。