現場改善会計論(GKC)をはじめて読んだとき、正直、何が書いてあるのかさっぱりわかりませんでした。何度か読み返すうち、なんとなく、著者の狙いは感じ取れるようになりましたが、逆に疑問点が次々と、。その中身も高度というよりは「なんで、こんな?」というような低レベルのものばかり。探求心というよりは変な好奇心が出てきて、関連する上總康行名誉教授の「現場改善効果の見える化―機会損失を組み込んだ現場改善会計論―」を読んでみて、「な~んだ、元が間違っているんだ」とわかったのが前回のブログ。
今回は、一連の “GKC見学ツアー” をまとめてみたいと思います。
1,現場改善会計論(GKC)が設定した前提条件
GKCは次の三つを前提として論じられているようです。
- 部分改善で余剰生産能力が創出される。
- 生産ラインは線形モデルである。
- 部分改善を金額評価して全体の改善評価額に結び付けることができる。
例えば、上總康行名誉教授の「現場改善効果の見える化」には次のような説明があります。
ある工程の作業時間が8時間から6時間に短縮した場合、賃率が1,000円/時間だとして、改善効果は2,000円(2時間×1,000円/時間)である。また、2時間の時間短縮で2時間分の生産能力が増強される。この生産能力増強分を会計的利益にするためには受注獲得のための営業・経営努力が必要である。
部分改善で余剰生産能力が創出される、と主張されているようです。実際は、多くの場合、生産ラインは複数工程で構成されていますので、1工程で8時間から6時間の短縮で生み出された2時間でどれだけの受注増加に応じられるのか。5工程から成る生産ラインで、各工程1時間かかるとすれば、1個作るのに5時間必要です。2時間では1個もできません。改善した工程は動き回らないボトルネック工程だ、とか、全工程で2時間短縮できた、ということなら別ですが、、。そんな説明はどこにもありません。
②については、生産ラインの中をワーク(被処理物)が流れるとき、さまざまな変動・バラツキが重なります。そのような生産ラインで稼働率が高くなると工程前の仕掛が急激に増え出し、リードタイムも指数関数的に長くなります。つまり、非線形特性を示します。ところがGKCでは、このような現象についての記述はまったくありません。
③ についても、2時間の作業時間短縮で2,000円の改善効果だ、と当然のことのように金額評価して、企業の利益に結び付けようとします。
2,GKCが依拠したものとその前提条件を対比
GKCが依拠したのは上總康行名誉教授の管理会計論、トヨタ生産システム、藤本隆宏教授の設計情報転写論の三つ。これらが、GKCの前提条件である
「部分改善で余剰生産能力が創出される」、
「生産ラインは線形モデルである」、
「部分改善を金額評価して全体の改善評価額に結び付ける」
がどのような関係にあるのかを探ってみたいと思います。
以下、依拠した上總康行名誉教授の管理会計論を「会計論」、トヨタ生産システムを「TPS」、藤本隆宏教授の設計情報転写論を「転写論」と略記します。
依拠した会計論、TPS、転写論の特徴
問題構造を解析する手法として、現実の事象を簡略化・抽象化して、図や数式などで表現する「モデル化」があります。今、問題にしている生産ラインの特性、メカニズムを理解するために、この手法を利用してみたいと思います。
先ず、会計論、TPS、転写論それぞれのメカニズムとか、論理構造とか思い浮かべるとき直観的に感じることは、線形モデルなのか非線形モデルなのか。線形と非線形の違いは、ひらたくいえば、二つの変数の関係をグラフで表したとき、直線になるのが線形、そうでないのが非線形ということでしょうか。専門的にはもっと正確な説明が必要かもしれませんが、ここではこんな程度にしておきます。
TPSは線形、一般の生産ラインは非線形
具体的な例で考えてみましょう。直列5工程の生産ラインがあるとします。各工程の処理時間はどの工程も1時間ピッタシ。投入口には材料が十分にあるとして、この生産ラインに投入したワークの生産リードタイムは、、5時間ですね。8時に作業を開始、1時間の昼休み、17時に終了とすると、1日何個完成するか。この計算は比較的簡単です(計算方法は省略します)。
また、生産を開始するとき、生産ラインには仕掛がまったくないのか、前日17時で終了した状態から翌日に再開するのか、で違ってきます。でも計算はできますよね。いつ、生産を開始したら、いつ完成するかもわかるし、合理的な生産計画であれば、製品が何個できあがってくるかもわかりますね。単純な加減乗除算で計算できる。こういうのは線形モデルじゃないかと思います。
一方、多品種少量変量・受注見込混合生産では、注文が入るタイミングもバラバラ、注文品の加工時間もバラバラ、いつ完成するかはベテランのKKDが頼り、というところが多いのではないでしょうか。注文が少ないときはだいたい納期通りにできてたものが、繁忙期になると納期遅れが続出なんていう経験をお持ちの方は多いと思います。単純な加減乗除算で計算できるわけではありません。こういうのは非線形モデルじゃないかと思います。
で、TPSはどちらでしょうか。線形?それとも非線形? サイクルタイム(タクトタイム)がわかれば1日の生産数はわかるし、かんばん枚数を求める計算式も多少複雑にはなりますが、電卓で簡単に計算できます。厳密な話ではなくて、常識的なザックリ感でいえば、TPSは線形モデルだと考えていいんじゃないかと思います。
また見込大量生産を行っている大企業では、ERP、MRP等のITシステムで管理している工場が多いと思います。まとめづくりしますので、仕掛在庫は多くなり、また、需要変動に対する追従性(生産リードタイム、月次とか週次等の生産管理サイクル、、が影響)が悪いための欠品、過剰在庫発生などの問題はありますが、ひろく利用されています。これも線形モデルとして扱えるのではないか、と思います。
トヨタ、大企業の見込生産以外の、特に多品種少量変量・受注見込混合生産の中小企業は、非線形モデルだと考えておきます。
会計論は線形
では、会計論は、どちらでしょうか。会計って、過去のある時点と次の時点の経済価値(金額)の出入りを集計して損益を計算しているんじゃないでしょうか。活動(生産、営業等、、、)の結果の会計評価、つまり、将来のことではなく過去の活動の結果を会計評価する。ですから、生産ラインの特性が線形だとか非線形だとか、は会計処理には関係ないと考えられます。のであれば、会計計算の中身は単純な加減乗除。会計の周辺には、償却率とか複利計算とか、非線形っぽいものもあるようですが、会計計算には関係なし、ですよね。だから会計評価は線形モデルと考えていいんじゃないのかなぁ。間違いであれば、ご指摘ください。
転写論は線形? 非線形?
転写論はどうでしょうか? 藤本隆宏教授は転写論で「良い流れの実現」を主張しています。ポイントは「流れ」という現象は線形、非線形のどちらのモデルで扱えるか。「流れ」といっても様々な流れがあります。川の流れ、人の流れ、雲の流れ、、そして生産ラインを流れるワークの流れ、、。
「生産ラインの流れ」って、特殊でしょうか。いや、どこにでもありますよ。日常生活の中でよく見かけます。昼下がりのATM、スーパーのレジ、評判の良いラーメン屋さん、少し前ですがコロナワクチン接種会場、、、などでできる列。この列の長さで「流れ」の良し悪しを判断できます。列の長さが長くなれば「流れ」が悪くなってきている、短くなってくれば「流れ」が良くなってきている、という感じです。
街中で見かけるこのような待ち行列と生産ラインの各工程前で滞留する仕掛の列は同じモデルで記述することができます。つまり、日常の経験則が生産ラインの流れにも応用できるということです。どんな特徴があるかといいますと、来客間隔が短くなり、ある程度以下になると急激に待ち行列が長くなる。しかし、行列が短くなり出すのにはしばらく時間がかかる、という感じでしょうか。
生産ラインでも同じような経験をされているのではないかと思います。受注が増えだすと急激に工程内仕掛が増え出し、減らそうとしてもなかなか減らない。
藤本隆宏教授の転写論では「良い流れの実現」を主張してはいるんですが、「流れ」具合を記述する待ち行列現象についての合理的説明がないんです。設計情報を媒体(材料)に転写したものが製品だ、という抽象化だけなら実害はないのですが、「良い流れの実現」という物理現象を取り込んでいるにもかかわらず、科学的、物理的、工学的に合理的な説明がない。
生産リードタイムについては、
生産リードタイム=1/(設計情報受信の速度×受信密度)
という数理モデルで説明してはいるんですが、本人に式の意味をお聞きしたところ、「文系的表現」だそうで、、。
藤本隆宏教授の転写論では「流れ」の良し悪しを象徴する生産リードタイムの記述が “デタラメ”。
つまり、転写論は本来なら非線形モデルなんですが、非線形特性が無視されているため、その論理展開は支離滅裂、使いものになりません。
日本の製造企業数は全体の99.5%の66万社が中小企業、大企業が4千社だそうです。GKCが対象にしている企業は、特に限定してはいないので、大部分は一般の製造中小企業だと解せます。その生産環境は、多品種少量変量・受注見込混合生産が大部分。ほとんどの企業は非線形モデルである、と考えられます。
GKCが対象としているのは、事例にもある矢橋HD(株)ような中小製造企業だと思われます。
以上、まとめますと、
*TPSは線形モデルである
*一般の生産ラインは非線形モデルである
*会計論は線形モデルである
*転写論は、本来は非線形モデルであるはずだが、非線形特性の記述がない
「部分改善で余剰生産能力が創出される」に対する会計論、TPS、転写論
GKCが前提としている「部分改善で余剰生産能力が創出される」とする考えに近いのは会計論、TPS、転写論のどれか。TPSの解説書にはそのようなことがはっきりと書いてはありません。転写論では、各工程の設計情報転写時間を合計して1個当たりの「正味作業時間」としているところから、部分改善=全体改善という考えであることが判ります。会計計算はもともと、生産ラインの物理的特性を考慮せず、線形モデル的な加減算集計を行いますので、部分改善=全体改善という考え方に抵抗はない(少ない)のではないかと思われます。
「部分改善を金額評価して全体の改善評価額に結び付ける」に対する会計論、TPS、転写論
「部分改善➡全体改善」の部分は前項で言及済ですので、ここでは「部分改善を金額評価する」という部分に注目します。GKCの論文そのものに、「TPSでは部分改善を金額評価することはない」と説明しているにもかかわらず、金額評価を行うのはなぜか。論文からはその理由をはかり知ることはできません。
そこで、推測になりますが、
*多くの企業で、従来から改善活動は「コストダウン」と呼ばれていて、改善効果の評価を金額で行っていた
*企業の業績は会計評価(売上、利益額、利益率、、)である
*現場のコストダウンと企業の業績を結び付ければわかりやすくなる
と考えたのではないか。
転写論と金額表示の関係についてはっきり説明しているところはないようですが、転写論をサービス業等にも拡大していますので、金額評価そのことには、抵抗はほとんどないのではないか、と感じます。
会計論との関係では、会計で金額評価をすることは当たり前 。門前払いです。
まとめ
検討結果を表1にまとめてみました。〇印は「許容する」、×は「許容しない」を示します。大雑把ではありますが、感触はつかめるんじゃないかと思います。TPSも会計論も線形モデルというところが、ちょっと、紛らわしいのですが、TPSは物理的、会計論は会計的に線形である、ということで両者はまったく異なることにご留意ください。(4,トヨタが改善効果を金額評価しないのはなぜ? で詳述)
表1を概観してわかることは、GKCと親和性がある(近い)のは会計論と転写論。
GKCが対象としている一般の生産ラインとGKCの前提を比べてみれば、すべての項目で対立的であることが判ります。このミスマッチが、GKCの論理的合理性を損ない、命脈を絶つ結果につながることが懸念されます。
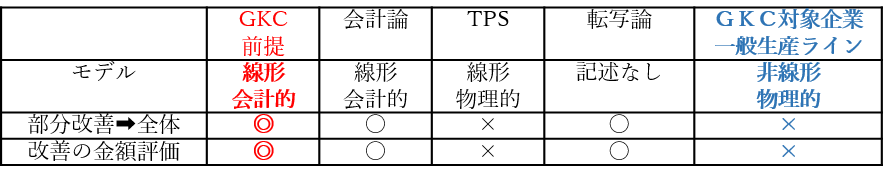
表1 GKC、会計論、TPS、転写論、一般の生産ラインの特徴まとめ
3,非線形特性の正体は?
生産ラインの特性を線形と非線形という切り口でモデル化しました。ここで、非線形特性はどのようなメカニズムで起きているのか、について考えてみます。
非線形特性の正体は「待ち行列現象」です。非線形特性を持っている待ち行列現象ってどんな現象なのか、簡単に説明しておきます。
図1をご覧ください。原材料は常にあり、第1工程に供給されます。第1工程で処理後、第2工程で処理され完成します。第1工程と第2工程間の移動時間は無視します。第1工程の平均処理時間をTp1、変動係数をStp1、第2工程のそれぞれをTp2、Stp2とします。第1と第2工程間にある仕掛在庫がどのようになるかを考えてみます。
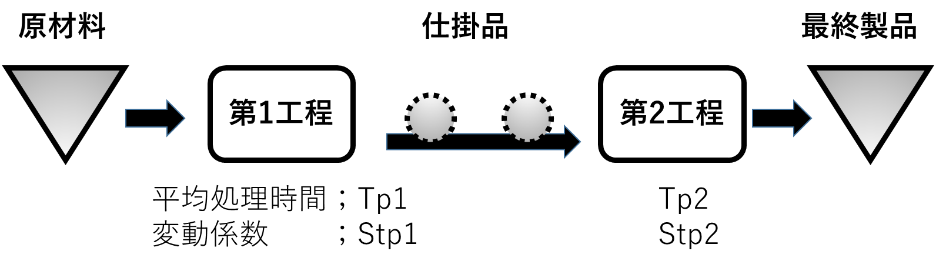
図1 2つの工程間で発生する仕掛
はじめに、Tp1もTp2もバラツキのない固定値の場合を考えてみます。但し、立ち上がりは除きます。Tp1とTp2の組み合わせは表2に示すように3種類あります。Tp1>Tp2のとき、例えばTp1が1.2分、Tp2が1分だとすると、第1工程から第2工程に供給されるワークの時間間隔は1.2分、第2工程の処理時間は1分なのでその前で待つ仕掛はありません。Tp1=Tp2の場合は、第1工程の処理が終了すると同時に第2工程の処理が開始されますので、この場合も仕掛はありません。Tp1<Tp2の場合は第1工程の処理が終わっても第2工程は処理中なので、その前で待たなければなりません。
すでに、いくつかの滞留仕掛がある場合を考えてみます。Tp1>Tp2のときは時間の経過とともに仕掛は減少していきます。Tp1=Tp2の場合は仕掛数の変化はありません。Tp1<Tp2では仕掛数は増えていきます。まとめると表2のようになります。
処理時間 | 仕掛発生 | 滞留仕掛数変化 |
Tp1>Tp2 | 0 | 減少 |
Tp1=Tp2 | 0 | 変化なし |
Tp1<Tp2 | 累積 | 増加 |
表2 Tp1、Tp2と仕掛の増減
次に、Tp1、Tp2が互いに独立に変動する場合を考えてみます。確率分布の種類は問いません。変動係数のみで定義します。そのときの平均仕掛数を次の近似式で求めてみます。

ρ=Tp2/Tp1
この式はTp1>Tp2の範囲でしか使えません。Tp1≦Tp2では、時間経過とともに仕掛数は限りなく増え続け無限大に発散してしまいます。
ρが0.50~0.95と0.950~0.999の範囲での平均仕掛数の変化の一例を図2と図3に例示します。ρが0.90~0.95辺りでは平均仕掛数は多くても十数個ですが、ρが0.99を超えると数十~数百となります。さらに、仕掛数のバラツキは平均の数倍の範囲に広がりますので、仕掛が突然増え、一旦増えたらなかなか減らないなど、不安定な管理状態が常態化することになります。
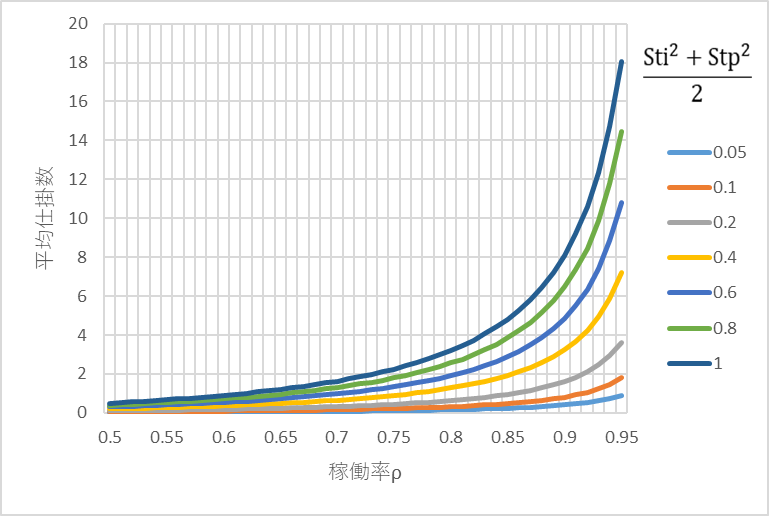
図2 稼働率0.5~0.95での平均仕掛数
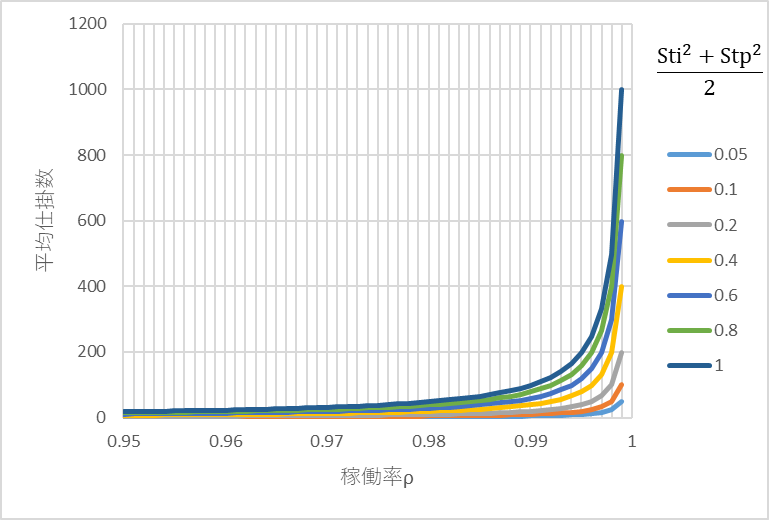
図3 稼働率0.950~0.999での平均仕掛数
待ち行列現象を抑制するためには
稼働率が高い状態で仕掛数を少なくするためには、Stp1とStp2を小さくすればいいことが判ります。

ρ=Tp2/Tp1
Stp1とStp2を小さくする方法が、平準化、標準時間、ムダ取り、、、など。つまり、TPSとは非線形特性である待ち行列現象を極小に抑える手法である、とも言えることになります。
4,トヨタが改善効果を金額評価しないのはなぜ?
TPSは線形モデルです。会計論も線形モデルです。どちらも線形モデルで相性がいいはず。でも、トヨタは現場で改善効果を金額評価しません。なぜなんでしょうね。非線形特性があるから、一般の企業が金額評価してはいけないのはわかりますが、トヨタは線形モデルならば、改善効果を金額評価してもよさそうなものですが、、。
GKCの提唱者は、トヨタが現場で金額評価を使わないことを承知しています。それでも、TPSに依拠すると言いながら、現場改善に金額評価を取り入れたのがGKC。つまり、GKCの提唱者はトヨタが現場で金額評価を使わない本当の理由を理解していないんだ、と思います。
トヨタも戦前、戦中はフォードやGMと似た生産方法でした。1950年の経営危機をきっかけにトヨタ生産方式の導入が始まり今日に至るわけですが、ここでは、トヨタ生産方式の特徴を生産ラインの非線形特性を極力抑制し、線形モデルで扱えるようにした、という視点で捉えております。
生産ラインの特性を線形モデルに換えることで、さまざまなメリットが出てきます。
生産計画を立てやすくなる
現場の状態を把握、共有しやすくなる
生産管理、現場管理が簡単になる
異常を発見しやすくなる
生産進捗がわかりやすくなる
仕掛を少なく、一定に維持することができる
・・・・
線形モデル状態を維持することも重要です。先に挙げた仕掛数の急激な増加という壁に挟まれた狭い範囲でしか線形モデルは成立しません。少しでも外れると、非線形領域に入り込みます。そうならないように、作業時間を測定し、あらゆるムダを省き、遅れそうになったら助け合い、異常が発生したらすぐ止める・・・まぁ、トヨタ生産方式ですよ、、。つまり、TPSは、一般の生産ラインが持つ非線形特性が顕在化する危機に晒されながら、そうならないように、線形モデルを維持している、と解釈することもできます。
そのような製造現場に金額評価を入れたらどうなりますか?
金額評価で物理現象を記述できますか? 金額評価で、現場で扱う時間、重量、体積、長さ等の絡み合いを記述できますか。流れるモノがどのような形状なのか、どれぐらい大きいのか、重いのか、どのぐらいの時間滞留しているのか、金額評価でわかりますか。金額評価で「なぜなぜ5回」が機能しますか。金額評価で非線形特性発生の危機を察知できますか。
トヨタが現場で金額評価を拒絶する理由は、TPSの根幹にかかわる重要な意味が隠されているのではないか、と考えるわけです。
TPSに依拠しながら会計論にこだわる愚に気づけ
にもかかわらず、GKCは現場で改善効果を金額評価しようとしているわけです。トヨタの線形モデルと会計の線形モデルとの違いが理解できていないのではないでしょうか。
重要なところなので、TPSの線形モデルと会計論の線形モデルの違いについて繰り返します。
トヨタ生産方式は Just In Time を実現する様々な工夫で非線形特性を極力、抑制した結果、線形モデルとして扱えるようになり、生産現場の物理現象を簡単に記述できるようになった。それに対して、会計はある期間の活動結果を金額換算して集計するもので、その集計は四則演算を主にした線形モデルだ、ということです。
金額(経済価値)とはサービス、商品等の交換を広く、円滑に行うために人間がつくった約束事。その価値判断は人により国により異なり、常に変動します。物理現象とはまったく異なる性質をもっていることに留意する必要があります。
一旦、金額評価してしまったら、そこで物理的因果関係は消滅し、全体の改善効果への繋がりは遮断されてしまいます。一部の現場改善効果を金額評価して、それを工場全体の改善額と結び付けることは、原理的に不可能です。「絶対に、やってはいけないこと」です。
5,現場改善会計論(GKC)を反面教師として
GKCの提唱者は以下の3点について、理解できていなかったと考えられます。
① 生産ラインの部分改善は、多くの場合、生産能力増強にはならない。
② 一般の生産ラインは非線形モデルである。
③ 生産ラインの物理特性を金額評価に変換後は、物理的因果関係が遮断され、現場の管理機能は失われる。
GKCは従来の会計の慣行を打ち破り、生産ラインの中の現場改善効果を直接会計処理の中に取り込もうとした意欲的なチャレンジであったと思われます。TPSの教訓に振り向くこともなく、師から受け継いだ従来の会計ルールに盲従し、さらに、これも別の師が掲げる設計情報転写論で今風の体裁を装う。確かに、見栄えはします。
その甲斐もあってか、「現場改善効果の類型化―会計的視点からの考察―」柊紫乃(愛知工業大学)・上總康行(京都大学名誉教授)は日本管理会計学会 2022年度年次全国大会で学会賞(論文賞)受賞しています。そして、2023/12/25には「現場改善会計論: 改善効果の見える化」(中央経済社)を上梓しています。
日本管理会計学会は何を評価したのかわかりませんが、「現場改善会計論」が生産現場で役に立つことは何もありません。それどころか、今起きているDX(デジタル・トランスフォーメーション)の障害になることを深刻に考えなければならないと思います。
ただ、最後の公益のチャンスがあるとしたら、
現場改善会計論(GKC)を反面教師として、
次の“当り前”を学ぶことができるかもしれません。
部分最適の和は全体最適にあらず。
現場改善を金額評価した後、それに関する物理的因果関係は消滅する。
東大、京大という日本を代表する大学教授陣の専門知識が後継教授陣に伝承される過程を背景に行われたGKC。そのなかでみられる、信じがたいほどの「思考能力の退化」や「知の劣化」は、ここ30年の日本のものづくりの停滞を裏付ける具体的事例ともなりえます。その価値が世に認められれば、これも公益の一つ。これこそ“怪我の功名”ではないでしょうか。