前回は、現場改善会計論が依拠している「設計情報転写論」(藤本隆宏元東大教授)とトヨタ生産方式(TPS)、および共同執筆者の上總康行京大名誉教授をたどってみたら、ぼんやり見えてきたのが、いや、なにもみえない空洞みたいなものなんですが、「ものづくりの盲点」かな、という話。で、「ものづくりの盲点」と関連するキーワードを二つ挙げました。
見込み生産
待ち行列現象
と、言っても、ピンときませんね。今回は、この辺りを少し、掘り下げてみたいと思います。
矢橋林業(株)の改善事例
題材はやはり「現場改善会計論」。下記の関連文献があります。
現場改善会計論の提唱―原価管理から余剰生産能力管理へ―
著者;柊 紫乃 日本管理会計学会誌 管理会計学2023 年第31 巻第2 号
この中に、矢橋ホールディングス(株)の傘下にある、注文住宅、分譲住宅の設計、施工、販売などを手掛けている 矢橋林業(株)での「原価プロジェクト」の事例紹介があります。矢橋林業(株)の国内従業員数は174名(2024/1)。規模でいえば中小企業に分類されます。
矢橋林業(株)の関連資料を調べてみると、状況は次のようです。
*2014年~2019年、連続して赤字である。
*原価のみえる仕組みが不十分であることが問題。
*矢橋流原価管理の再構築が必要である。
*これまでも、TPSに基づく現場改善活動が行われていた。
*現場改善活動強化のため(株)OJT ソリューションズ (以下、OJTS)の指導を受ける。 ➡現場力の向上Project(以下、現場力PJ)
*現場改善活動と会計業務を連動させる必要がある。
➡会計の見える化Project(以下、会計PJ)
*矢橋流原価管理の再構築期間;2019年11月~2022年6月の約2年半
下図は「現場改善会計論の提唱」にある「矢橋流原価管理の再構築」の説明図です。
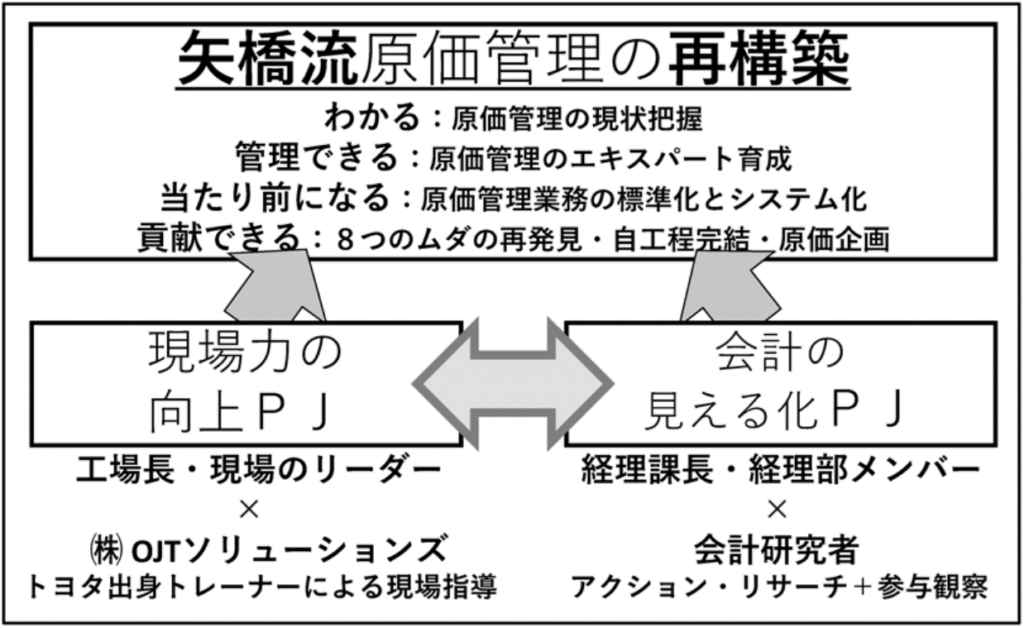
現場力PJ
これまでは主に会計に注目してきましたが、今回は主に「現場力PJ」の活動をみてみたいと思います。
(株)OJT ソリューションズ
「現場力PJ」を支援したOJTSのトレーナは全員がトヨタ出身者(76名、2021/10時点)。OJTS紹介動画(YouTube)をご参照ください。
OJTSの企業理念と事業価値について、同社のホームページに次のように書いてあります。
企業理念
モノづくり現場で培った改善と人材育成のノウハウをベースに顧客のモノづくり力と人材育成・活用力を高める。
事業価値
人づくりとしくみづくりを通じて継続して改善成果を上げられる現場をつくり顧客企業の利益に貢献する。
矢橋林業(株)の状況
矢橋林業(株)での改善事例の紹介動画(You Tube)矢橋ホールディングスの改善事例 があります。次のような説明があります。
以前(10年以上前)から改善活動に取り組んでいて、会社としても重要視してきた。しかし、
- 改善で作業性は良くなるが、利益率がどの程度改善されたか見えない。
- 項目ごとの時間短縮はできたが、全体の収支でみてどのぐらい改善されたか見えない。
- 改善効果を時間当り利益として算出してはいたが、邸別原価を正確に把握できていなかったので、改善効果が原価に具体的にどのように反映されるかまでは詰められていなかった。
OJTSからは、「1日どのぐらい時間が短縮できたか」を問い掛けられた。
今は、日報の電子化などやり始めていて、最終的にひと月の中の製造原価、利益率がみえるようになってきている。
矢橋流原価管理の再構築はできたのか?
プロジェクトの成果
プロジェクトの成果として次の五つが挙げられています。但し、企業業績との関係についての説明はありません。
現場力PJ
① 5大管理の管理ボード拡充
② 頻発停止の改善
会計PJ
③ 邸別原価表(原価計算ツール)の構築
④ 運賃課題の連関図による分析
⑤ 全費用のコスト・ビヘイビア分析
ものづくりの生産性は改善できたか
OJTSの指導で進められた「現場力PJ」と会計研究者が支援する「会計PJ」を両輪として展開された「矢橋流原価管理の再構築」の成果はどうだったのか。「矢橋流原価管理の再構築」が目標であれば、前記の①、③、④、⑤の成果で目標は達成した、とみることもできる。しかし、なぜ、「矢橋流原価管理の再構築」が必要かといえば、6年連続の赤字体質からの脱出が目的であることは明らかです。ここでは、一段、掘り下げて、矢橋林業(株)のものづくりの生産性がどのように改善され業績向上に寄与する(した)か、という視点でみてみたいと思います。
分析のキーワードは冒頭に挙げた下記の二つのワード。
見込み生産
待ち行列現象
動画によると10年前ぐらいからTPSに基づく改善活動を進めていたようです。今回の「現場力PJ」ではOJTSの指導が入りました。OJTSのトレーナは、40年以上もトヨタの現場で、本物のTPSを体得した方々です。何が変わったのか。何が変わらなかったのか。
トヨタと矢橋林業(株)の違い
ひとつ目のキーワード「見込生産」の切り口で課題を整理してみたいと思います。
トヨタは「見込生産」でしょうか?
その前に、「見込生産」の対義語は? そうですね、「受注生産」です。両語の定義を確認しておきます。
「見込生産」;どの製品を、いつ、誰が、何個買うか決まる前に生産を開始する生産方法
「受注生産」;どの製品を、いつ、誰が、何個買うか決まってから生産を開始する生産方法
「見込生産」は需要を予測して、生産計画を立てて、それに従って生産を行います。ただ、生産計画を立てても、途中で変更がある場合もありますので、生産計画固定を条件としたいと思います。
一方、受注生産は注文が来てから生産を行います。受注後に生産計画(スケジューリング)をつくり、それに従って生産するという場合もあると思いますが、多品種・少量・変量の場合は投入済みオーダーの状態をベースに新規オーダーのスケジュールを積み上げるなんて言う芸当はできませんので、結局は、詳細スケジュールなしで生産を行うことになります。
つまり、
「見込生産」➡「詳細生産計画固定」
「受注生産」➡「詳細生産計画なし」
ということになります。
で、トヨタは「見込生産」ですか? 「受注生産」ですか? ・・・
月次生産計画でつくるモノは決まっていますので「見込生産」ですね。
では、矢橋林業(株)は「見込生産」ですか? 「受注生産」ですか? ・・・
住宅事業ですから「受注生産」でしょうね。
手待ちのムダが一番のムダ
先に挙げた 矢橋ホールディングスの改善事例 で工場の技術者がこのようなことを述べています。
ラインの方たちにはムダな動作、手待ちのムダが一番のムダだ、と教育した。待ち時間は少(筆者加筆)なくなったが、やはり、まだ、考え込むとか、次に何をやろうかという作業を探す動作がまだ残っているので、ルールというか、こうなったらこうするんだよ、ということまで、指導する側が決めていかなければいけないという課題が残っており、今後取り組んでいくよう考えている。
この課題を解決するためにOJTSのトレーナはどのような指導をしたんでしょうか。動画からは、課題は残ったままで、なんとかしなければ・・・という担当者の“迷い”みたいなものを感じます。
現場でみられる日常茶飯の“手待ちのムダ”。10年以上前からTPSをベースにした改善活動を行ってきた現場でもまだ起きている。「それが一番の無駄だよ」、とOJTSのトレーナから指摘されたんでしょうね。
「Just In Time にモノが流れていない」。「TPSの基本ができていない」。OJTSのトレーナの目から見ればそう見えたに違いありません。
OJTSの指導で「手待ちのムダ」を排除できたか
で、OJTSのトレーナの指導でこの問題は解決したんでしょうか。現場の技術者の話を聞く限り、解決はしていないようです。
トヨタではほとんどわからない程度に排除されている“手待ちのムダ”。矢橋林業(株)ではなぜ、なくすことができないのでしょうか。OJTSの指導があっても・・・なくならない。
その理由は、二つのキーワードの背後に隠れています。トヨタで起きていることと、矢橋林業(株)で起きていることを比べてみると下記のようになります。
トヨタ;
見込生産→生産計画確定→平準化・標準作業・ムダの排除、→サイクルタイム同期生産→Just In Time→待ち行列現象の発生がない(ほぼゼロに抑制)
矢橋林業(株);
受注生産→生産計画確定できず→処理時間・到着時間がバラツク→待ち行列現象が発生
二番目のキーワードに挙げた待ち行列現象が出てきました。簡単に言いますと、見込生産で詳細計画固定のトヨタでは待ち行列現象の発生がない(少ない)が、受注生産で詳細生産計画のない矢橋林業(株)では待ち行列現象が発生する、ということになります。
TPSでは標準時間設定、サイクルタイムでの同期生産等により「手待ちのムダ」の発生を予防していますが、「受注生産」では、オーダーによって処理時間は異なり、受注タイミングもバラバラなので、「手待ちのムダ」を現実的になくすことはほぼ不可能です。また、手待ちは前工程からワークが流れてこない状態ですが、逆に、工程での処理が終わる前にどんどん流れてくることもあります。こうなると、工程前に仕掛の滞留が発生します。「手待ちのムダ」は工程(人、機械、、)が待たされる現象ですが、逆に前工程から流れてくるモノ(ワーク、被処理物、、)の時間間隔が短くなるとモノが待たされる現象となります。「手待ちのムダ」と「仕掛の滞留」は同一工程で同時には起きませんが、生産ライン全体では、手待ちが起きている工程があるかと思えば、仕掛が滞留している工程もある、という状態になります。
手待ちが多いということで、投入を増やして稼働率を上げたりすると仕掛が急に増え、生産リードタイムが急激に長くなってしまいます。
待ち行列現象による待ち時間は、処理時間の数倍、数十倍になり、また、バラツキが大きく確率的な予測が難しく、生産ラインの管理が混乱する大きな要因になります。
トヨタでは待ち行列現象を学ぶことはできない
TPSがほぼ出来上がっているトヨタの生産現場では待ち行列現象をみることはほとんどないでしょう。待ち行列現象を排除してJust In Timeを実現したのがTPSですから、トヨタの生産現場では待ち行列現象は無縁なんだと思います。OJTSのWebsiteの隅々を探しましたが、待ち行列現象への言及はまったくありません。
OJTSのトレーナはTPSの生産環境しか経験ありませんので、受注生産環境では必然的に起きる待ち行列現象の問題を、まったく知らないのも無理はありません。
「異業種にトヨタを導入する」ことを掲げて発足したNPS研究会。会員企業は「受注生産」企業です。支援したのが、TPS生みの親、大野耐一とその弟子、鈴村喜久男。トヨタ直々の指導体制です。発足して数年はメディアでも取り上げられ注目を集めましたが、最近はトヨタの字も消えて、ありふれた経営哲学を旗印にしているようです。これも、受注生産企業にトヨタのやり方でTPSを導入しても、トヨタを再現することはできない証左ではないでしょうか。
簡単にまとめておきますと、TPSは待ち行列現象を極小化しJust In Timeを実現していますが、それを可能にしてる条件は「見込生産」で詳細な生産計画を固定していること。生産計画を固定できない「受注生産」では、TPSのツール、ルールで待ち行列現象を抑制することはできない、ということになります。
OJT ソリューションズはTPSの弱点を自覚しているのでしょうか?