現場改善会計論(以下、GKC)の論理構成のキーワードは「時間」ではないかと考え、
「製造現場における改善効果測定と2種類の時間概念」柊紫乃、上總康行、2017(以下、「2種時間概念」と略称)
に注目しました。巷に出回る常識的知見を持ち込むと、解析にゆがみを与えかねないので、生産ラインの時間特性を「待ち行列理論」をガイドラインにしたらどうか。ということで、前回その紹介をしました。今回は、「2種時間概念」がGKCの論理基盤をどのように支えているのか、あるいは逆に崩壊させているのか、現場の実態を思い浮かべながら、斬り込んでみたいと思います。
1、モノづくり;市場と工場をつなぐ時間要素
モノをつくるトリガーとなるのは、いつ、どこで、だれが、なにを買うか、である。ここでは、“いつ”買うか、“いつ”売れるか、に注目する。この“いつ”という時刻が生産管理では重要な時間要素の一つであるからだ。
コンビニで扱うコモディティ商品なら、24時間いつでも買える。町には様々なカテゴリーの量販店があり、店内をみればいろいろな種類の商品がずらりと陳列されていて、見比べて買うことができる。
一方、例えば、歯科医院で治療に使う歯のかぶせ物(クラウン)なんかは、人それぞれに合わせて作らなければならない。1~2週間待たなければならない。
前者を見込生産、後者を受注生産と呼んでいる。
1.1 見込生産と受注生産の違い
生産管理ではよく出て来る受注生産と見込生産。生産現場ではどのように違うのか。先ず簡単な例からみていく。図1に見込生産、図2に受注生産のイメージを例示する。

図1 見込生産のイメージ

図2 受注生産のイメージ
見込生産は同一あるいは類似製品を大量に生産する場合に採用される。需要を予測し、生産計画を立て、その計画に基づいて材料を手配し生産する。生産ラインの投入口にはある期間生産に必要な材料を揃えておくのが一般的である。従って生産ラインへの投入は切れ目なく行うことができる。一方、受注生産ではランダムに舞い込む注文ごとに、それぞれに合う材料を準備する。投入間隔がバラツキ、ラインへの投入が遅れることがしばしば。大雑把な違いを表1に例示する。
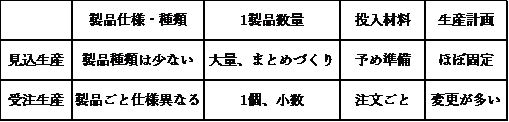
表1 見込生産と受注生産の違い
実際は、見込生産と受注生産の間にはいろいろなバリエーションがある。大量生産でも、大型の取引では、注文を受けて量産することもあり、また、受注生産しているものでも、繰返し性がある場合は、それを見込んで、確定注文が来る前に生産を始めることも多い。ただ生産管理上、見込・受注生産それぞれの特徴を理解しておくことは必須である。
ここでは、それぞれの特徴を「時間」という切り口で解析してみる。ベースとする理論は、前回紹介した「待ち行列理論」。平均投入間隔(到着間隔);Ti、その変動係数;Sti、平均処理時間;Tp、その変動係数;Stp、平均待ち時間;WT、平均手空き時間;FrT、稼働率;ρとして、見込・受注生産の特徴の一例を表2に示す。

表2 見込生産と受注生産での主要時間要素の比較
見込生産では、生産効率を上げるため、一度に作る数量をできるだけ多くする傾向があり、仕掛在庫は多くなりやすい。しかし、程度の差はあるが、生産計画をベースとした管理は可能。受注生産ではTiやTpのバラツキ要因が外部にあるところが多い。そのため、ρを高くすると、WTが長くなると同時に不確定性も高くなり、生産リードタイムの管理精度が低下して納期管理が難しくなる。
1.2 シミュレーションでイメージをつかむ
記号を並べただけでは分かりにくいので、それぞれの時間要素がどのような特性になるのか、シミュレーションで確認してみる。工程A~Eの5工程直列生産ラインを例に、表3にシミュレーション条件を示す。
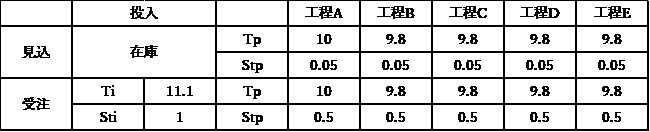
表3 シミュレーション条件
見込生産では投入口に材料在庫が準備されていて、工程Aが必要な時はいつでも投入可能。工程Aの平均処理時間(Tp)は10分のガンマ分布、工程B~EのTpは9.8分。すべての工程の変動係数(Stp)は0.05とする。
受注生産では平均投入間隔(Ti)は11.1分、その変動係数(Sti)は1の指数分布を使う。工程AのTpは10分のガンマ分布。工程Aの稼働率(ρ)は90%となる。工程B~EのTpは9.8分。すべての工程のStpは0.5とする。
調べたい特性は投入から完成までの処理時間の合計と各工程前でワークが待つ時間の合計、それに投入から完成までの時間;フロータイム(FT)とする。図3に見込生産、図4に受注生産でのシミュレーション結果を示す。また、表4にそれぞれの平均値と標準偏差値のシミュレーション結果を示す。
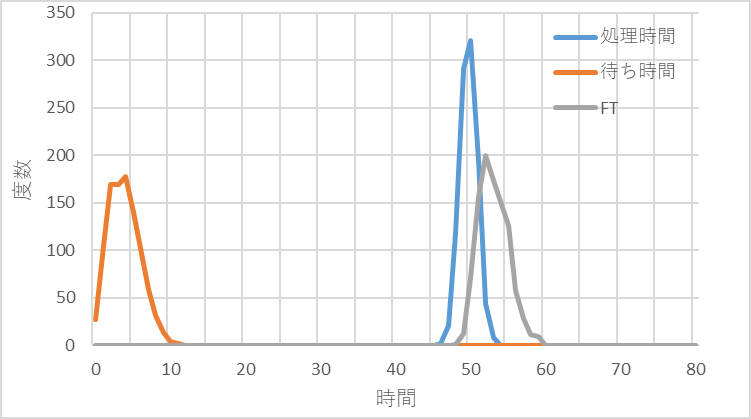
図3 見込生産ラインでの処理時間(Tp)、待ち時間(WT)、フロータイム(FT)
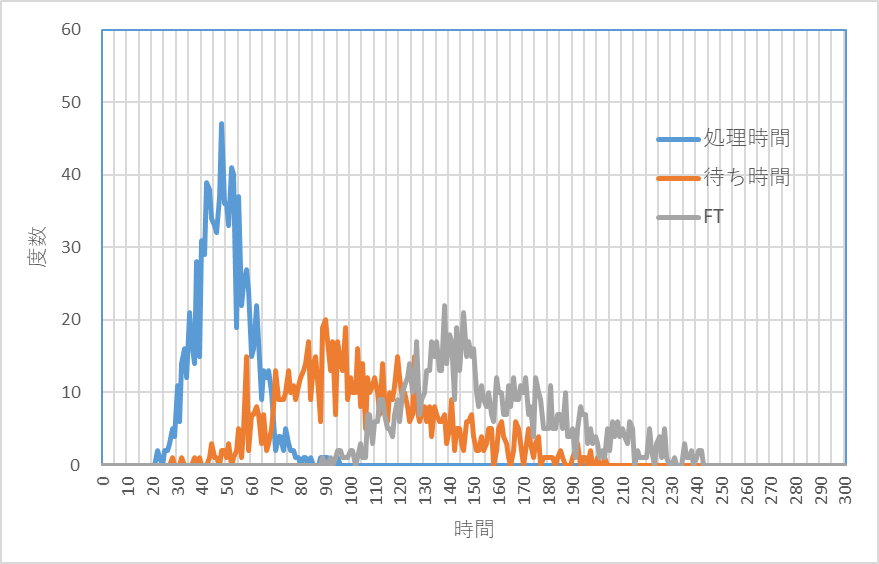
図4 受注生産ラインでのTp、WT、FT
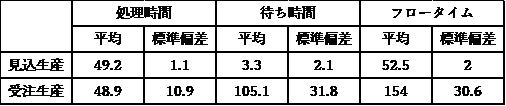
表4 シミュレーション結果;投入~完成までの処理時間、待ち時間、フロータイム
両者間で最も顕著な違いはフロータイム;FTである。見込生産では平均が52.5、標準偏差が2.0に対して、受注生産では平均が154.0、標準偏差が30.6。違いの要因は待ち時間である。見込生産では待ち時間の平均が3.3であるのに対し、受注生産のそれは105.1、標準偏差は2.1に対して31.8。この現象は、前回紹介した「待ち行列理論」で説明することができる。
1.3 工場、企業単位でみると
見込生産と受注生産の違いを5工程直列の生産ラインを例にみてみたが、工場あるいは企業という枠で俯瞰してみれば、生産の流れはもっと複雑である。工程も、機械が主体の加工工程、たくさんの部品が集まる組立工程、あるいは、熱処理、塗装、、などなど。それらの区画をここでは、セグメント と呼んでおく。管理単位となっている場合も多い。
工場、企業という枠でみた場合どうなるのか。セグメント単位にみた場合の見込生産と受注生産でのイメージを図5、図6に示す。
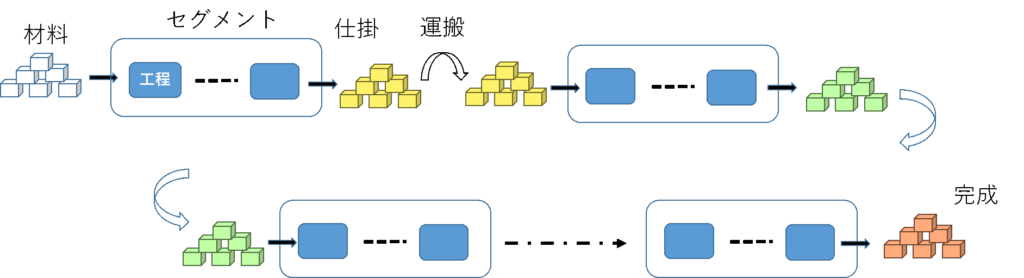
図5 セグメント単位でみた見込生産のイメージ
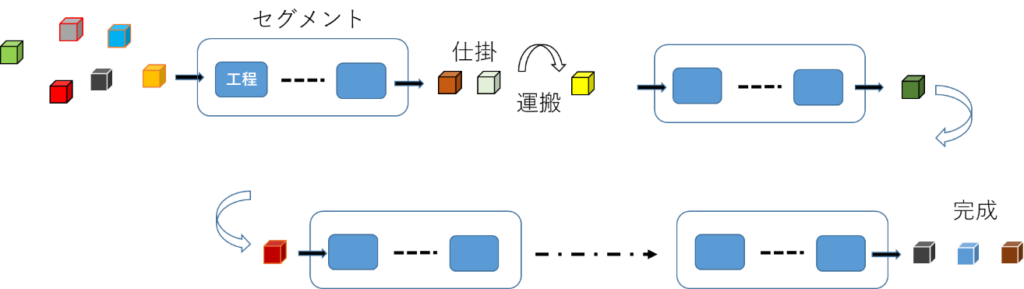
図6 セグメント単位でみた受注生産のイメージ
両者の違いはセグメント間の仕掛状態である。見込生産の場合の仕掛は同一品種であるが、受注生産の場合の仕掛は1個(あるいは少数個)づつ異なる。滞留させずに仕掛発生ごとに運搬すれば、待ち時間はない(短い)が工数はかかる。まとめて運搬すれば待ち時間が長くなる。
運搬をひとつの工程と考えればわかりやすい。工程を「素材に何らかの変化を与えるプロセス」と考えれば、運搬は「ワークの位置を変える」工程である、と言える。そうみると、受注生産の場合は、工程間もセグメント間も、根本的な違いはない。受注生産での工程間の待ち時間/仕掛数 は、先に5工程直列ラインでみたように、稼働率;ρに対して指数関数的に待ち時間が長くなる/仕掛が多くなることである。その分布形状もだだっ広く、統計的分析をしても実用的な管理精度を得ることが困難な場合が多い。
生産計画・管理ツールとして、見込生産の場合はMRPIIが普及している。受注生産の場合は、生産スケジューラが使われることがあるが、待ち時間発生の不確定性があるため、ごく限られた条件以外は、有効利用は難しい。仕掛・待ち時間に注目した両者の比較を表5に簡単にまとめた。
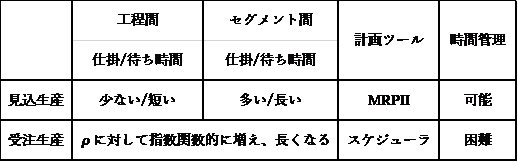
表5 仕掛、待ち時間に注目して
2、GKCの時間概念;基本的理解の欠如
モノづくりに関する時間概念でもっとも基本的なものは、見込生産か受注生産かを決める時間であると考えられる。注文を受けてから生産を開始するか、注文が決まらない時点で生産を開始するか、つまり「生産開始」時刻と「受注決定」時刻の前後関係で生産管理はガラリと変わる。
GKCの時間概念を調べるため、見込生産か、受注生産か、をキーワードに斬り込んでみた。最初に大ナタでバッサリと斬り込んで、その後で、細部をみてみるつもりだったが、初めの一振りで結論は出てしまったようだ。
先ず、最初に挙げておかなければならないことは、GKCでは、見込生産と受注生産の違いについての言及がまったくないことである。「2種時間概念」でも、それらに関する説明はどこにもない。生産開始時に受注が決まっているか、いないのか、が生産管理上重要な条件であるという認識がないことの証左でもある。これはGKCの論理基盤を毀損する致命的な瑕疵となりうるのではないか。
先に例示した生産ラインの基本特性をザックリとまとめ直すと表6のようになる。ひとつの工程に注目すれば、横列に示すワークが到着する平均時間間隔;Tiとその変動係数;Sti、工程の平均処理時間;Tpとその変動係数;Stp が独立変数で、縦列の稼働率;ρ、待ち時間;WTが従属変数。生産ラインとしてみた場合、縦列のTp合計、WT合計および生産リードタイム;LT(FTと同じ)が従属変数。
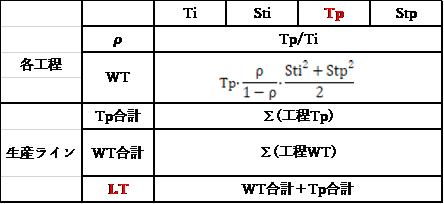
表6 時間要素でまとめた生産ラインの基本特性
表6に示した関係は、見込生産、受注生産の区別なく、一般的な離散型生産ラインに共通して適用できる。
「2種時間概念」に戻ってみよう。そこで言及している時間要素は「直接作業時間」と「リードタイム」だけである。「直接作業時間」と「リードタイム」は、表6ではそれぞれ Tp とLT に当たる。その他の項目についての言及はまったくない。
しかも、「直接作業時間」についてはトヨタ本から“コピペ”してきたような“現場改善用語”だけで、生産ラインのメカニズムについての説明はほとんどない。さらに「リードタイム」については、
生産リードタイム=1/(情報受信スピード×情報受信密度)
という意味不明な数式で生産リードタイムを説明する「設計情報転写論」を引っ張り出している。このような「妄想論」に依拠したことにより、時間概念のベースは支離滅裂、完全に破綻している。箸にも棒にもかからない、のである。
GKCの論理基盤に時間概念がどのような影響を及ぼしたか、という視点で「2種時間概念」を調べてみた。生産管理でもっとも基本的な「見込生産」と「受注生産」から入り、そこから生産現場の細々した日々の改善活動をみてみようと思っていたが、入り口に入るや否や、結論は出てしまった。
文系的に表現すれば、結論は、
現場改善会計論は、
豪華に聳え立つ “砂上の楼閣” か、
地平で怪しげに揺らぐ “蜃気楼” か・・・。
いずれにしても、実体のない理論である。
3、GKCの事例は特殊か?
東大、京大教授の流れを踏襲し、数年に渡り研究してきたGKCの論理構成はまったくの“マトハズレ”であることが判明した。一ヶ所や二ヶ所の間違いなら直しようもあるが、基本的、根本的なところが “デタラメ” だと、GKCそのものの存在価値はない。価値がないだけならまだいい。教職にある教授陣が発信する情報であることを考えれば、その悪影響は後世までも及ぶ。
GKCにかかわる教授陣は、今今も、“百害あって一利なし”たる低劣な情報を飛散、拡散させ続けているのである。
問題は、そして疑問は、なぜ、これほどまで間違いだらけのGKCが世に発表され、学会から表彰を受けることができたのか。その背後には、かつて製造大国と呼ばれた日本がいまや先進国での最下位を通り越し、中進国の仲間入りしそうな状況となっていること、や、日本の大学の世界ランク低落など、の理由と重なるところがあるとすると、、
GKCの事例は特殊ではない、のではないか・・・。次回はその辺りを、、。