1,現場改善会計論を斬る・・・脱線して、わき道に迷い込んで、、
設計情報転写論に依拠したことにより現場改善会計論はどのような影響を受けたのか、が気になって読み進めているうちに、ちょっと脱線して、個別原価計算と思われる邸別原価表の不備に目が行ってしまいました(前回)。この論文は、行間が広すぎるというか、論理展開そのもののブレが大きいというか、あっちに行ったりこっちに来たり、読んでいるうちに脇道に迷い込んでしまった、という次第です。
なぜ、この論文、これほどまでにわけのわからない論理展開なのか、いや、むしろ、そうでありながらひとつの論文としてまとめ上げ、世に発表したという大胆さはどこから来るのか。
確たる自信があったのでしょうか。あるいは依拠した理論の後光を利用したかったのでしょうか。依然として設計情報転写論の瑕疵を現場改善会計論ではどのように扱ったのか、気にはなっておりますが、それ以前の問題があるようです。現場改善会計論の背後を覗いてみたくなりました。
裏に回るのには脇道の方が近道のようです。引き返さず、このまま進んでみましょう。
2,現場改善会計論の出所を確認
脇道にそれたら、現在位置があやしくなってきたので、もう一度、出発点を確認しておきます。現場改善会計論(GKC)の要旨にこんな説明があります。
京都大学の上總康行名誉教授とともに筆者が提唱する現場改善会計論(GKC) は,トヨタ生産システムと「設計情報転写論」に依拠する。
GKCは、上總康行名誉教授の管理会計論、トヨタ生産システム(TPS)、藤本隆宏教授の設計情報転写論の三つがベースにあることを再確認して、背景探査を開始します。
上總康行名誉教授の論文についてはほとんど調べていませんでしたので、先ず、その辺りから。下記の論文 click here がみつかりました。
現場改善効果の見える化― 機会損失を組み込んだ現場改善会計論 ―
上總康行 2018年3月
GKCの狙いや考え方がわかりやすくまとまっているようですので、この論文(以下、原文)を手掛かりにGKCのルーツを探ってみたいと思います。先ず、要旨(原文、p15)を引用します。
要旨
本論文では,日本の製造企業で広く行なわれている現場改善から生じる経済的効果を測定するため、機会損失概念を全部原価計算に組み込んだ現場改善会計論の必要性を論じる。
現場改善から生じる改善効果はさまざまである。これらの改善効果は,製品原価に反映され、さらに損益計算書の純利益に反映される。しかしながら、現場改善はごく小さな改善を積み重ねて行われるので、この小さな改善から生じる経済的効果を原価低減として測定することは非常に困難である。このため、製造企業では、会計数値ではなく、非貨幣的尺度,例えばリードタイム、品質、安全性、効率や能率などが重用されてきた。これらの尺度は有用ではあるが、会計情報ではない。
現在,多くの企業で全部原価計算が使われているが、問題点も残されている。それは、改善効果を原価低減として測定することが困難なだけではなく、現場改善から生じる余剰生産能力に関する会計情報を提供しないことである。とくに低成長期ないし停滞期には、需要不足のため、現場改善から生じた生産能力の増加部分を直に吸収できない。このため、増加した生産能力は余剰生産能力となり、そのまま放置すれば利益を獲得する機会を失うという意味で機会損失の発生となる。この機会損失を回避すること、それは企業経営者の戦略的課題の1 つである。従来の原価計算ではこの機会損失を測定することが不可能である。現場改善から生じた機会損失を測定できる原価計算方法を開発することは、喫緊の課題である。
要点をまとめますと、こんな感じでしょうか。
現場改善➡生産能力の増加➡(需要不足)➡余剰生産能力➡機会損失(企業経営の戦略的課題)➡従来の原価計算では機会損失の測定が不可能・・・
喫緊の課題は?
現場改善から生じた機会損失を測定できる原価計算方法の開発
が主な目的。原文のp30に次のような説明があります。
柊紫乃氏と筆者は,現場改善が主として工程ごとに実施されることに注目して,工程別実際原価計算の下で現場改善効果を会計的に測定できる現場改善会計論を提唱した。(柊・上總(2016))
ここで注目しておきたいのは、下記の説明です。
「工程別実際原価計算の下で現場改善効果を会計的に測定」
つまり、工程ごとの改善効果を金額評価する、と解されます。一方、上總康行名誉教授は、要旨で次のようなことも述べております。
現場改善はごく小さな改善を積み重ねて行われるので,この小さな改善から生じる経済的効果を原価低減として測定することは非常に困難である。
また、こんな記述もあります。
(原文、p19)
「経理部門主導の会計の関与を峻拒しながらジャスト・イン・タイム生産方式を育ててきたトヨタ自動車では,今や財務会計と生産システムの巧妙な棲み分けを実現した」(河田(1996)p.239)(原文、p27)
「本当の『トヨタ生産方式』は原価低減を追わない」(田中(2006)p.85)
つまり、「現場改善効果を金額評価する」ことは非常に困難であり、トヨタでも行われていない、ことを上總康行名誉教授は認識されていた、ということになります。
3,改善事例の説明は、、
ご本人も極めて難しいと認識しながらチャレンジしたテーマなので、どのようなアプローチで課題に立ち向かったのか、興味が湧くところです。
ところが、繰り返し読んでもピンときません、、。
原文p22に「3.サイクルタイム短縮とその会計的効果」に以下のような説明があります。
(要約)
ある製品加工にかかる直接作業時間(工数)が10時間で、2時間の残業が行われていた。定時賃率は1,000円、残業賃率は1,250円。第1次改善が行われ、10時間から8時間に短縮されたとすれば残業をする必要がなくなり、改善効果は2,500円。
次に第2次改善が行われ、8時間がさらに6時間に短縮されたとすれば、直接労務費は2,000円の原価低減となるはずである。しかし、多くの日本企業では、正規従業員として雇用された直接工には固定給が支払われる。このため、改善によって作業時間が減少しても、実際の賃金支払額はカットされない。その結果、改善効果2,000円は原価低減額として測定されない。その改善効果2,000円相当分を機会損失として認識することにしたい。
つまり、「工程別実際原価計算の下で現場改善効果を会計的に測定」した結果が2,000円だ、これが機会損失だ、と。そして、改善効果額と機会損失額の関係を次の式で説明しています。
改善効果額=原価低減額+機会損失額
2,000円が改善効果額だとすれば、
原価低減額+機会損失額=2,000円
となるのでしょうか。需要が増えて機会損失をすべて回収すれば原価低減額が2,000円となる、と解せます。これは、1個原価が2,000円下がる、ということでしょうか。利益が1個当たり2,000円増えるということでしょうか。あるいは、1日当りの利益が2,000円増えるということでしょうか、、、。
4,生産能力は上がるのか
原文の説明では、「8時間から6時間への短縮で生産能力は増加するが、需要がない環境では余剰生産能力となり原価低減とはならないので機会損失として認識する」、とのこと。
ある工程の作業時間短縮は生産能力を増加させる
これは、正しいのでしょうか? その前に確認しておく必要があることは、「8時間から6時間への短縮」とは、その工場で行われている投入から完成まで(全工程)の時間なのか、あるいはその中のひとつの工程の時間なのか。原文には「図5サイクルタイムの短縮」の説明がありますので、ひとつの工程を対象にしている、と解釈できます。
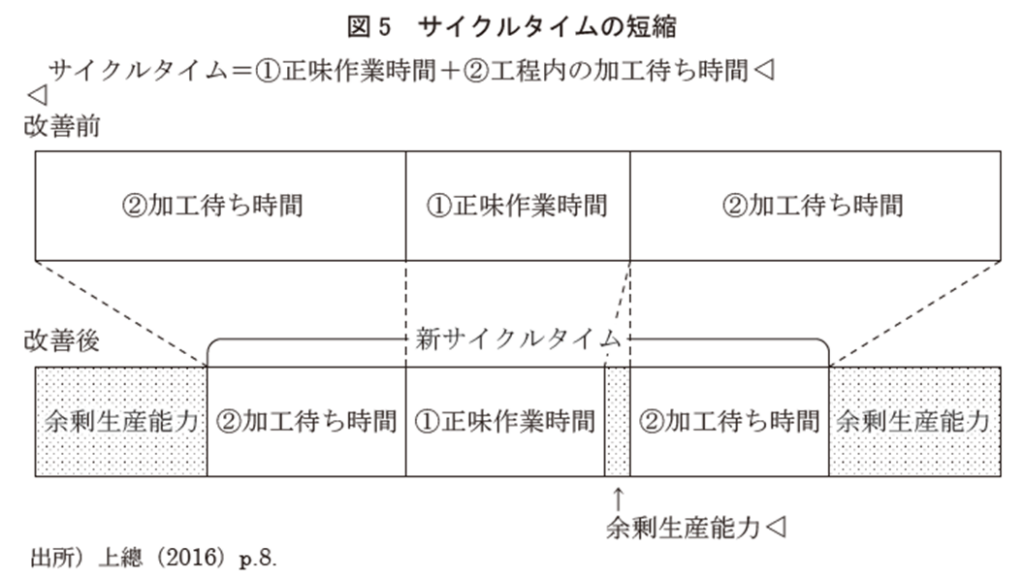
こんなフレーズ、お聞きになったことありませんか?
生産ラインの能力は、一番能力が低いボトルネック工程の能力で決まる。
原文には、ボトルネック工程での時間短縮だ、という説明はまったくありません。ボトルネック工程ではなかったら、生産能力は増加しますか? 増加しませんよね。リードタイムは短くなるかもしれません。それも運搬や流し方によりますが、、。
8時間から6時間に短縮した時間は、待ち時間が2時間増えた、という場合がほとんどではないかと思います。余剰能力とか、機会損失とか、、ちょっと違うんじゃないでしょうか。
たまたま、改善した工程がボトルネック工程だとしたら、生産能力は増えるかな。 でも、無条件ではありません。他のすべての工程が2時間以上の余裕があれば、そうですが。ある工程の余裕時間が、例えば30分しかなかったら、そこが新たなボトルネック工程となり、30分の改善効果しかでないことになりませんか。
仮にラインバランス100%の生産ラインだとすれば、その能力を上げるためには、全工程の能力を上げなければならないって、いうことですよね。
もうひとつ、忘れてはいけないことは、中小企業が置かれている生産環境の大部分は、多品種・少量・変量で受注生産。このような環境では様々な変動要因がかさなり、待ち行列現象が必然的に発生します。ラインバランスをできるだけ高くしようとすればするほど、待ち行列現象は生産ライン全体に広がり、ボトルネックはあっちに行ったり、こっちに来たり、常に動き回ることになります。
そうしますと、余剰生産能力が生じたとしても、安定した状態ではありません。従って機会損失も不安定な状態となり、現れたり消えたり。現金2,000円がテーブル上に置かれたまま、という感じではありません。
改善効果額=原価低減額+機会損失額
この式も成立しないでしょうね。例えば、直列5工程のバランスラインだとします。各工程の作業時間は1時間(60分)/個、8時間/日 稼働で8個/日 できます。5工程ありますので、1個作るのに5時間かかります。ある、ひとつの工程で45分/個 でできるように改善が行われたとします。8個つくるのに8個×45分=360分(6時間)ですみ、2時間の手空き時間ができます。2時間の手空きでどれだけの余剰生産能力ができるでしょうか。1個作るのに5時間かかるわけですから、2時間では1個もできません。計算される改善効果額は2,000円、需要があったとしても、原価低減額はゼロ、機会損失額もゼロ、、。この式、成り立ちませんね。会計的には成り立つのかもしれませんが、、。
2,000円分の機会損失は需要があれば埋め合わせができると思われるかもしれませんが、それは、会計基準は線形モデルであることが影響しているかもしれません。生産ラインの特性は、非線形であり、確率分布しますので、単純な加減乗除では計算はできません。基本的に両者の数理モデルは、まったく異なることに留意する必要があるのではないでしょうか。
5,現場改善会計論を裏から観れば、、わかったことは、
現場改善会計論を裏から観たら、違った景色がみえてきました。現場改善会計論に入る前提条件が成立していないようです。あっちに行ったりこっちに来たり、右往左往しているようです。入口を間違えたのでしょうか。
ポイントを3つ、挙げておきます。
その1;1工程の現場改善で生産能力が増加する条件は限られている
余剰生産能力が安定する条件を明示する必要がある。
その2;改善効果額=原価低減額+機会損失額
この式は成立しない。
その3;生産ラインの特性は非線形的で確率分布することが考慮されていない
①ボトルネックで生産ラインの能力が決まる
②待ち行列現象・・稼働率vs待ち時間
トヨタがなぜ、現場に金額評価を持ち込まないのか。そのトヨタが安定して高い業績を維持していることを上總康行名誉教授もご承知のはず。現場改善を金額評価する愚に気が付かないのでしょうか。現場で金額評価が行きかえば、物理的因果関係を追う「なぜなぜ5回」の機能が著しく低下することは目に見えています。常日頃の改善を重視するトヨタは金額評価の弊害を認識しているのではないかと思われます。
・・・・・
現場改善会計論のベースとなる考え方を提唱した上總康行名誉教授の
現場改善効果の見える化― 機会損失を組み込んだ現場改善会計論 ―
を拝読させていただきました。その結果、わかったことは、
現場改善効果と機会損失との会計的結合を目指す現場改善会計論は、その前提条件に致命的誤謬を内在している可能性が高い
ということでしょうか。