技術・生産管理、進化経済学を専門として、トヨタ生産方式をはじめとした製造業の生産管理方式の研究で知られる藤本隆宏教授は、生産管理の最重要課題は「流れを良くすること」だと強調します。私もまったく同感です。
ところが、藤本教授の著書を読んでみると「流れ」という語句は頻繁に出てくるのですが、流れをよくする具体的な方法は陳腐なものばかり。トヨタ生産方式に関する記述も、ありきたりのトヨタ語が多く、それも表面的な説明ばかり。
例えば、教科書的にまとめられた「生産マネジメント入門Ⅰ」の中の説明。
「流れの良さ」を「正味付加価値時間/生産リードタイム」で表せば、トヨタが200~300分の1に対して、普通のメーカーでは2000~3000分の1だ。「流れ」をよくするためには生産リードタイムの短縮がカギで、在庫システムの改善等による在庫削減が必要だ、と。
で、“おやっ”、とおもった。在庫システム改善の説明で、待ち行列問題を取り上げているじゃないですか。待ち行列問題が在庫問題の解決に役立つだろうという考えがあったのでしょう。ほのかな期待を抱いて読み進めてみましたが、EOQや安全在庫問題と待ち行列問題と合わないところがあるとか、ないとか言いながら途中でうにゃむにゃに、、。待ち行列問題は棚上げっていう感じ、です。
EOQと安全在庫とかではなくて、工程と工程の間にある仕掛の挙動に視点を置けばよかったのにぃ、、というのが前回のブログでの話です。工程間の仕掛の移動っていろいろです。機械的に直結されていて自動的に流れる場合もあれば、処理を終了したらわきに置くだけで、次工程が必要に応じて取りにくるというのもあります。注文が増えたり、工程にトラブルがあったりすると仕掛は急増します。生産ライン全体をみますと、そういう仕掛滞留が多いのではないでしょうか。
EOQや安全在庫と工程間のワークとはお隣同士。わずかな視点のズレではありましたが、結果は大きくズレました。待ち行列理論の基本がわからず使い方を間違えたのか、それとも生産ラインの基本特性を理解してないために的を外してしまったのか、その両方だったのか、定かではありませんが、、。
生産ラインの「稼働率vs生産リードタイムの特性」は、技術・生産管理そして、トヨタ生産方式をはじめとした生産管理方式の研究を専門とする大学教授にとっては、一丁目一番地の、基本中の基本的なコアノレッジです。それが、どうやら、すっぽりと抜け落ちている。このコアノレッジを欠いて展開する分析、解析は、当然のことながら的はずれでピンボケ、いや、それだけならまだいい。関連方面に多大な悪影響を及ぼすのではないか、と懸念を抱くわけです。
「生産リードタイム/正味付加価値時間」が、トヨタは200~300倍に対して、普通のメーカーでは2000~3000倍、つまりトヨタの10倍だという話と待ち行列現象の関わりを簡単にみておきましょう。
一般的な生産ラインは複数の工程がありますが、ここではひとつの工程に注目して、そこをワーク(被処理物)が流れる様子を見てみます。図1に工程がひとつの生産ラインの一例を示します。ワークは到着順に加工されます。工程が手空き状態のときワークが到着すれば直ちに加工が始まります。工程がビジーのときは到着したワークは加工が終わるまで工程前で待ちます。加工の順序はFIFO(ファーストイン・ファーストアウト)とします。
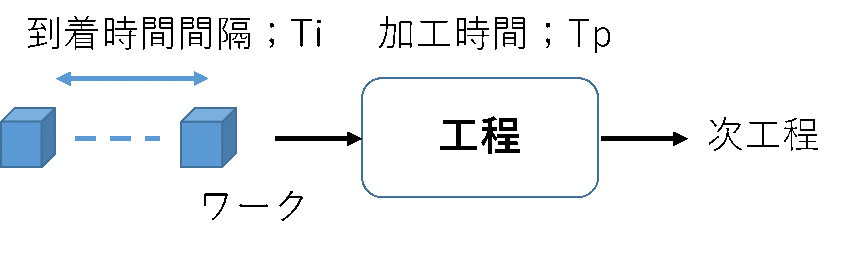
図1 ひとつの工程でのワークの流れ
① Ti≧Tp のときは工程前で待つワーク(仕掛)はありません。
② Ti<Tp のときは時間の経過とともに仕掛の数が増えてきます。TiとTpの差が大きければ大きいほど増加のスピードが速くなります。
③ ②の状態で、Ti=Tp になると仕掛の増加が止まります。
④ ②または③の状態で Ti>Tp になると仕掛が減り始めます。TiとTpの差が大きければ大きいほど減少のスピードが速くなります。
では、TiもTpも互いに独立に変動する(バラツク)とどうなるでしょうか。それぞれの変動係数(標準偏差÷平均値)をSti、Stpとします。Ti、Tpは平均を表すとします。その時の仕掛の平均待ち時間;WTの近似値は次の式で求められます。

Ti/Tpは工程の稼働率に相当しますので、ρ=Ti/Tpとして次のように表すこともできます。
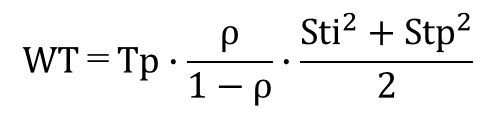
待ち時間/正味付加価値時間はWT/Tpとなりますので、
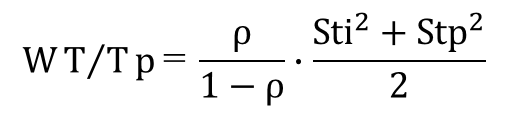
となります。
ρ/(1-ρ) は稼働率依存、(Sti2+Stp2)/2 は変動係数依存で一般的には0~1の値をとります。(Sti2
+Stp2)/2 が0.05~1のときのWT/Tpの一例を図2に示します。
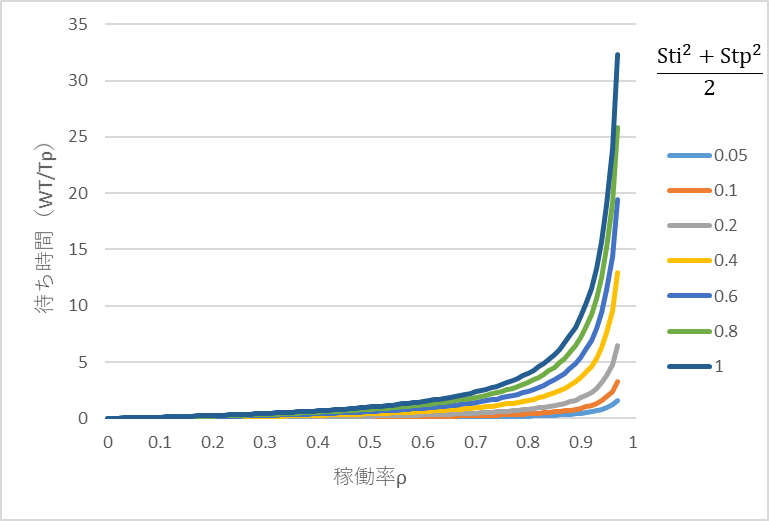
図2 稼働率対待ち時間の一例
稼働率対待ち時間のグラフに普通のメーカーとトヨタの位置を示した一例が図3です。(稼働率の範囲を0.7~1に変えています)
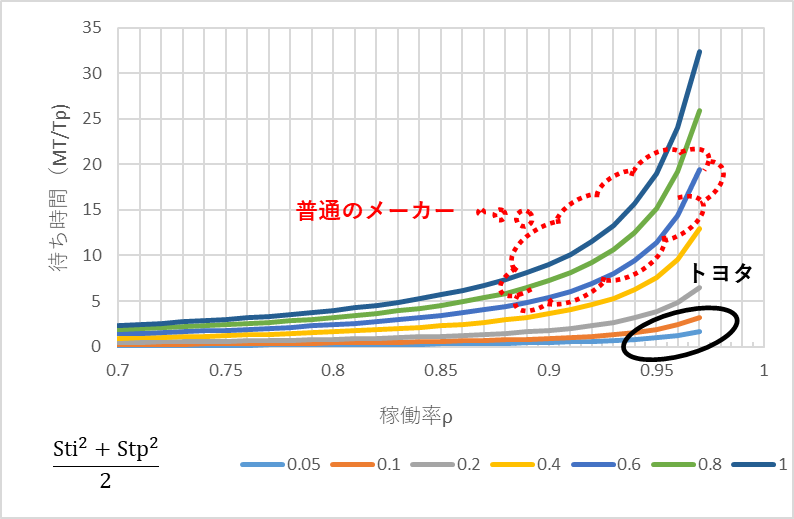
図3 トヨタと普通のメーカーの待ち時間
普通のメーカーの正味付加価値時間に対する生産リードタイムがトヨタの10倍だ、という話とほぼ合います。トヨタがなぜ待ち時間が短いのか、待ち時間の近似式をみれば一目瞭然です。(Sti2+Stp2)/2 が小さい、つまり、StiおよびStpが小さいからです。
Just In Time とは、簡単にいえば、待ち時間の最短化ではないでしょうか。「生産の流れ」の待ち時間を最短にするための仕組みがトヨタ生産方式である、とも言えるのではないでしょうか。そのメカニズムを説明するのに「待ち行列理論」は便利です。
技術・生産管理、進化経済学を専門として、トヨタ生産方式をはじめとした製造業の生産管理方式の研究で知られる藤本隆宏教授の「トヨタ論」は、実に、薄っぺらです。生産ラインの中をワークがどのようなメカニズムで「流れ」ていくのか、その原理を正しく理解していないのではないか。
「生産システムの進化論」ではトヨタを分析の対象としていますが、その結論は、
トヨタとは、情報システムの構造的複雑さにより他社の模倣を妨げ、
組織成員が共有する健全な「心構え」に支えられた
事後合理的能力構築能力を創発し続けるシステムである。
「設計情報転写論」でトヨタの「設計・生産の流れ」を分析した結論が、情報システムの構造が複雑だとか、心構えだとか、事後合理的だとか、、ですかぁ、、。
・・・余談・・・
日本で最も信頼できない職業は? 世界最大規模の世論調査会社が日本人500人に聞いた
「人を肩書で判断するな」というが、初めて人に会うときなどは、やはり職業で相手を判断してしまうもの。では、どんな肩書なら、信頼を得やすいのか?
ユーロネクスト・パリ(パリの証券取引所)に上場する世界最大規模の世論調査会社「イプソス」が、2023年5月26日~6月9日に世界31カ国、2万2816人(うち日本人500人)に調査したところ、日本では医師、科学者、裁判官がトップ3を占めた。世界でも医師、科学者は1位、2位に入るが、3位は教師。翻って日本では、教師は8位と信頼度が低い。
やっぱり、、、