1、ものづくり改善ネットワーク
「失われた10年」という言葉を頻繁に聞くようになっていた2004年4月、文部科学省が推進する「21世紀 COE(Center of Excellence)プログラム」の一環として、東京大学大学院経済学研究科に「ものづくり経営研究センター(MMRC)」が設立されました。初代センター長が藤本隆宏教授。その後「経営教育研究センター(MERC)」が設置され、その傘下で「ものづくりインストラクター養成スクール」が運営されています。
さらに藤本教授は2013年に一般社団法人ものづくり改善ネットワーク(MKN)を設立し、地域ものづくり改善インストラクター養成スクール等の運営や「地域ものづくりスクール開校」の支援等も行っています。
どんなこと教えてるのかと、ものづくりインストラクター養成スクールのカリキュラム2021年度パンフレットをダウンロード(Adobe PDF)をクリックしたら “Not Found”。メールで聞いてみたら、「今年(2023年)で終了、ものづくり改善ネットワークに引き継ぎます」、とのこと。
「ものづくり改善ネットワーク」の方に カリキュラム がありましたので覗いてみました。藤本教授担当は次のようになっています。
講座名 | 内容 |
ものづくりとは? | よい設計のよい流れ |
流れを見切る | プロセス分析 |
流れの良し悪しを知る | 納期とリードタイム |
流れを管理する | 日程管理と資材所要量管理 |
在庫を減らす | かんばん方式と順序供給 |
「流れ」の文字が目につきます。具体的にどんなことを教えているんでしょうか。ホームページに YouTube 藤本隆宏の“ものづくり考” に動画があります。そのなかの「在庫とは」をちょっとみてみました。
2、「在庫とは」;動画の概要
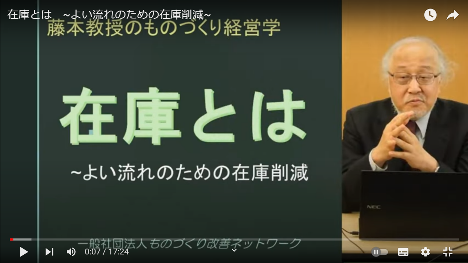
納期の裏にはリードタイム有、リードタイムの裏に在庫有。淀む在庫を減らしてよい流れをつくる。
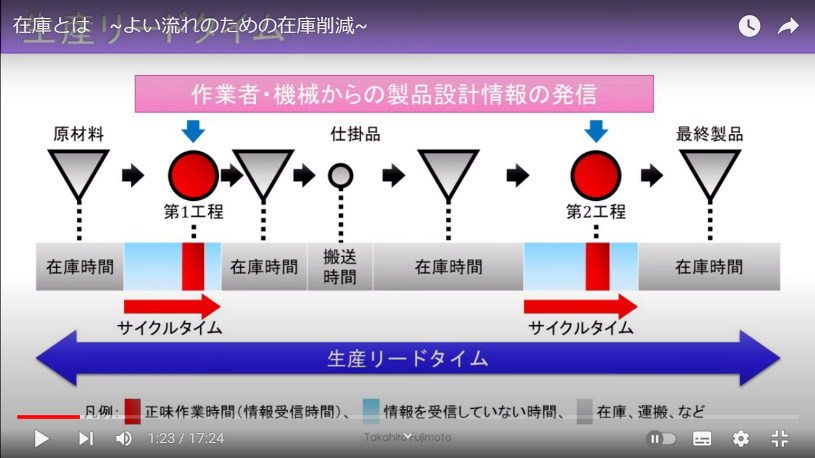
トヨタの生産リードタイムに対する正味作業時間(情報受信時間)は1/200(0.5%)、普通の会社のそれは1/2000(0.05%)。0.05%を0.5%にするだけで1/10になる。実例はいっぱいある。
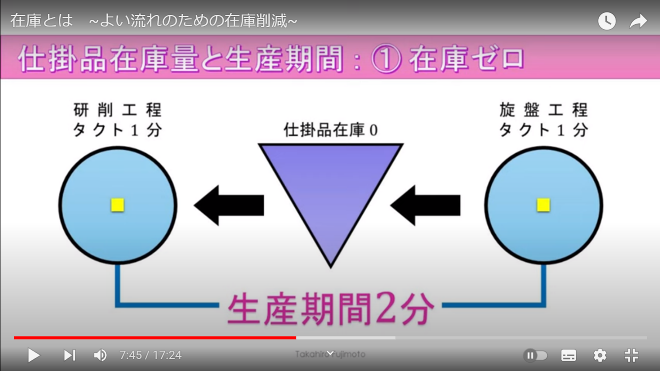
在庫ゼロであれば生産リードタイムは2分
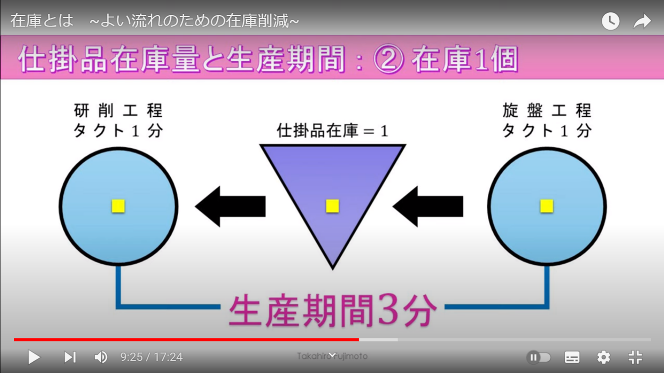
在庫1個なら生産リードタイムは3分
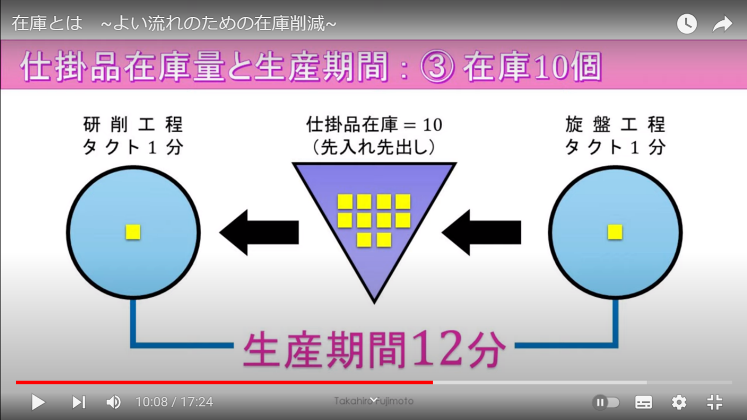
在庫が10個であれば、生産リードタイムは12分
在庫が100個なら生産リードタイムは102分、1000個なら1002分・・・。生産リードタイムはほぼ在庫数に比例する。
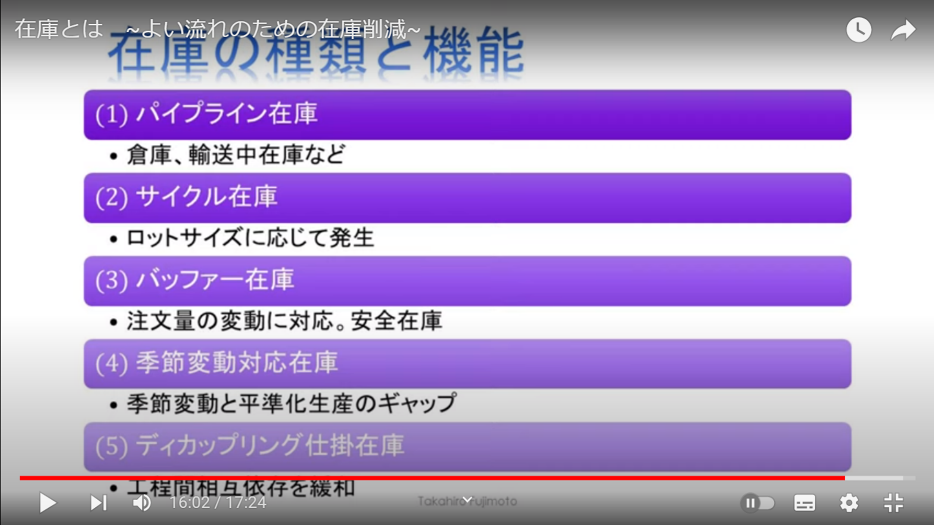
在庫には機能のある在庫と機能のない在庫がある。
流れを良くするためには機能のない在庫をゼロにする。
3、大量にある「機能のない在庫」
挙げた(1)~(5)の在庫は全部機能があるので、「機能のない在庫をゼロにする」とは、機能を損なわない程度に在庫を減らすっていうことでしょうね。そうやって減らしたら、普通の会社の生産リードタイムに対する正味作業時間は、トヨタ並みの1/200に、つまり1/10になるんでしょうか。1/2~1/3ぐらいならできる企業はあるかもしれませんが、大部分の会社が1/10にできるかといったら、“うそ”になりますよ。
5種類の在庫に含まれる「機能のない在庫」を減らす努力は、努力の程度は違うかもしれませんが、どこの会社でもやってますよ。普通の会社の正味作業時間/生産リードタイムが1/2,000っていう話、30年~40年前からあって、なにも変わっていません。なぜか?
種明かしをすれば、5種類の他に、ほとんど機能のない、しかも不規則に急激に増え、しかしなかなか減らない、手に負えない在庫がある、ということです。
このブログをご覧いただいている方々は、何度も取り上げておりますのでお察しがつくと思いますが、ここで簡単に「機能のない在庫」について説明しておきます。
図1をご覧ください。原材料は常にあり、第1工程に供給されます。第1工程で処理後、第2工程で処理され完成します。第1工程と第2工程間の移動時間は無視します。第1工程の平均処理時間をTp1、変動係数をStp1、第2工程のそれぞれをTp2、Stp2とします。第1と第2工程間にある仕掛在庫がどのようになるかを考えてみます。
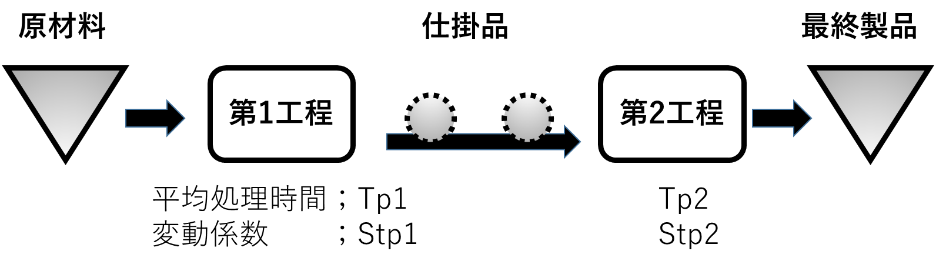
図1 2つの工程間で発生する仕掛
はじめに、Tp1もTp2もバラツキのない固定値の場合を考えてみます。但し、立ち上がりは除きます。Tp1とTp2の組み合わせは表1に示すように3種類あります。Tp1>Tp2のとき、例えばTp1が1.2分、Tp2が1分だとすると、第1工程から第2工程に供給されるワークの時間間隔は1.2分、第2工程の処理時間は1分なのでその前で待つ仕掛はありません。Tp1=Tp2の場合は、第1工程の処理が終了すると同時に第2工程の処理が開始されますので、この場合も仕掛はありません。Tp1<Tp2の場合は第1工程の処理が終わっても第2工程は処理中なので、その前で待たなければなりません。
すでに、いくつかの滞留仕掛がある場合を考えてみます。Tp1>Tp2のときは時間の経過とともに仕掛は減少していきます。Tp1=Tp2の場合は仕掛数の変化はありません。Tp1<Tp2では仕掛数は増えていきます。まとめると表1のようになります。
処理時間 | 仕掛発生 | 滞留仕掛数変化 |
Tp1>Tp2 | 0 | 減少 |
Tp1=Tp2 | 0 | 変化なし |
Tp1<Tp2 | 累積 | 増加 |
表1 Tp1、Tp2と仕掛の増減
次に、Tp1、Tp2が互いに独立に変動する場合を考えてみます。確率分布の種類は問いません。変動係数のみで定義します。そのときの平均仕掛数を次の近似式で求めてみます。

ρ=Tp2/Tp1
この式はTp1>Tp2の範囲でしか使えません。Tp1≦Tp2では、時間経過とともに仕掛数は限りなく増え続け無限大に発散してしまいます。
ρが0.50~0.95と0.950~0.999の範囲での平均仕掛数の変化の一例を図2と図3に例示します。ρが0.90~0.95辺りでは平均仕掛数は多くても十数個ですが、ρが0.99を超えると数十~数百となります。さらに、仕掛数のバラツキは平均の数倍の範囲に広がりますので、仕掛が突然増え、一旦増えたらなかなか減らないなど、不安定な管理状態が常態化することになります。
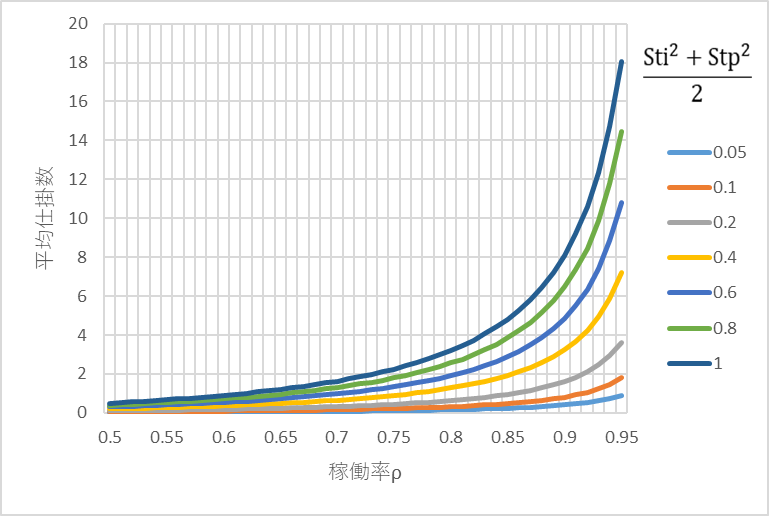
図2 稼働率0.5~0.95での平均仕掛数
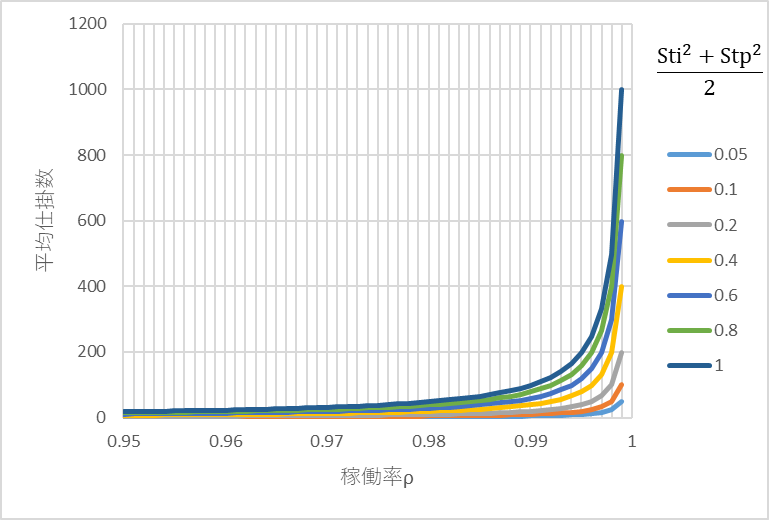
図3 稼働率0.950~0.999での平均仕掛数
4、工場2,000拠点を視察しても、気が付かない
工場ではできるだけ稼働率を高くしようとします。稼働率が高くなればなるほど、仕掛が急激に増加し、生産リードタイムが長くなり、納期遵守率が低下します。2工程間で発生する仕掛数試算例をみてもわかるように、平均で数十個~数百個、そして、その数倍の範囲でばらつきます。図2、図3でもわかるように、断崖絶壁を登るがごとく、極めて不安定な領域で生産活動が行われることになります。
このような在庫に有用な機能はほとんどありません。「流れ」をよくするために真っ先に排除しなければならない在庫であることは衆知の話ではないでしょうか。
藤本教授の講義の中には、このような待ち行列現象による滞留仕掛在庫の発生についての説明はまったくありません。
技術・生産管理、そしてトヨタ生産方式をはじめとした生産管理方式の研究を専門とし、現場に1,000回以上通った、工場2,000拠点を視察したと豪語する藤本教授が、現場にあふれ返る仕掛在庫が何たるか、に気が付かないことってあるのでしょうか?
「事実は小説より奇なり」
軽妙な口調で解説する動画をみながら、日本のものづくり理論を指導する大学教授のレベルの低さに唖然としております。
ちなみに、待ち行列現象による仕掛在庫って、トヨタ生産方式では極少に抑えられている、言い方を換えますと、トヨタ生産方式の最も顕著な特徴は、この種の仕掛在庫が実質ほぼゼロに近いぐらいに抑制されている、と解釈できます。Just In Time って、そういうことじゃないでしょうか。
「ものづくり改善ネットワーク」の講義内容に、致命的な間違いがあるようです。
ご注意ください!!