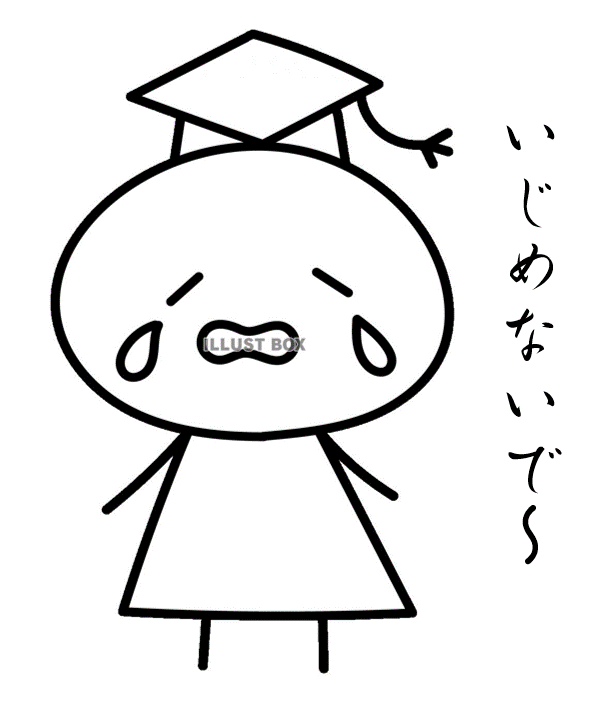
(赤茶色の部分が本間峰一氏のメールから引用した部分です。メール公開はご本人より了承いただいております。)
コンサルの最初の手順として最大値(異常滞留)の発生原因を分析してつぶしておく必要がある。業務改善コンサルなら当たり前のアプローチだ。
「当たり前のアプローチ」の背後には、製造現場は上からの生産指示に従わなければならない、という前提があることがわかりました。そのような基準だとすると、生産指示に従わないことが「異常滞留」の発生原因にされてしまいそうですが、、、
異常滞留の事例とその発生原因は、
親会社の内示で生産開始したら、途中で親会社が納期変更したのでそのオーダーは現場の班長の独自判断でストップさせて別の製品の加工を先に動かした。その結果そのオーダー加工品は工程途中で半年以上止まっていたが、誰も気づかなかった。
やっぱし、生産指示に従わず「現場の班長の独自判断でストップさせたこと」が異常滞留の発生原因だ、とされているようです。
異常滞留(最大待ち時間)の発生原因調査では、
最大待ち時間の発生要因を調べると工程待ちよりも人間の手続きミスや判断ミスが原因となっていることが多い。
「人間の手続きミスや判断ミス」って、生産指示に従っていても防げなかったのか、指示に従わなかったから起きたのか。前者であれば、生産指示そのものが適切ではなかったとかその仕組みに欠陥があったとか。後者であれば人間のミスつまり「属人的なもの」が原因だ、と。いずれにしても、異常滞留発生の原因は企業(製造現場)にあることになりそうです。
製造現場の状況は、
私のコンサル先をみていると私が指摘するまで行われていないところがほとんどです。そうでなければ200日なんて工程滞留が見過ごされているはずがありません。理由の一つに過度な製造時間短縮に目が行き過ぎていることがあるように思います。その背景には原価管理とTPSがあるのではないかとみています。
「私が指摘するまで行われていない」・・・「私の指摘が絶対に正しいのだ!」という上から目線的雰囲気が感じられます。「その背景には原価管理とTPSがある」・・・製造時間ではなく待ち時間だよ、という本間氏の主張の背景のひとつ、でしょうか。しかし、違和感がありますね。
待ち時間がダントツに短いのはTPS(トヨタ生産方式)ですよ。今、待ち時間を短くしようとしているときにTPSこそ良きお手本になるんじゃないでしょうか。「TPSに目が行き過ぎているから滞留が見過ごされている」、、TPSも悪者扱いですか。で、本間氏の改善コンサルの具体的な方法は、
原因の多くが属人的なものが多いので地道に皆でデータを見ながら話し合うのが筋だと思っています。コンサルがそのトリガーになれれば十分だと思います。
つまり、異常値の原因は製造現場で働く皆さんの問題だから、みんなで話し合って解決策をみつけなさい、ということのようです。これで、コンサルを依頼した企業側は満足するんでしょうか。
いくら何でも、これが改善コンサルのすべてか、と思うと、寒気さえ感じてしまいます。何かもっとまともな考えもあるはずだ、と思い、定量的な側面の質問に変えてみました。
「属人的なもので発生する異常値をなくすことで、80%を占める待ち時間を短くできる根拠は何ですか?」という質問に対する、定量的な説明部分(異常値の性質、特性等)を抜粋してみます。
異常値というのは工程間でそのワークだけが1か月以上滞留している話で、沖電線の資料でいえば最大値になります。通常の滞留は中心値ですので、異常値とは処理時間の何倍ではなく通常の滞留実績時間(中心値)の何十倍という数字です。原因は、200日になると現場が故意にストップさせたか、伝票処理のミスが中心です。滞留させたからといって納期遅れにはつながらないのでずっと放置されるというのが多いです。
異常値とは、滞留時間の中心値(中央値のことと解釈します)の何十倍も離れていることを異常値と捉えることから、定量的な分析をしようとする意思は感じられます。でも「納期遅れにはつながらない」んだったらいいんじゃないの?と言ったら元も子もなくなりますか。
最初に企業の管理レベルが十分でないというお話ししましたが、定量的な問題を議論するような状況ではない工場がほとんどです。
定量的な分析ができないのは「企業の管理レベルが低いから」。「そんな工場がほとんど」だから、定量的な分析をできない理由は企業側にある、と言いたいのでしょうか。
異常値が大きすぎて平均値が使えないので、中心値で比較するようになりました。それでも中心値が異常値に影響して長くなりがちです。属人的な異常値の原因を洗い出してつぶすだけでもかなりの時間がかかります。・・・的外れにならないように必ず改善による結果数字を確認するようにします。組織が細分化されている大企業ほどこの結果確認作業をしていないことが多く、信じられないような異常値が放置されています。ただ、このフェーズのコンサルができるデータが得られない工場の方が多いのが実状です。
異常値が大きすぎ、、平均値が使えない、、中心値が異常値に影響、、、データの分布状態が予想したものとは違っているようですね。その理由は、異常値の原因が物理的なものではなく「属人的なもの」だから、と言いたいのでしょうか? さらに「結果数字を確認しようとしても確認作業をせず、放置している」と、企業側に非があることを繰り返します。
最大待ち時間の発生原因を分析しているところが少ないことを問題にしています。
「待ち時間を短くするためには、最大待ち時間の発生原因に手を打たなければならない。なのに、その分析をしているところが少ない」。原因分析をしない企業に問題がある、と。
最大待ち時間が平均待ち時間もしくは中央待ち時間の3から5倍以上の数字・・・を異常値(異常滞留)と呼んでいます。・・・佐々木さんは異常値を処理時間の何倍と定義していましたが、そんな定義はしていませんので訂正してください。
先に言及しましたが、本間氏は「異常値大きすぎ、、平均値が使えない、、中心値が異常値に影響・・・」と言いながら、「使えない平均値を基準に使う」って、矛盾していませんか?
待ち時間の平均値は、平均処理時間に工程への到着間隔と処理時間の変動が影響しますので、そのバラツキは平均処理時間のそれより大きくなり、不安定になります。平均待ち時間を基準にすると、平均処理時間を基準にするより、定量的判断の精度が低くなってしまいます。(待ち時間発生の詳細については後述します)
最大値が排除出来て、待ち時間が平均値付近に集中してきたら次は工程負荷が待ち時間の発生要因になっていないかの検討をします。
「最大値が排除出来て」って言いますけど、待ち時間の発生メカニズムも曖昧なままで、原因は企業の管理レベルが低く、属人的なものだということなら「最大値が排除出来る」のに何年かかるんでしょうね。「生産性が低いのは管理レベルが低いからだ」って、30年前にも聞いたことがありますよ。まぁ、いいかっ。仮に、仮にですよ「最大値が排除できた」として、、、も、
「待ち時間が平均値付近に集中」するような分布はしないんですよ。そして、
「工程負荷が待ち時間の発生要因になっていないかの検討をします」ですかぁ。検討なんかする必要はありません。工程負荷と待ち時間の関係はすでに解明されていますから。(これも詳細は後述します)
そこではじめて製造能力の問題がでてきますが、・・・あくまでもここまでいくまでが大変だという話をしています。
「時間の最大値(異常値)」は「製造能力」と深くかかわっています。異常値の原因を分析するときも製造能力を無視できません。本間氏の説明の中では最大値の原因分析に製造能力の話はまったく出てきません。だから「最大値を排除」できるわけはないのですが、「最大値が排除できたら、そこではじめて製造能力の問題が出てくる、、、」となると、、、論理が崩壊していますね。 待ち時間の発生メカニズムについての理解がまったくないようですね。
今回のBlogの後半は、待ち時間発生のメカニズムに関する話になり、わかりづらくなってしまいました。しかし、ここが最重要ポイントになります。待ち時間発生のメカニズムは生産ラインの基本中の基本的な特性です。すべての生産ラインに、例えひとつの工程しかない生産ラインにでも、共通する特性です。
簡単に言えば、工程間(前)の待ち時間は、工程に到着する時間間隔と工程の処理時間(製造時間)で決まります。到着間隔と処理時間はバラツキます(変動します)ので、待ち時間もバラツキます。そのバラツキ具合が、われわれの常識と異なるんです。大きく異なるんです。だから、「先ず最大値を排除して、次に平均値の短縮、、という“当り前のアプローチ”」が機能しないんです。
本間峰一氏とのメールを題材にしておりますが、本間氏ひとりの問題ではありません。生産改善コンサルタント、生産スケジューラの開発者・ベンダー、関係する学界など、ほとんどの方々がこの生産ラインの基本的特性を理解していないようなのです。
1990年代に米国では、Factory Physicsが大学のプログラムに加わり、生産ラインの物理的特性の理解が進みました。2000年代後半には、ごく限られた条件でしか使えない生産スケジューラのほとんどは姿を消しました。日本では、生産スケジューラ・ベンダーが美辞麗句の誇大広告合戦を繰り広げております。日本の生産管理は30年遅れてしまいました。
本間峰一氏のメールにあったメッセージです。
最近日本のものづくりが危機状態にあるという話がよく出てくるようになりました。
生産ラインの特性を正しく理解することなく、大量生産時代には有効だったかもしれない「当り前のアプローチ」を、馬鹿の一つ覚えよろしく振り回す改善コンサルにも責任の一端があるのではないでしょうか。
次回から、生産工程間で発生する待ち時間について、物理的、工学的側面に重きを置いて検討してまいりたいと思います。