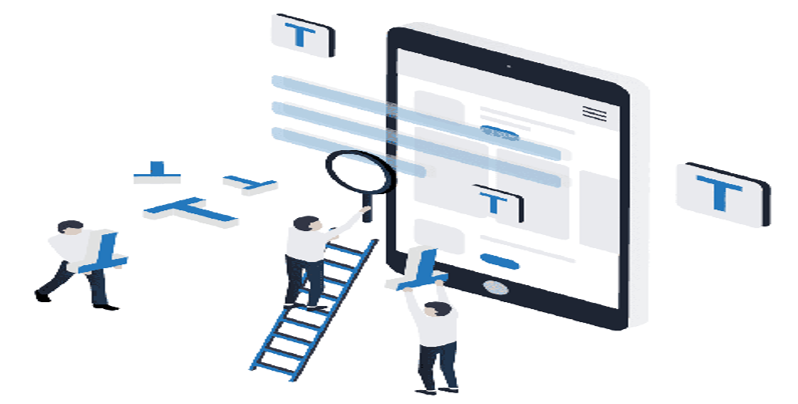
生産スケジューラ・ベンダーの(株)スカイディスクのWebsiteに “生産スケジューラ導入が90%失敗する理由” と題するブログがあり、そこに、製造業従事者352名に同社が実施した次のようなアンケート結果が出ています。
- 導入済・運用もうまくいっている 1.4%
- 導入・運用に課題がある 17.3%
- 未導入(過去に検討したことがあるが諦めた) 18.5%
- 導入検討中 27.6%
- 未導入・未検討 35.2%
導入検討中と未導入・未検討を除くと、次のようになります。
- 導入済・運用もうまくいっている 3.8%
- 導入・運用に課題がある 46.5%
- 未導入(過去に検討したことがあるが諦めた) 49.7%
半数は、導入検討はしたが導入せず、47%は導入はしたが問題を抱えながらの運用。問題なく使っているのはたったの4%。このアンケート結果は、私の経験とほぼ重なりますので参考にさせていただこうと思います。
でも、(株)スカイディスクって、生産スケジューラのベンダーですよ。「生産スケジューラの導入が90%失敗」なんて言っていいのかな、、と思いながら、読んでみると、「従来の生産スケジューラは云々・・・だから90%失敗するが、我が社のスケジューラはクラウド型なのでカンタン、短期で導入できる・・・」。なるほど、ネガティブな情報を逆手に取った宣伝、巧みですね。
ただ、宣伝は巧みなんですが、“うまく運用できているのはたったの4%”しかないのはなぜか、“問題を抱えながらの運用となっている”のはなぜか、“導入を検討するも半数は諦めてしまう”のはなぜか、という疑問に対する説明は、的外れでトンチンカン。
これらの問に応えるためには、(株)スカイディスクの宣伝ではなくて、同じ生産スケジューラ・ベンダー、FlexscheのWebsiteにある“解説記事”の方が面白そうなので、そちらを取り上げてみたいと思います。
解説記事の中の 第2回:生産リードタイムを短縮せよ の末尾の方に、次のような記述があります。
ではどうすれば生産リードタイムを短縮できるのでしょうか。
生産リードタイムには、正味の作業時間と待ち時間とが含まれます。このうち、通常は、待ち時間の方が圧倒的に長く、また、短縮もしやすいものです。待ち時間は様々な原因によって発生します。それらを明らかにして、影響や効果の大きいものから改善していくべきです。
なお、どこでどのような待ちが発生しているかも、生産スケジューラであぶり出すことができます。 さらに、どのような改善を行えばどのような効果が得られるかも、生産スケジューラを活用すれば定量的にシミュレーションすることができます。
ポイントをまとめますと、
(A) “生産リードタイムは作業時間と待ち時間。このうち、待ち時間の方が圧倒的に長い。”
この認識は昔(30年以上前)からあって、私も同感です。
(B) ①“待ち時間の発生原因を明らかにする➡②影響や効果の大きいものから改善”
この考え方も改善手法としては広く利用されている、ごく普通のやり方です。
(C) “①待ち発生の場所、状況も、生産スケジューラであぶり出し、②待ち時間の発生原因を明らかにする”
と言っていますが、ここらあたりから怪しくなってきます。
(D) さらに、“改善と効果を生産スケジューラで定量的にシミュレーションできる”
とも言っていますが、ここまでくると、完璧に“うそ”。
Flexscheって、生産スケジューラの開発・販売会社ですよね。生産スケジューラで何ができるのか、正しく理解できているんでしょうか。“できない”ことを“できる”ってのたまう、、どうも“まともな会社”ではないようです。
だから、「生産スケジューラの導入が90%失敗」するんですよ、って言いたくなるわけです。
生産スケジューラで、“できること”と“できないこと”を考えてみたいと思います。
先ず、“(C)の①待ち発生の場所、状況も、生産スケジューラであぶり出せる”ですが、多分、これは、作成したスケジュールに対して、実行時の時刻を記録して、ワークごと、工程ごとの待ち時間がわかる、ということを言っているのだと思います。これは技術的には十分に可能なことですので、これは“できる”です。
(C)の②“待ち時間の発生原因を明らかにする”ですが、、。特定できる原因もありますが、大部分は何が原因だかよくわからない、、んです。ワークごとに、通過した工程での待ち時間のデータが全部そろっていても、待ち時間の発生原因が分かるのは、ごく一部。
待ち時間の短いものの原因はムリとしても、平均からグーンと離れた異常値的な待ち時間の原因ならわかるんじゃないの、と思われるかもしれませんが、異常値的に長い待ち時間の原因もよくわからないものが圧倒的に多いんです。なので、これは“できない”、です。
となると、ちょっと戻って、(B)の①“待ち時間の発生原因を明らかにする“もほとんど、“できない”ことになります。(B)の①ができなければ、(B)の②“影響や効果の大きいものから改善”も”できない“ことになります。(B)って、一般的に、常識的に認められ広く使われている手法ですが、待ち時間を対象にする場合は使えない。このことにお気付きいただきたいんですがねぇ~。
(D) “改善と効果を生産スケジューラで定量的にシミュレーションできる“ですが、シミュレーションって、実際の生産ラインの動き(流れ具合)を再現することですよね。生産スケジューラで使う時間は固定値。ですから、リソース(機械、作業員、)への仕事の割付けは詳細にできて、様々な組み合わせを試してみることはできます。完璧な最適解を求めることはできなくても(NP困難問題)、まあまあの解は見つけることはできると思います。
ところが、現実は、工程への到着間隔と工程の処理時間が変動する場合が圧倒的に多く、この場合、待ち時間が発生し、計画時刻と実際の作業時刻に乖離が生じます。時間の経過とともに乖離が大きくなり、計画通り実行することは難しくなります。多くの場合、実行不可能となってしまいます。
従って、(D)も“できない”、となります。
Flexscheの“解説記事”の第2回:生産リードタイムを短縮せよ の末尾の方にある説明、(A)~(D)の内、“うそ”でないのは(A)だけ。残りは全部“うそ”。
、で、生産スケジューラがうまく動かないのはなぜ?
“生産スケジューラ導入が90%失敗する理由”は、Flexscheの“解説記事”は正しいと信じているから~、、。
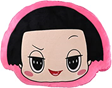
“ チコちゃん ”に聞いても、そう答えると思いますよ!
でも、、4%はうまくいくんでしょ。なぜ?
うまくいく条件はあるんですよ、確かに。それは、工程に到着する時間間隔と工程での処理時間が予め分かっていて、且つ、それらの時間は計画時も実行時も同じである場合、です。多少ズレても、実用的に問題がない範囲であれば使えますけど、、。まぁ、それが4%ぐらいある、、ということだと思います。