OJTソリューションズ(以下、OJTS)は、矢橋林業(株)で行われた「現場力の向上Project(以下、現場力PJ)」の指導にあたりました。が、現場の技術者は「手待ちのムダが一番のムダだ」と認識しながら、その課題を解決できていないようです。OJTSのトレーナーはどのような指導をしたのでしょうか? その背景を生産ラインの物理特性の視点で、見込生産と受注生産、待ち行列現象の切り口で分析してみますと、OJTSのトレーナーは生産ラインの基本特性を理解しているのだろうか? という疑問が湧いてきたというのが前回の話。
トヨタで40年以上の経験を持つトレーナーの専門知識に疑問符が付くとなると、穏やかではありません。
生産方式としてbest of the best だと世界で認められているTPS。多くの企業が導入しようとしてきましたし、目下、TPSに習って改善活動を進めている企業もたくさんあります。そのような企業に、正しい支援サービスを提供するのがOJTS。OJTSはどのような考え方でトヨタベースの改善活動支援サービスを提供しているのか、気になってきました。
OJTSの会社紹介動画を覗いてみました。関連するところをピックアップします。
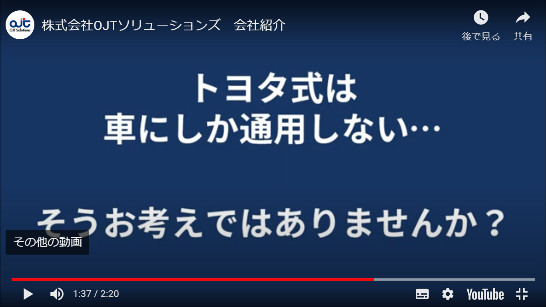
(ナレーション)
トヨタ式は車にしか通用しないのではないか。そういった言葉を多くのお客様よりお聞きします。みなさまもそうお考えではないでしょうか?
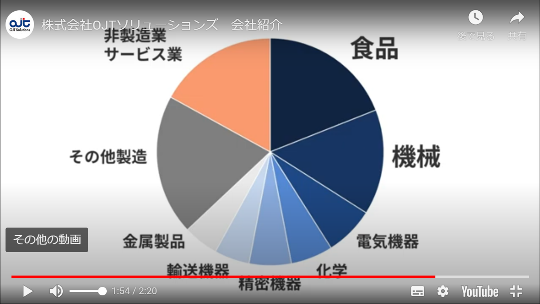
( ナレーション)
トヨタ式の本質はどのような業種にも通用します。
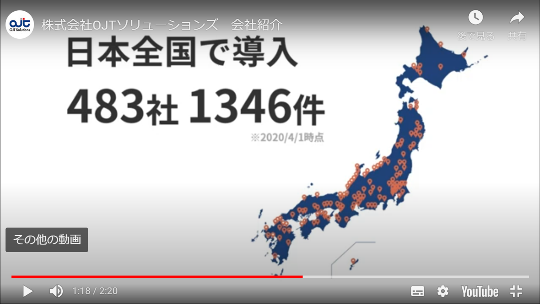
(ナレーション)
これまで日本全国483社、1,346件のプロジェクトのお手伝いをしてきました。
どの企業も、自社が提供する商品やサービスに対する顧客の印象やニーズには敏感です。
「トヨタ式は車にしか通用しないのではないか? そういった言葉を多くのお客様よりお聞きします」
このようなネガティブ・フィードバックを使う余裕さえ感じられます。
「トヨタ式の本質はどのような業種にも通用します」
これを異次元的汎用性と呼んでおきます。そして、異次元的汎用性の裏付けとしたいのでしょうか、
「日本全国483社でお手伝いをしています」
と自信をのぞかせます。
OJTSは顧客企業を食品・機械・電気機器・・・サービス業と業種で分類しています。業種によってつくるモノが異なり、つくり方も異なりますので、汎用性をみるのに異業種という切り口はそれなりに意味があると思います。ただ、業種間の違いは多岐にわたり、それらと生産システムの相性とか適合性を確認するとなると、大変な作業になりそうだし、うまくまとめることができるかどうかもわかりません。
ここでは、逆に、生産システムの特性側から様々なモノをつくる場合の整合性をみた方がわかりやすいのではないかと思います。ということで、初めに、TPSの基本的な特徴を確認しておきます。
TPSの特徴は?、といえば・・・そうですね、Just In Time。もうひとつ、ニンベンが付いた自動化、っていうのがありますが、ここでは、話を複雑にしないために省略します。
Just In Time って、必要なモノが必要な時に必要な数量届くっていうことですよね。例えばひとつの工程を考えてみますと、作業開始時刻直前に前工程から流れてくるということ。遅れてくれば工程で手待ちが生じます。これは「手待ちのムダ」。じゃ、ずーっと前に到着していればいいか、というと、今度はモノが待つことになります。これは仕掛の滞留(「在庫のムダ」)となります。「手待ちのムダ」に「在庫のムダ」。ムダをなくすためには、Just In Time に到着させなければならない、ということですね。
ここで、クエスチョン。Just In Time はどのような生産環境でも可能でしょうか?
OJTSは、
「トヨタ式の本質はどのような業種にも通用する」
と説明しています。「トヨタの本質」をここではわかりやすいように「Just In Time」に置き換えてみます。
「Just In Time はどのような業種でも通用する」
Just In Time はどのような業種でも成立するか? Just In Time が成立する条件って、どのような条件でしょうね。ある工程で作業(加工、組立、、)が始める直前にワーク(被処理物)が流れてくるようにするための条件です。
工程で作業が始るのはいつか? 一般的には次のようになるのではないでしょうか。
- (仕掛がある状態では)現行の作業が終わったとき
- (手待ち状態では)ワークが流れて来た時(それまで待つ)
- スケジュールで開始時刻を指示されている場合は、
(仕掛有状態)指示時刻が過ぎているときは直ちに開始。まだの場合は指示時刻まで待つ
(手待ち状態)ワークが流れてくるまで待つ
1.は「在庫のムダ」、2.は「手待ちのムダ」が発生している状態です。3.は作業の開始と終了時刻を指示している場合ですが、ちょうど開始時刻に間に合うように前工程からワークが流れて来るかどうかが問題です。一般の生産ラインでは、スケジュール時刻と実作業時刻に乖離があり、その差が大きくなるとスケジュール通り作業ができなくなります。
TPSではJust In Time をどのようにして実現しているのでしょうか。
Just In Time 成立の条件ってどんなことなのか、ひとつの工程で考えてみます。
最も基本的な条件は、
前工程からその工程に到着する時刻=工程での処理終了時刻
となります。簡単に、
到着時刻=処理終了時刻
としておきます。これを実現する方法として、
到着時刻間隔=処理時間
が考えられます。その工程の処理時間は次の工程の到着時刻間隔となりますので、この関係がすべての工程間で成立すれば、Just In Time で流れることになります。この関係を外注や部品納入業者にも適用すれば全体のサプライチェーンがJust In Time でつながることになります。
これをトヨタはどのようにして実現しているかは、トヨタ本の解説をご参照いただくとして、ここではJust In Time と関係の深いトヨタ語を二つ、三つ挙げておきます。
<平準化>
到着時刻間隔=処理時間 にするためには負荷を一定にする必要がありますので、平準化は最も重要な条件となります。
<タクトタイム>
到着時刻間隔=処理時間=タクトタイム となります。
<標準作業時間>
タクトタイムを安定させ且つ改善(短縮)するために標準作業の維持管理が重要です。
その他にも重要な考え方やツール、ルールはたくさんありますので、トヨタ関連書をご参照ください。
ただ、トヨタ関連書でもあまり良く説明されていないことがあります。あまりにもありふれたことだからでしょうか。それは・・・
生産計画固定
です。生産計画を固定するためには見込生産でなければなりません。この条件を外すと、Just In Time は成り立ちません。但し、Just In Time の基準、つまり手待ち時間が〇〇分以下とかという基準はありませんので、トヨタを基準とすれば、トヨタのようなJust In Time はほぼ不可能だ、ということになります。
受注生産では生産計画をある期間、例えば月間、固定することは至難のワザです。限定的な範囲で短期間固定することはできても、見込生産での生産計画のように安定的に固定することは、ほぼ、不可能に近いのではないか、と考えられます。
業種と見込生産、受注生産との関係はどうなってんでしょうか。業種によってはほとんどが受注生産だよ、という業種もあるかもしれませんが、同じ業種でも製品やサービスの違いで受注生産もあれば見込生産もある、というのが一般的ではないかと思われます。
ですから、OJTSが「どのような業種にも通用する」という表現は、正しくないのではないか、と思います。正しく表現するのであれば、
「見込生産で実行可能な生産計画を固定できれば、どのような業種にも通用する」
ということになるのではないかと思います。
矢橋林業(株)の現場力PJに戻ってみます。矢橋林業(株)は見込生産でしょうか? 受注生産でしょうか?
典型的な受注生産ですね。中には見込生産品もあるかもしれませんが主流製品ではないでしょう。大部分は受注生産・・・ということは、矢橋林業(株)ではJust In Time の実現は? ほぼ不可能、ということになります。
Just In Time に変わるTPSをベースにしたソリューションは、なにか、あるんでしょうか。受注生産でもJust In Time が成立する方法はTPSにあるのでしょうか。矢橋林業(株)の現場力PJの現場の技術者の声を聞く限り、OJTSからの提案は何もないようです。
日本の製造業と建築業の企業数は約76万社。そのうち99.7%は中小企業(2021年、中小企業庁)だそうで。この実態から推定しても、OJTSが支援した483社の大部分は中小企業ではないかと思われます。そして中小企業の特徴は、多品種・少量・変量の受注生産。矢橋林業(株)も典型的な中小企業です。
OJTSの導入事例として下記の4社が紹介されています。
- オリンパス(株)
- (株)坂角総本舗
- 日精エー・エス・ビー機械(株)
- 尾道さつき会
1~3 は主に自社設計の製品を製造していて、規模は大企業。計画サイクルはそれぞれ異なると思いますが、見込生産が主であると思われます。4 は介護サービス業ですが、タスクにリソースをあてがうというプロジェクト型の要素があり、この場合、待ち行列現象を抑制する方法があります。つまり、事例の4例は比較的結果を出しやすい環境の企業ばかり。
483社の大部分は中小企業で、多品種・少量・変量の受注生産。そのような企業でOJTSが指導した改善活動の結果はどうであったか、矢橋林業(株)の結果をみればわかります。
「一社だけで、わかりますか?」
「ええ、わかります。それぐらい、決定的な現象なんで、、」。
ここで、一旦、まとめてみます.
[OJTSのメッセージ]
「トヨタ式の本質はどのような業種にも通用します」というメッセージでトヨタ式(TPS)はどのような生産環境にも使える万能の生産方式である。また、トヨタの現場で40年以上の経験を持つトレーナーはTPSについて熟知しており、製造業だけではなくサービス業も含めてあらゆる業種で改善の指導をすることができる。
[これを裏から観ますと]
トヨタでは、見込生産・生産計画固定をベースにしたJust In Time の仕組みの大枠は、1970年代にはほぼ出来上がっている。OJTSのトヨタ出身者の知識は、待ち行列現象がほとんど目につかないJust In Time の仕組みができあがった現場で会得したものであり、待ち行列現象を認識していないのではないか。
多品種・少量・変量の受注生産環境では待ち行列現象が必然的に発生し、原理的にJust In Time は成立しない。OJTSのトヨタ出身者は、多品種・少量・変量の受注生産環境での改善の知識はまったくなく、その指導能力はないと思われる。
羊頭狗肉
OJTSは、TPSはあらゆる業種に通用する万能な生産方式であるかのように見せかけ、そして、トヨタ出身者はあらゆる業種にTPSを移植する能力があると喧伝する。
OJTソリューションズのメッセージは羊頭狗肉になっていませんか?