前回は、「間欠需要」では在庫過多になるので、在庫を減らす方法として、
①出荷頻度を織り込んだ必要量計算を行う
②出荷頻度が落ちてきたら、出荷量の計算期間を延ばしていく
の2つがある、という説明。その真贋を調べてみました。②はまったくの“いかさま”。そちらに気を取られ、①についてはスルーしてしまいましたが、
5日間の必要量=1日あたり出荷予測×5日間の出荷日数予測
の式の
5日間の出荷日数予測
は、「出荷確率」を意味しているのではないか、ということに気が付きました。
「出荷確率」につきましては “ものづくり徒然草”の
No.87 安全在庫の計算;「出荷確率」を考慮するのはなぜ?
に愚見をサラッと載せてありますので、参考にご覧頂ければ、と思います。“出荷確率”という考え方も、実は、統計学を知らない素人が持ち出した“珍説”、、、のようでありまして。
さて、今回は何を取り上げましょうか。「在庫管理の基本と仕組みがよ~くわかる本」p.10~p.13にある 1-1 在庫実態を「見える化」する に注目してみましょう。(赤茶字部分は本書より抜粋)
▶▶「在庫散布図」で在庫の実態をみる
アイテム別に在庫の実態を把握するための有効な手法として「在庫散布図」があります。図1-1は、在庫散布図の一例を示しています。まず、在庫拠点を1ヶ所選んでください。次に、その拠点における以下の3つの数字を用意してください。必要なのは、その拠点に在庫してあるすべてのアイテムの数字です。
①アイテムごとの月間出荷量
②アイテムごとの月間出荷日数
③アイテムごとの月末在庫量
これらの数字が取れたら、以下の計算を行います。
④1日あたりの平均出荷量=月間出荷量(①)÷月間出荷日数(②)
⑤出荷対応日数=月末在庫量(③)÷1日あたり平均出荷量(④)
さて、ここまで計算できたら、⑤出荷対応日数と②月間出荷日数という2つの数字を使って、在庫散布図を作ります。図1-1を見てください。(本書の図とは異なるデータですが、イメージは似せてあります)
図1-1 在庫散布図
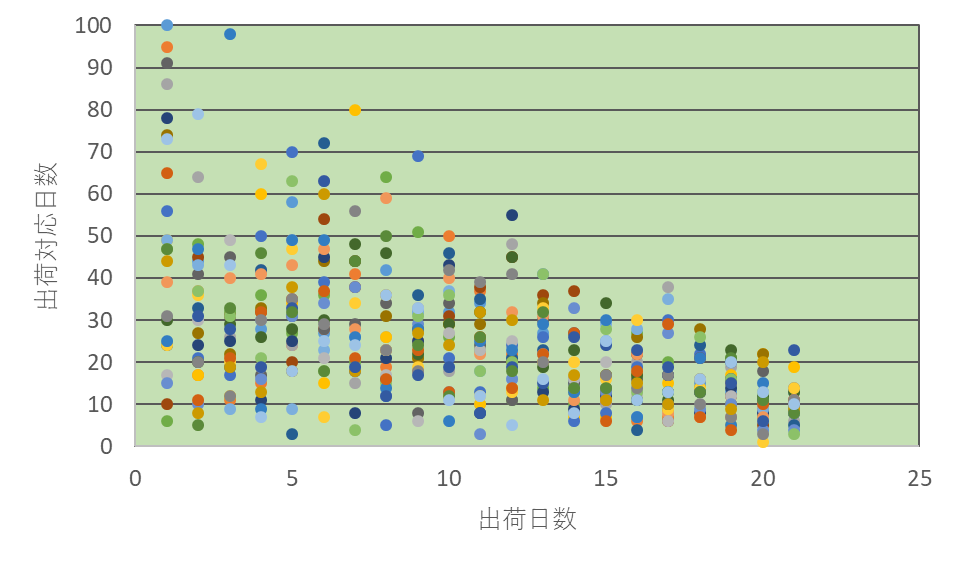
縦軸に「出荷対応日数」、横軸に「出荷日数」を取っています。出荷対応日数というのは、「今ある在庫で、あと何日分の出荷に対応できるか」という数字です。たとえば、出荷対応日数が10日なら、あと10日間の出荷に対応できるということになります。
横軸の出荷日数というのは、月間で何日出荷があったかということです。出荷日数の最大値は、その月の稼働日数になります。
在庫散布図へのプロットは、アイテム別に出荷対応日数と出荷日数がぶつかるところにマークをしていきます。
▶▶在庫散布図からわかること
図の左上の、出荷対応日数100日にプロットされているアイテムがあります。このアイテムは出荷日数が1日ですから、月に1回しか出荷がないということです。そして、今の出荷状況なら、今の在庫量はあと100日分あるということです。出荷が月1回ですから、実質100か月分の在庫だということです。
出荷対応日数が、0日に限りなく接近してプロットされているアイテムも少なくありません。これは、欠品の危険があります。在庫が少なすぎるのです。
この説明を読んでなんとなくわかったような気になられた方も多いのではないかと思います。月間出荷量、月間出荷日数、月末在庫量から出荷対応日数を計算し、出荷対応日数で在庫量の適正さを判断するということなんですが、、。
でも、ですね、、。きちんと調べてみると、欠陥だらけで、使いものにはなりません。その理由のいくつかを上げますと、、
[1] 図1-1をご覧ください。出荷日数が0(グラフの一番左端)には出荷対応日数のプロットはありません。月間出荷日数が0だと分母が0となるため、1日あたり平均出荷量の計算ができないんですよね。だから出荷対応日数も計算できない。でも、現実には2~3カ月に1回しか出荷がないとか、半年に1回の出荷とかいうアイテムって、たくさんありますよ。「出荷がないのに在庫がある」。これって、在庫管理では忌々しき状態なんですがね。それを無視しちゃってんじゃないでしょうか。 [2] 在庫量は出荷時に減少し、入庫時に増加して変動する。ですから在庫量を捉えるためには変動の範囲を捉えなきゃいけません。一般的には、平均とか分散、最少、最大などで変動範囲をつかまえます。月末とかの一時期のデータだけではとらえられませんよね。さらに、経理では月末の在庫残高をみますから、それをできるだけ少なくしようとして、月末出荷推奨・月末入庫抑制に走る、などの影響があって、ますます乱高下するわけです。月末在庫量だけで在庫量全体のバラツキを捉えることはできませんね。 [3] ①~⑤の式をみても、補充発注から入庫までの調達リードタイム(納入リードタイム)をまったく考慮していませんね。在庫量を決定する最も重要な要素ですよ、調達リードタイムは。原理的に破綻してますね。 [4] 調達リードタイム>発注間隔のとき、必ず発注残が生じます。前に発注したものが入庫される前に次の発注が行われますので、前に発注したものは発注残状態になる。在庫管理では“常識”。しかし、①~⑤の式の中に発注残はなし。これだと在庫循環のメカニズムを正しく捉えることができませんので、間違った判断を助長することになります。 [5] 需要は受注件数(出荷件数)と1件当りの受注数量(出荷数量)で決まります。受注即出荷とすれば、出荷日数は需要に対して従属的に決まります。“出荷件数”と“出荷日数”は、在庫循環のメカニズムの中では、全然違うんです。例えば、出荷可能日数28日のとき、出荷日数と出荷件数との関係は図1-2のようになります。直線的な関係ならまだしも、非直線的な関係なので、在庫量の計算に出荷日数を使うと間違った答えが出てきます。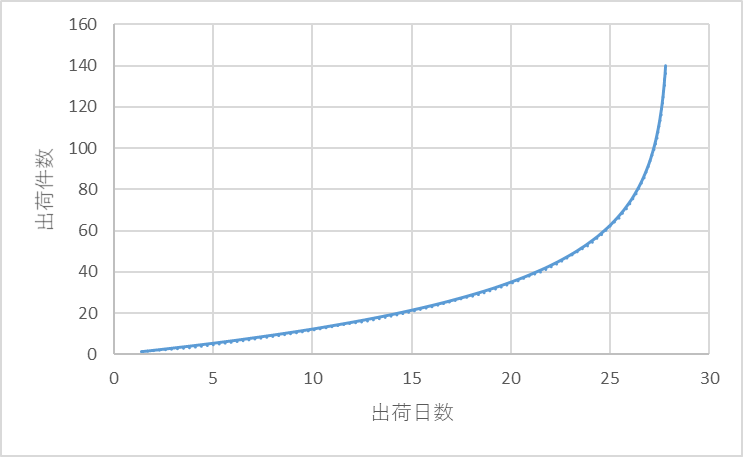
図1-2 出荷日数と出荷件数の関係の一例
在庫管理では、[1]~[5]はいずれも致命的な欠陥です。これで“在庫実態を「見える化」する”ことができるのでしょうか? 見えたとしても、“虚像”か“歪曲された像”しか見えないのでは、、。