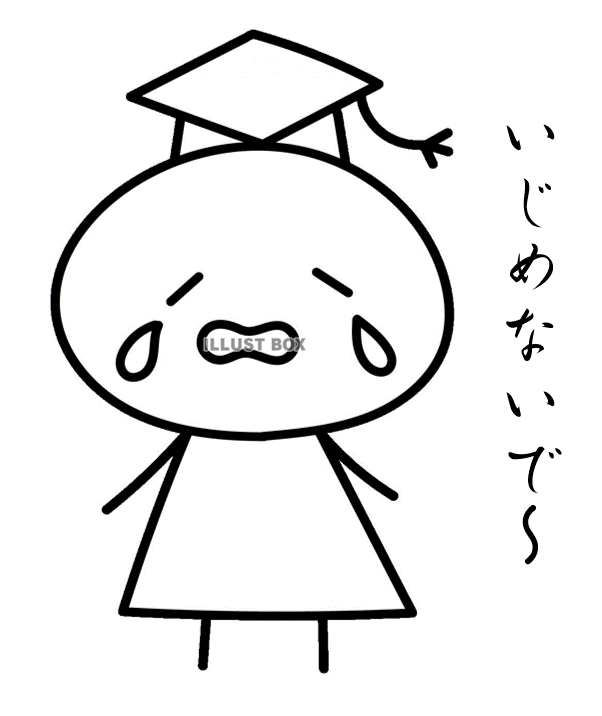
今回も、「在庫管理の基本と仕組みがよ~くわかる本」2019年4月発行の論評です。この書の主張の根幹みたいな部分に迫ってみたいと思います。それは何かといいますと、
“「必要なものを必要なときに必要なだけ」発注することができる不定期不定量発注法がお勧めだ”、
という主張です。本書からその主張の骨子を拾ってみます。
p.73
▶▶ 「必要なものを必要なときに必要なだけ」発注する
需要が変動するからこそ在庫管理が必要です。定期不定量発注では先の見通しは完全に読めないことから、担当者の思惑が入り込み、在庫の過剰や絞り込みすぎが問題になる可能性がありました。
不定期不定量発注法では、思惑が入り込む問題はあまり心配いりません。急に出荷が増えて在庫が減ってしまったら、慌てることなく発注すればよいだけです。逆に、出荷が減って在庫があまりがちという状況になれば、発注しなければよいのです。定期不定量発注法に比べて、発注担当者のストレスは少ないと言えそうです。
p.76
▶▶ 日数で換算する
—-「明日、出荷するために必要な量」を計算するためには、在庫の数量を「日数」に換算して判断します。まず、過去の出荷実績を日単位で収集します。—-2~3年、販売し続けるものであれば、過去1年程度の期間について出荷データを収集し、出荷があった日をベースに「1日あたり平均出荷量」を算出します。
p.76~77
▶▶ 需要の変動をみる
—-2~4週間程度の期間で平均出荷量を求め、出荷があるたびに、その時点から過去2~4週間の平均出荷量を求めるのです。——出荷があるたびに平均出荷量を求めるので、計算の対象が移動していきます。このような計算によって求められる平均値を移動平均といいます。—–
p.82
▶▶ 毎日「発注点チェック」を行う
発注のタイミングが来ているかどうかは、毎日、出荷があるたびに計算してチェックします。需要は変動するわけですから、いつ発注すべきか、状況は毎日変化する可能性があると考えるからです。これを「発注点チェック」と呼ぶことにしましょう。発注点チェックは、以下の手順で行います。
①出荷があるたびに「在庫量÷1日あたり平均出荷量=出荷対応日数」の計算を行う
②出荷対応日数とリードタイム日数+安全在庫日数を比較する
③出荷対応日数がリードタイム日数+安全在庫日数を下回ったら、発注する
不定期不定量発注法とは、発注タイミングも発注量も不定で、よく言えば、“適時適量発注”だが、悪く言えば、“行き当たりばったり発注”、と巷の評価は定まっていません。本書の主張は前者。本当に“適時”であり“適量”なのか。チェックしてみましょう。
本書が主張する不定期不定量発注法の基本的なメカニズムを一般的な不定期定量発注法(定量発注点法)との比較を通して調べてみます。簡単な条件で考えてみます。需要(出荷量)の母集団を
*1日あたり平均出荷量は10個、標準偏差は2個
の正規分布に従うとして、変わらないものとします。リードタイム日数は3日(固定)とします。
安全在庫は、安全係数を2として、
安全在庫
=安全係数×√リードタイム日数×1日当り出荷量標準偏差
=2×√3×2≅6.9
で、7個となり、発注点となる在庫数は、
発注点在庫数=平均出荷量+安全在庫=10(個/日)×3(日)+7(個)=37(個)
で、37個となります。定量発注量は60(個)としておきましょう。
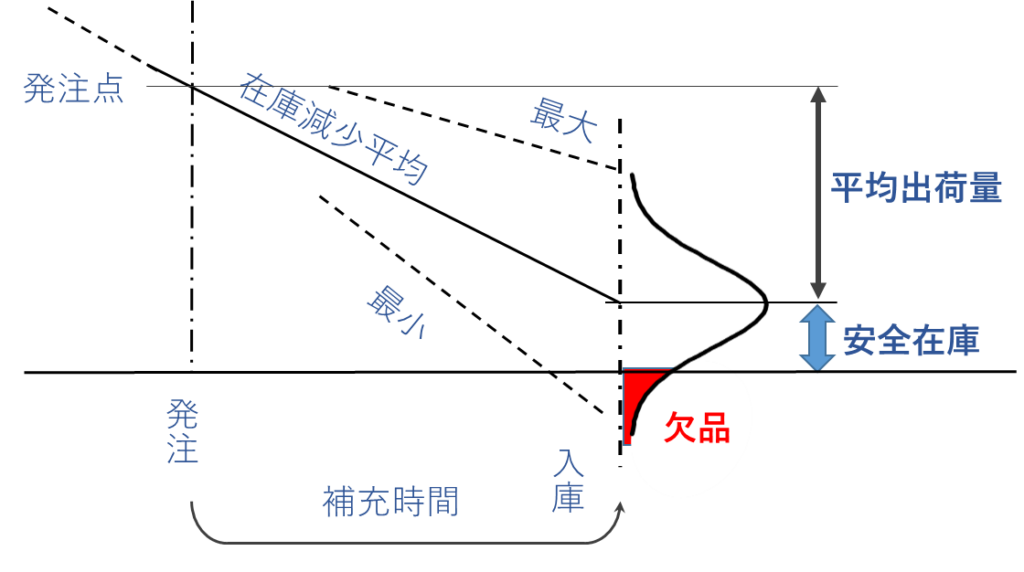
次に、本書が主張する不定期不定量発注法ではどうなるか、調べてみます。
先ず、“1日あたり平均出荷量”を計算します。本書の説明では何日間かの“移動平均”となっています。“移動平均”について、ちょっと、コメントしておきます。移動平均算出の日数をn日とすると、平均は母集団の平均と同じ、標準偏差は、母集団の標準偏差をσとすれば n÷√σとなります。
数値を入れてみましょう。母集団(1日あたり平均出荷量)の標準偏差は2個ですので、n=10の移動平均の標準偏差は、
2÷√10≅6.3 (個)
となります。 “1日あたり平均出荷量”が、2σでみれば、8.74(個)~11.26(個)の範囲にバラツクとみることもできます。「発注点チェック」をしてみます。
①出荷があるたびに「在庫量÷1日あたり平均出荷量=出荷対応日数」の計算を行う
①の計算に従えば、同じ“在庫量”でも“1日あたり平均出荷量”がバラツキますので、“出荷対応日数”もバラツクことになります。“出荷量の母集団は変わらない”という条件でも“出荷対応日数”が変動することにご留意ください。
②出荷対応日数とリードタイム日数+安全在庫日数を比較する
“安全在庫日数”は安全在庫を日数換算したもののようです。安全在庫は、先に計算したように7個ですから、切り上げて1日となるんでしょうか。“リードタイム日数”は3日ですから、“リードタイム日数+安全在庫日数”は4日。
③出荷対応日数がリードタイム日数+安全在庫日数を下回ったら、発注する
わかりやすいように、在庫量がどうなったとき発注するのか、という視点でみてみます。①~③から、次の式が導き出せます。
在庫量<(リードタイム日数+安全在庫日数)×1日当り平均出荷量
リードタイム日数;3日、安全在庫日数;1日、1日あたり平均出荷量は8.74(個/日)~11.26(個/日)を代入すると、
➡ 在庫量<35(個)~45(個)
つまり、発注点が35(個)~45(個)の範囲で変動することになります。一般的な発注点方式では発注点が37個で一定ですが、本書の主張する不定期不定量発注法では発注点がランダムに変動するということになります。
一般の不定期定量発注法は、発注量は予め決められています。本書が主張する不定期不定量発注法では、発注量は次のようになります。
P83
1日あたり平均出荷量×在庫日数=発注量
“在庫日数”は予め決めた日数ですが“1日あたり平均出荷量”が掛けられていますので、発注量も毎回変動することになります。定量発注量の60個を“在庫日数”に変換しますと、6日となり、発注量は、
6(日)×8.74(個/日)~6(日)×11.26(個/日)≅53(個)~68(個)
と変動することになります。
一般的な不定期定量発注法と不定期不定量発注法の比較をまとめますと、次のようになります。
不定期定量発注法 | 不定期不定量発注法 | |
発注点 | 37(個)一定 | 35(個)~45(個) |
発注量 | 60(個)一定 | 53(個)~68(個) |
不定期不定量発注法は、その名の通り、“発注点”も“発注量”も変動します。しかし、そのことによって、同じサービス率を保つための在庫量が増えてしまいます。“発注点”の変動は安全在庫を増やし、“発注量”の変動は在庫量を増やします。下図を参照ください。
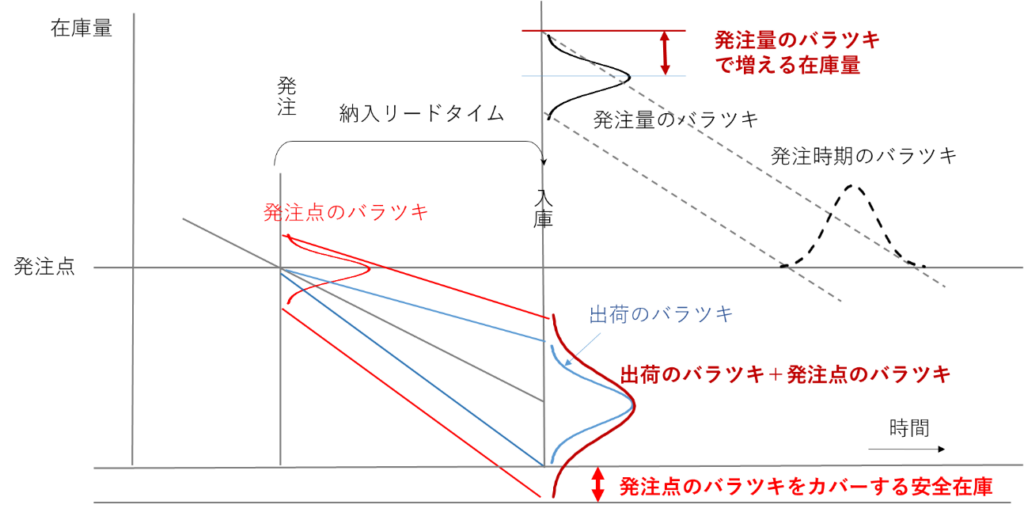
出荷があるごとに“1日あたり平均出荷量”を計算し、“その時の在庫量”を調べ、“出荷対応日数”を計算し、それを“リードタイム日数+安全在庫日数”と比較し、“出荷対応日数”が小さければ“1日あたり平均出荷量×在庫日数=発注量”を計算し“発注する”。
一方、一般的な不定期定量発注法は、在庫が発注点以下になったとき、予め決めた定量を発注する、これだけ。簡単です。
本書の主張する不定期不定量発注法。出荷ごとに毎回「発注点チェック」なる退屈な計算をして手間暇かけ、結果、在庫量が増える。一般的な不定期定量発注法と比べて、良いところはどこにも見当たりません。にもかかわらず、ご丁寧に、下記の説明まであります。筆者らは在庫管理の“専門家”?。レベルの低さに“唖然”とするしかありません。
p.67
▶▶ 定量発注法の特徴
不定期定量発注法のほうは、今後も使用するという会社はあるでしょう。ただし、需要の変動への対応力は低いと言わざるを得ません。発注時期を不定期にすることによって、多少、需要の変動に対応しているという程度です。
p.70
不定期定量発注法では欠品や過剰が起こりやすく、しかも、その状態にはなかなか気づくことができません。この方法をあまりお進めしない理由は、まさにそこにあります。適用するとしても、在庫品のすべてをこの方法で管理することは、危険なことといわざるを得ません。