先だって、近くの本屋さんで、“工場管理2018年8月号の[特集1]“をパラパラと立ち読みしました。「おー、これは、、」と思い、家でじっくり読むことに、、。
“[特集1]なぜ納期遅れが起きるのか 生産管理システム活用の盲点“ 解説1~6、執筆者;本間 峰一
この記事、変に、おもしろい。日本の生産管理システムの弱点がズバリ、わかります。ただ読んだだけではわかりません。生産ラインの基本特性についての予備知識が必要です。具体的な事例で、先ずは、予習兼準備体操から、、。
[事例]
ある受注生産をしている企業がある。受注が確定したら生産開始。生産リードタイムは10日。どんな注文でも10日、ピッタシ。この工場は同時に1台しか製造できない。1台完成したら次の注文に取り掛かかる。注文はランダムに舞い込む。注文が多くなると投入口で待つことになる。製造は受注順に行う。
投入待ちの注文がない時は、納期は10日。納期遵守率100%です。注文が増え、投入待ちの注文がある時はどうなるか。とりあえず知りたいのは受注してから完成するまでの時間です。注文が増えれば納期も延びるんじゃないか、ということは経験的に分かりますが、ではどのくらい?
実は、この問題を解くのにちょうどよい計算式があります。待ち行列理論にM/D/1モデルというのがあります。Mは注文の到着時間間隔の分布が指数分布、Dは処理時間が一定、1は処理工程がひとつ、という意味です。受注してから完成までの平均時間は次のようになります。
受注~完成までの平均時間=製造時間+待ち時間
製造時間は10日で一定ですので、待ち時間に注目します。待ち時間の計算式は次のようになっています。
平均待ち時間=ρ/(2μ・(1-ρ))
λ;平均到着率(受注件数/単位時間)
μ;平均サービス率(処理数/単位時間)
ρ=λ/μ(稼働率)
事例の数値;μ=1台/10日 で、注文の到着率を振って稼働率を変えたとき、平均待ち時間がどうなるか、計算した結果の一例を図1に示します。
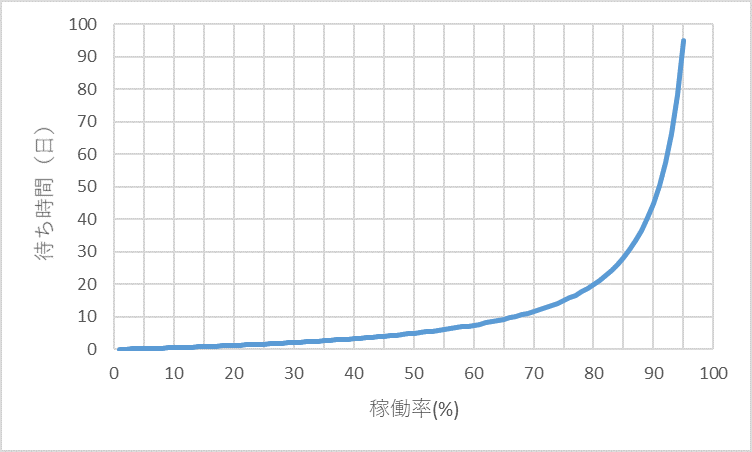
図1 待ち時間の一例
製造時間は稼働率に関係なく10日で、一定ですので、受注~完成までの平均時間はほとんど、待ち時間によって特徴づけられます。図1をみてわかるように、稼働率が80%を超えるあたりから急激に待ち時間が長くなります。この現象を“待ち時間の跳ね上り”と呼んでおきます。
こうなる原因は何か。製造工程ではきちんと10日で生産しています。にもかかわらず、稼働率が高くなると、受注~完成の平均時間は、100日を超えてしまいます。この原因は、需要の変動です。需要の変動は生産工程の外、工場内ではどうすることもできません。
待ち行列理論の数式では平均値しか計算できません。どんな分布で、最大値はどのぐらいなんでしょうね。計算式では求められませんので、シミュレーションで確かめてみます。
シミュレーション結果の一例を図2に示します。稼働率95%では最大の待ち時間は300日を超えてしまいます。

図2 待ち時間のシミュレーション結果の一例(生産台数5,000台)
稼働率95%のときの待ち時間の分布の一例を図3にし召します。ダラダラとすそ野を引いていることが分かります。赤棒は待ち時間ゼロの確率(約6%)です。
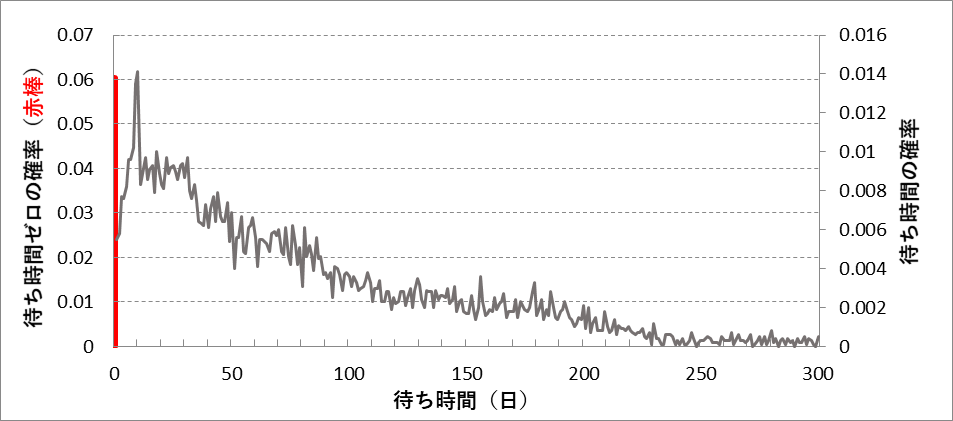
図3 稼働率95%のときの待ち時間の分布の一例
図4は待ち時間の時系列変動(生産台数1000台まで)を示したものです。待ち時間は0日~200日の範囲で不規則に変動しています。
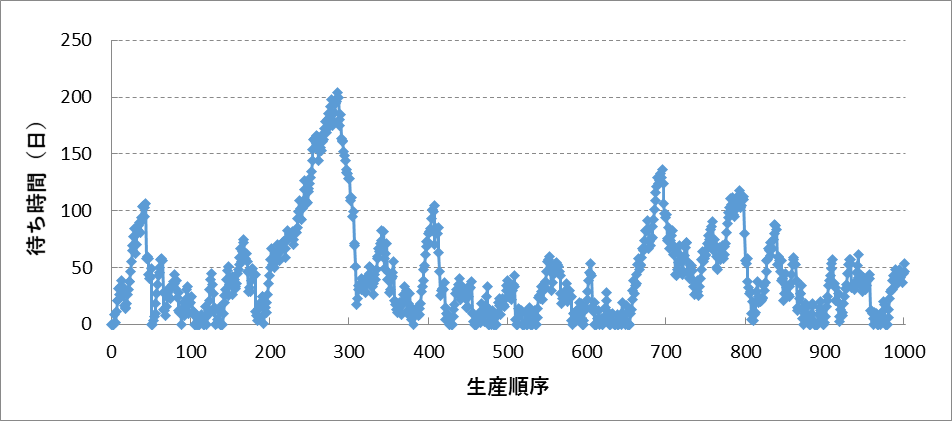
図4 待ち時間の時系列変動
事例の工場はひとつの工程とみることができます。複数の工程が直列、並列に連なって生産ラインとなり、生産ラインが連なって工場となり、サプライチェーンを形成します。事例は、生産ラインの最少構成単位がどのような特性を持っているかを示しています。
1工程で起きる待ち時間の跳ね上りは、程度の差はあっても、どの工程でも起きます。1工程の完成時間間隔は次工程の投入時間間隔となり、処理能力との関係で待ち時間はバラツキます。生産ラインの投入から完成までの各工程の待ち時間がバラツけば、工程を通過する時間もバラツクことはお分かりいただけると思います。
生産ラインのこのような特性は、不特定多数の変動要因によって引き起こされます。外部の変動要因もあれば企業内の変動要因もあります。この事例では、企業内の変動はなし、変動要因は注文到着時間間隔のバラツキだけですが、このような企業外(市場)の変動は企業側ではどうすることもできず、受け入れるしかありません。
実際の生産ラインは複数の工程の連鎖からなります。さらに様々な企業内の変動要因が加わりますので特性はもっと複雑に、待ち時間の跳ね上がりもさらに激しくなると考えられます。
生産ラインの基本特性をまとめてみますと、
- 待ち時間は、稼働率(負荷率)が80%ぐらいから急激に長くなる(待ち時間の跳ね上り)
- 企業内の変動がゼロでも、需要の変動(受注の時間間隔の変動)だけで待ち時間の跳ね上りが起きる
- 待ち時間の分布は滑り台状に時間の長い方向にすそ野を引く
- 時系列でみると、待ち時間は不規則にバラツク
- 待ち時間の跳ね上りは、複数の工程が連鎖する離散型生産ライン、さらにはサプライチェーンを構成するあらゆる基本ユニットで起きる。
- 生産ラインへの投入から完成までの経過時間を定めることは、極めて困難である。
- 指定された時刻で生産することは、ほぼ不可能である。
この知見を頭に入れておいて、件(くだん)の特集記事の解説に目を通してみます。気にとまった文章を抜き出してみます。(記事からの引用部分は色を変えてあります)
① “人手不足により納期遅れ対策が重要になってきた”
解説では、実需増や能力不足によって納期遅れが起きる、と説明しています。経験的、直観的に、ひっかかりなくスーッと受け入れる方が大部分だと思いますが、少々鋭く穿ってみましょう。予習した生産ラインの基本特性、図1をご覧ください。負荷率が80%以上の領域では、負荷率がちょっと上がっただけで、待ち時間はグーンと長くなります。待ち時間は、バラツキが大きく且つ不規則に変動します。生産完成の時期を予測することは極めて困難となります。だから、納期遅れが激しくなる、というわけですね。実需増に対して先行手配をするとか、内示数を積み上げるから納期が読めなくなる、とか、残業規制の強化、パート賃金上限問題による人手不足が要因だ、などの説明がありますが、なくてもいいとは言いませんが、本質ではないと思います。
② “製造指示にはどう対応しているのか、製造指示通りのリードタイムで製造できているのか”
解説によると、製造開始時刻と製造所要時間が指示され、その通りに製造を行うことが生産管理の基本だ、と。しかし、実態は、緻密な生産計画をつくっても計画通り生産できない、とか、進捗情報があっても納期通りできるかどうかわからない、といった状況だ、と。その根本原因には触れられないまま、解決策は、生産スケジューラーの導入と流動数曲線の利用だ、と説明しているんですが、、。
先ず、緻密な計画をつくることができるのかどうか、を検証してみましょう。待ち時間の跳ね上り現象をもう一度、ご覧ください。事例では1工程、処理時間一定の条件ですが、実際は、処理時間も変動しますし、生産ラインは直列、並列に複数の工程がつながります。1工程で起きる待ち時間の跳ね上りは、程度の差はあっても、どの工程でも起きます。1工程の完成時間間隔は次工程の投入時間間隔となり、処理能力との関係で待ち時間はバラツキます。つまり、生産ラインの投入から完成までの各工程の通過時間は大きくバラツクことがお分かりいただけると思います。このような特性を持つ生産ラインで、工程ごとの通過時間を緻密に、正確に決めることはできるでしょうか。「えいっ、やっ」、と決めたとしても、その通り生産をすることはできるでしょうか。管理レベルを上げたらできるでしょうか? 生産スケジューラーを導入したらできるでしょうか? 流動数曲線を利用したらできるでしょうか?
生産管理システムのスタンスは、生産ラインの基本特性からみれば、物理的に不可能なことを前提にしていることになりませんか。
③ “納期遅れ問題を解消するための基本は、現在の生産が正しい納期設定通りに生産されているかどうかの進捗監視である”
②で述べましたように、各工程の通過時間を予め決めることは不可能に近いことです。ですから「正しい納期設定」もできません。というと、異論が聞こえてきそうなので、コメントしておきます。「正しい納期設定」が可能な条件があります。生産計画固定、変動が極小(3%以下)、同期生産、、、このような生産環境では、生産ラインの特性は、すごく単純になります。詳細は前回のBlog“生産ラインの基本特性;投入負荷と処理能力”をご覧ください。生産計画固定ということは、事例でみた需要の変動を遮断することを意味します。あとは工程内のバラツキを小さくすれば、生産ラインの特性はすごくシンプルになります。この状態であれば、実用的な範囲で、正しい納期設定もできますし、進捗監視もできます。卑近な例はトヨタ生産方式ですね。
ところが、需要変動を受け入れざるを得ない生産環境では、事例で示した生産ラインの基本特性を無視することはできません。生産管理システムには、納期設定と進捗監視が必要だ、というのはその通りです。しかし、生産ラインの基本特性を無視した納期設定、進捗監視は物理的に成り立たない、ということを申し上げたいわけです。
④ “生産理論を知らない生産管理担当者;生産管理の活用目的や生産管理理論を勉強せずに、コンピュータや製造現場に振り回されている生産管理担当者が増えている”
現在の生産理論は、生産計画を固定し、需要変動を遮断することを条件に成り立っている、と考えられます。そのような条件の生産管理であれば、現行の生産管理理論を勉強する意味はあると思います。しかし、そうでない業種、企業の方が圧倒的に多いわけです。生産管理の問題の多くは、生産計画を固定できない企業や業種で起きているのではないでしょうか。
生産ラインの基本特性を無視した現行の生産管理論は破綻している、といっても過言ではありません。機能しない生産管理論を学んでも、コンピュータや製造現場に振り回されている状況が改善されることもなく、悶々とした日々が続くだけではないか、と危惧するわけです。
⑤ “生産管理システムは、使う人がマスタに魂を入れないと役に立たない”
あれもダメ、これもダメ。八方ふさがりで、今度は「魂」ですか。精神論に逃げ込んでも救われないと思いますが、、。
⑥ “滞留時間を短くする”
待ち時間の主なものは①正味製造時間、②ワーク待ち時間、③工程待ち時間、④運搬時間、⑤段取り時間、⑥バッファー時間。
発生原因は、購入品の調達が間に合わない、部品合流が同期化していない、製造設備の能力不足、設備の固定化・偏在化、設備故障、オペレータや治具の不足、、、。
これらの大部分は企業内で観察される事象。だから企業で対策できるかというとそうではありません。これらの滞留時間の根本原因は需要のバラツキです。需要の変動がある限りこれらの待ち時間を無くすことはできません。ここでも生産ラインの基本特性が無視されています。
その他にも取り上げたいところはたくさんありますが、まぁ、こんなところにしておきます。
この特集記事、
“[特集1]なぜ納期遅れが起きるのか 生産管理システム活用の盲点“ 解説1~6
興味のある方は、原文をお読みください。ザックリとまとめると、“生産ラインの基本特性を無視した生産管理システム活用の解説”。“生産ラインの基本特性;待ち時間の跳ね上り”は執筆者の目には入っていないようで、解説の中にはまったく出てきません。“群盲象を評す”かな。群盲の日常会話を多少わかりやすく羅列しただけ。でも、「盲点」に触れずに「盲点」を描きたかったのだとしたら、、絶妙な表題ですね。
中身はどうでしょう。お粗末そのものです。MRPもダメ、CRPもダメ。生産スケジューラーが解決策の一つだ、といいながらAPSの本格活用はまだ、、の原因も言い訳的なものばかりでうにゃむにゃ。的をはずしたこの特集の解説、解決の方向性を示すことがないばかりでなく、生産管理システム関連に携わる方々へ間違ったメッセージを発信しているのではないでしょうか。そして、この記事が日本の生産管理システムを支える専門家、専門誌のレベルを示していると考えると、底知れぬ寒気を感じてしまいます。
記録的な猛暑が続く今夏に合わせて組んだのだとすれば、時宜を得た特集記事であった、、のかもしれませんが、、。
-暑中および残暑見舞いに代えて-